Injection Mold Tooling
What you need to know about Injection Mold Tooling
Are you looking to get the most from injection mold tooling design? Do you need to manage the total cost of ownership and ensure seamless integration between tooling and production? Understanding the process and how to manage lead times can heavily impact your final product. Additionally, key considerations such as effective design and well-chosen materials can drive efficient, high-quality outcomes that support long-term manufacturing success.
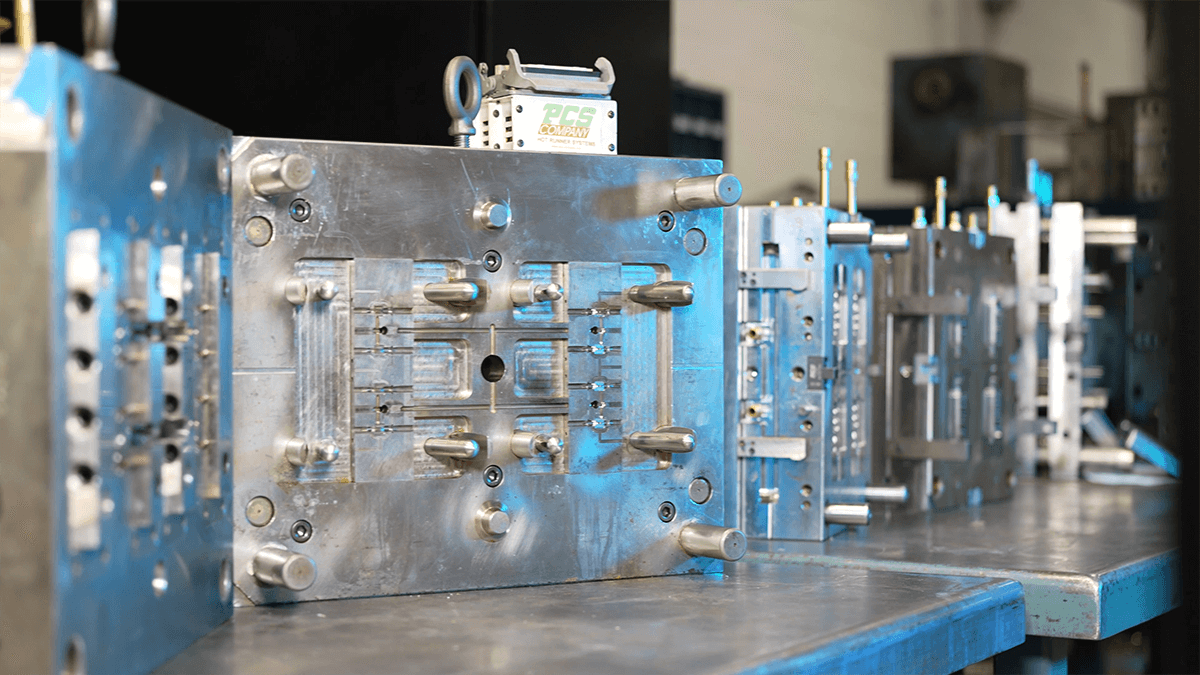
What Is the Injection Mold Tooling Process?
Understanding of the critical path activities in the mold manufacturing timeline is pivotal. The stages of a new injection mold build typically include:
- Kickoff: Initial project launch where goals, timelines, and specifications are defined.
- Design for Manufacturing (DFM) & Design: This phase involves refining the mold design to ensure it meets all requirements and is optimized for manufacturing.
- Mold Build: The physical construction of the mold, which includes machining, assembly, and initial testing.
- Sampling and Operational Qualification (OQ): Initial testing of the mold to verify that it produces parts that meet the specified quality standards.
- Production Qualification (PQ) Lot to Production: Final validation and full-scale production readiness, ensuring the mold can consistently produce parts at the required volume and quality.
By effectively managing these stages, process and lead times can be optimized, ensuring that the project stays on schedule and within budget.
