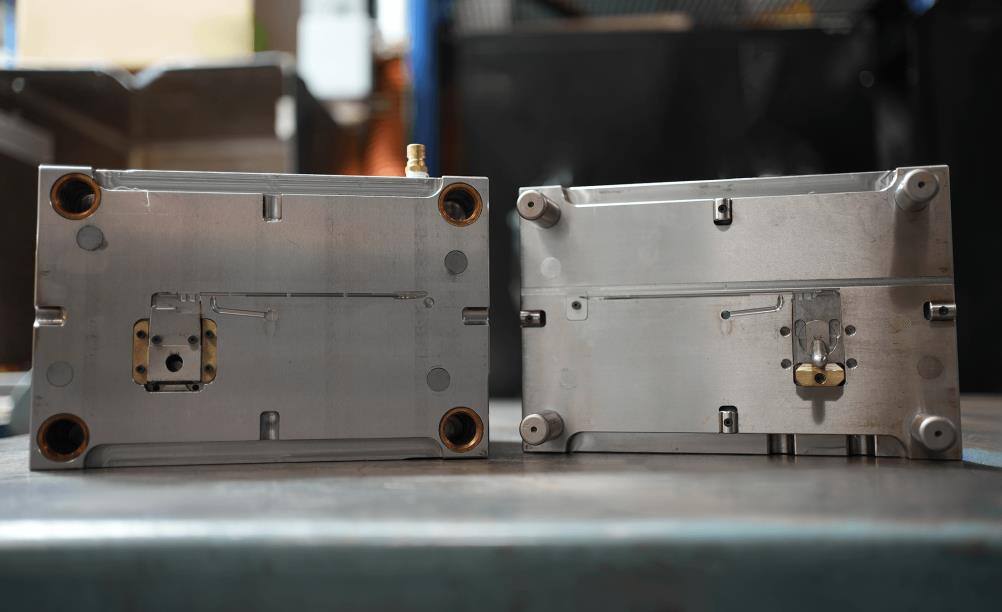
Benefits of In-House Tooling Capabilities
Updated March 2025
Tooling engineers review the designs of injection molded parts and consider their practical limitations before translating the design into a custom mold. The tooling process is critical in any custom injection molding project and must be addressed. However, physically manufacturing that mold can be a challenge.
Why You Should Consider A Molding Partner with In-House Tooling Capabilities
In-house tool design and mold building provide various benefits in the injection molding process that don’t have to rely on outsourcing or other factors. Having injection mold tools produced under one roof from start to finish enables unified project management, improving the final product's quality.
Customize Precisely to Project Needs
Relying on a single injection molding partner for the entire process, including upfront engineering, mold design, tooling, and beyond, ensures that the result meets your unique project needs. The direct line of contact between your team and everyone involved in producing your plastic components or devices ensures key objectives are held at the forefront of every decision. Any potential practical difficulties in tooling can be addressed as soon as possible without any disruption in communication. You stay informed and involved throughout the entire project.
Enhance Quality and Consistency
Custom tools improve quality and consistency in injection molding. The cohesive oversight over the entire process ensures that any mold design is made with practical injection molding constraints in mind. Instead of discovering issues when the molds are already built or returned from an overseas shop, you'll be notified of any potential issues or defects upfront before the steel is cut.
Quality control is applied throughout the entire process rather than simply as a check at the end. In-house tooling allows in-depth inspections and evaluations when creating injection molds, keeping quality and consistency high.
This approach to injection mold tooling ensures that all components are crafted to the highest standards and work together correctly. You can ensure that all parts involved, including the cavity, core, sprue, runners, gates, and more, are designed and fabricated for reliable injection molding production.
Reduce Costs and Increase Efficiency
At first glance, going with in-house tooling from a domestic shop would increase your costs. However, this is only true for the initial investment. Undoubtedly, quality and expertise carry a certain price tag, but the cost savings over entire injection molding production runs can be considerable.
In-house molding ensures that your molds are built to spec and are ready to go immediately. You won’t face downtime and increased maintenance costs due to low-quality tooling, which creates production issues. The quality of tooling shows itself in the consistency of the parts you manufacture, reducing reject rates, and eliminating at risk production runs.
Partnering with a shop that offers in-house tooling can also open the door to innovative mold designs to achieve your specific product requirements. Options such as master unit dies can further reduce injection mold costs by avoiding the need for a dedicated mold base and minimizing tooling requirements using standardized inserts that fit into a frame.
Accelerate Market Responsiveness
Many industries that rely on injection molding as their manufacturing technology face incredibly turbulent market demands. When market trends strike, manufacturers must be ready to get new parts to market as soon as possible. A tooling process that relies on external back and forth is too slow. Handling tooling in-house alongside of the production makes an accelerated timeline possible.
Not only is coordination much faster, but the tooling process can deliver results sooner when the right equipment is available. Shops with in-house tooling can invest in advanced machining capabilities such as high-speed CNC mills that enable faster cutting, surface grinders, and other operations.
Streamline Communication and Workflow
When engineers, designers, toolmakers, and inspectors work in the same facility, communication is streamlined throughout mold production and process development. This improved communication makes mold production faster and more accurate, as issues can be identified and dealt with quickly rather than requiring extensive back-and-forth.
Relying on a third-party toolmaker inhibits communication between the designer, toolmaker, and injection molder leading to important details being lost in translation. Handling tooling in-house eliminates these issues. The workflow is laid out by the shop itself, without worrying about the communication barriers and delays introduced by coordinating with third parties. Your mold production benefits from the direct time savings of having every step physically under one roof, alongside savings due to improved collaboration.
Optimize Flexibility and Innovation
In-house tooling unlocks significant flexibility and innovation in mold production. When working with external toolmakers, shops need to be more extensive in the scope of their tooling options. Relying on experienced in-house toolmakers who work closely with designers allows for constantly exploring new techniques, methods, and tools.
The shop can then put those innovations to work for your injection molding production project. They can take on more ambitious projects that deliver quality results. Highly refined in-house tooling processes improve the speed and quality of the results you receive.
Use Our Experience for Complete Manufacturing Solutions
Commissioning an in-house toolmaker to manufacture your injection molded parts can be the difference between success and failure for your project. Working with a shop that implements custom tooling into its mold production processes can save you time while preventing serious quality issues.
With more than 75 years spent delivering manufacturing solutions, including plastic injection molding tooling design, Crescent Industries is the company to take on your next project. Our full-service shop handles the design process, in-house tooling, mold testing, and more, all right here in the USA. Contact our team today to find the solution for your manufacturing needs.
Topics:
Related Articles
-
Apr 10, 2025
How Are Injection Molds Made for Plastic Manufacturing?
Do you have a part design and need an injection mold built? Are you interested in finding a tooling...
-
Sep 06, 2023
What is Plastic Injection Mold Tooling?
Injection mold design gives you the ability to create parts with ease. You fill a mold designed to...
-
Nov 16, 2022
Project Management for Injection Molding Means Product Success
There’s a difference between project management and engineering management, and in the field of...