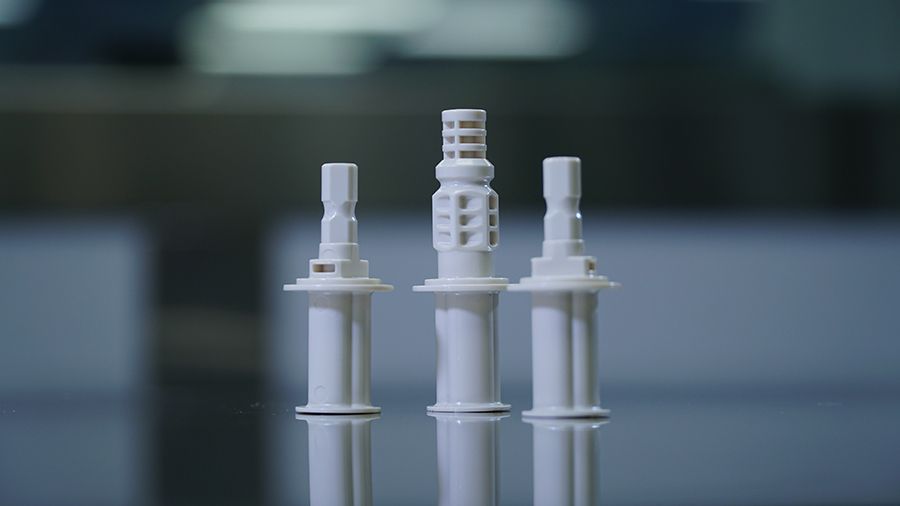
Injection Molding of Threads and Undercuts for Plastic Components
(Updated May 2019)
Threads and undercuts in plastic injection molded components require some special considerations and methods for manufacturing.
What is a threaded plastic component?
Threads in a plastic component allow for fastening of your plastic part to another plastic part or to a non-plastic part by using common fasteners. Plastic components can have threads on the external side or internally. External threads can be modified so that they can be molded without any special mold actions. Internal threads are more complex and require a rotating core that unscrews from the part. Material selection for internal threads is important as some polymers may “stick” and make it difficult to unscrew the part, especially glass-filled or high temperature materials.
Unscrewing molds are used for plastic parts that have threads or ridges that cannot be easily injected using the standard knockout method. In these molds, the parts are unscrewed from the mold to avoid thread damage. Unscrewing-molds remain the most complex of all injection molds and need to move at high speeds and clear previously molded parts efficiently in order to begin the next cycle.
They require tremendous technical savvy to build, then maintain. They are designed for many years of production, which is why they are considered a long-term investment when producing high-volume parts. Regarding their design, threaded parts adhere to the same injection mold design best practices as other parts. For example, when possible threaded parts should use draft, maintain uniform wall thickness, and avoid sharp corners or bends.
What is an Undercut in Injection Molding?
An undercut feature is any indentation or protrusion that cannot be removed from the mold in the direction of the mold opening. Undercuts are common in the medical industry, and are often found in parts that have snap and latch features, or holes for wiring.
These features inhibit the direct removal of the core and as a result, necessitate using an additional mold component such as a side core or internal core lifter to form the shape. Smaller undercuts can be removed from a mold without these devices if the part is free to stretch or compress around the undercut. In these cases, the wall of the part opposite the undercut must clear the mold or core before ejection is attempted.
Whenever there are undercuts, mold devices such as actions can be used. An action is mold-tooling that travels in a direction perpendicular to the direction of the mold opening. The undercut portion of the part is molded by the action, which moves away from the part as the mold opens.
Other mold devices can be used on parts with undercuts, such as lifters and collapsing tooling. Lifters are frequently used when a segmented plastic undercut is necessary. A lifter is a component in the mold that is normally attached to and actuated by the ejector system and moves at an angle to free internal molding details. They are typically attached between the ejector retainer and ejector plates with a mechanism that allows the fixed end to slide or pivot to compensate for the movement of the lifter position as it moves at the desired angle. This angle is critical for two reasons; first, if the angle is too great - the forward motion of the ejector system would put too much pressure against the lifter body. This pressure would create binding of the lifter and lead to excessive wear or premature failure. Second, if the angle is too shallow, the ejector plate travel would be excessive - therefore careful engineering and good expertise has to be engaged.
Some minor redesigns can save the use of actions and lifters which saves money, especially in the case of clips and catches. These are often used to assemble the plastic parts. Sometimes a design modification - like a hole in the part - will allow for the catch to be formed without the use of actions or lifters.
When designing parts with undercuts, sufficient draft should be added to ensure the part can be more easily removed. Additionally, you want to provide sufficient space so any supplemental tooling such as actions or lifters can move freely without obstruction. Lastly, select a material that is undercut-friendly and is not challenging to pull from the mold.
When working with threads or undercuts, work with your molding partner to perform a DFM analysis to model the part, tweaking the design as necessary to resolve any potential issues and improve its manufacturability. At Crescent Industries, our engineers use their knowledge as injection molders and mold builders when producing part designs and mold designs for our customers.
For additional information, please click below to get our white paper “How to Overcome Common Design Concerns for Injection Molded Components”. This white paper addresses some of the key concerns in the design step that are a 'must' to consider.
Topics:
Related Articles
-
Mar 19, 2025
Top 6 Advantages of Injection Molding for Your Project
Injection molding — the process of injecting molten resin into a mold — is one of the most...
-
Feb 19, 2025
Injection Molding vs CNC Machining: Which Method to Choose?
Every year, humans produce and use countless plastic products in various shapes, sizes, and...
-
Oct 03, 2024
Injection Molding Uses: Exploring Applications Across Industries
Injection molding is one of the most versatile manufacturing processes, with a wide range of...