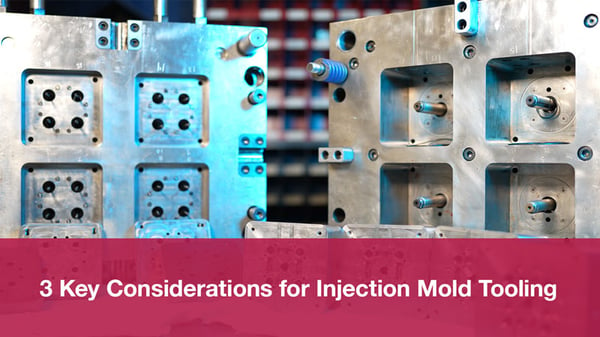
Key Design and Material Considerations
The choices made during the design phase and the materials selected for your mold tool can significantly impact not only the overall cost but also the efficiency and longevity of the tooling. During design and material selection, consider a variety of factors:
- The Part Being Molded: The primary driver for determining a mold tool’s design is the part being molded and whether the part design is injection moldable. Some part designs are injection moldable as delivered, while others require modifications to ensure manufacturability without altering the part’s form, fit, or function. These types of modifications may require specific materials or design choices to ensure a successful outcome, or value engineering of the product itself to enhance manufacturability.
- Material Selection: Tool steel selection is guided by factors such as production volume, the resin used in the molding process, and specific tool features.
- Managing Parting Lines and Weld Lines: Parting lines and weld lines are unavoidable aspects of injection molding. These lines typically do not affect the part’s structural integrity but can be visually apparent. Mold designers can employ various techniques to minimize their appearance, but complete elimination of these lines is impossible.
- Utilizing Mold Flow Simulation: Mold flow simulation is an essential process providing insights into how the mold will fill and pack. Simulation allows for making adjustments before the mold is fabricated, reducing the risk of costly revisions and ensuring optimal part quality.
- The Role of Material Properties: The properties of the materials used in both the mold tool and the resin greatly influence the molding process. Additionally, material shrinkage must be carefully accounted for during the design phase, with the mold cavity being slightly oversized to compensate for the expected shrinkage during cooling.
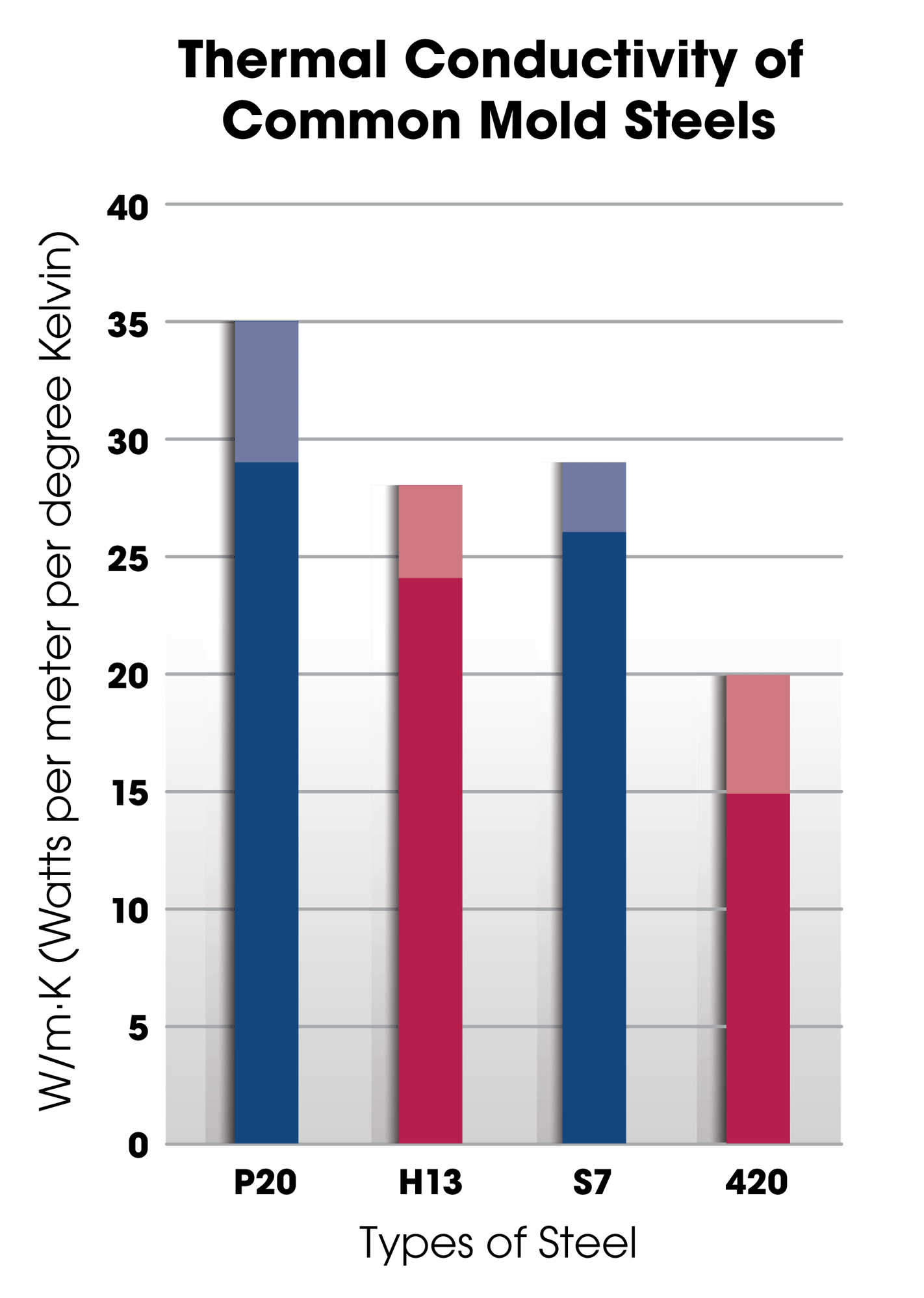
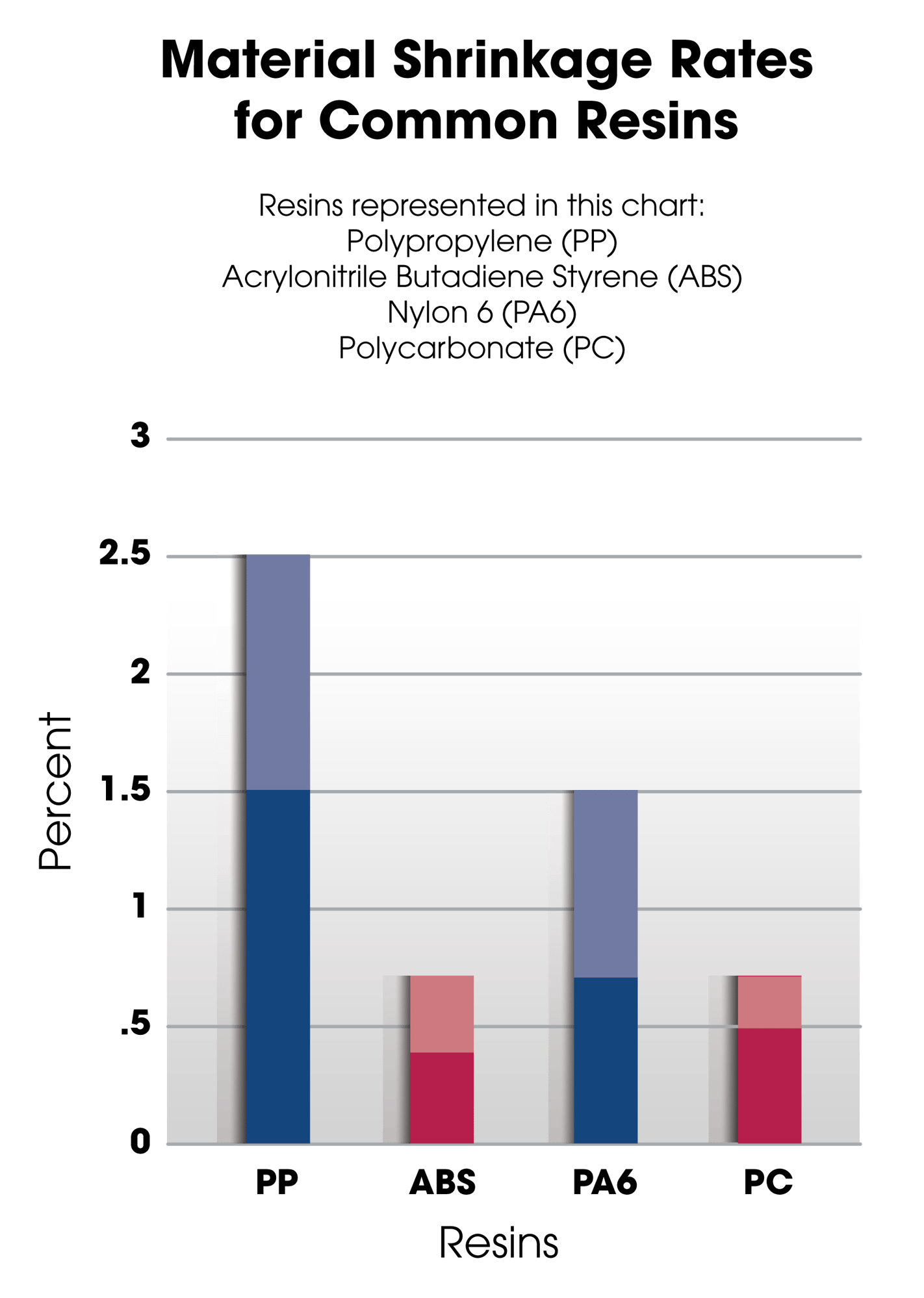
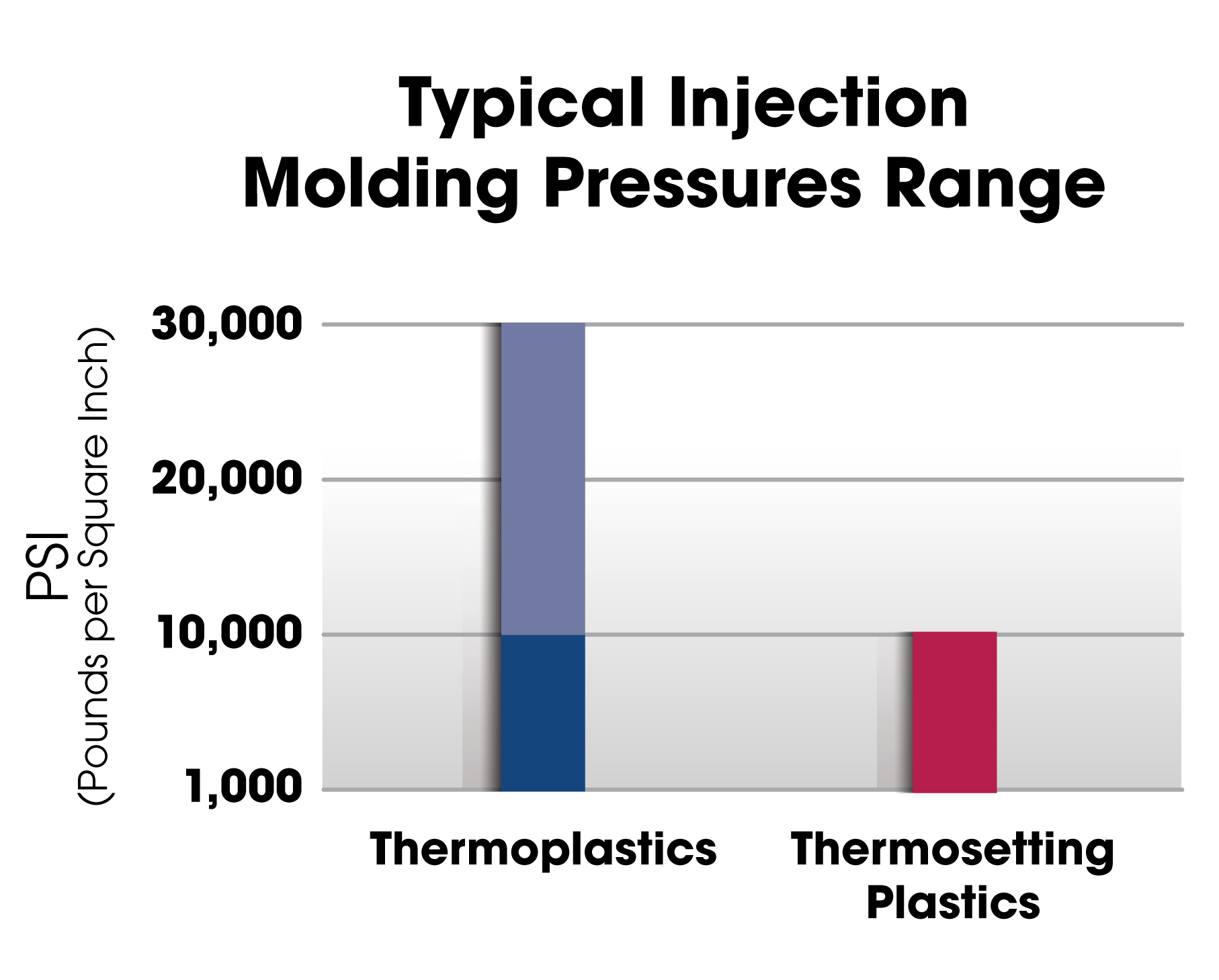
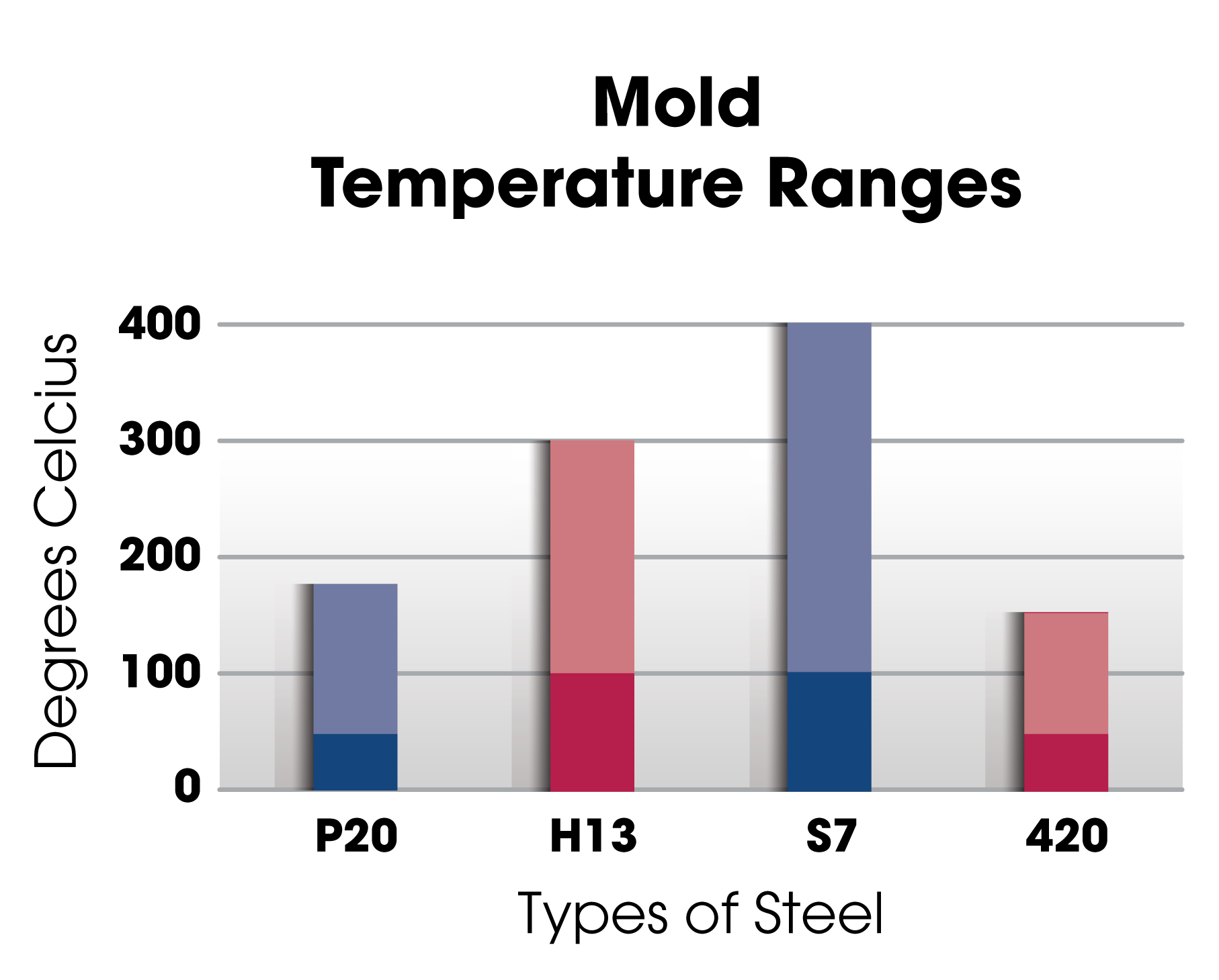
Once the design and materials are determined you will need to be aware of other technical factors that play critical roles in determining both the functionality and manufacturing effectiveness of injection mold tooling. These factors can be leveraged for achieving cost and efficiency goals.
HOW TO GET THE MOST FROM INJECTION MOLD TOOLING
Successful injection mold tooling is essential to meeting your project goals and executing your carefully considered strategies. To get the most from injection mold tooling there are three areas that impact your bottom line, inform your decisions, and improve your outcome. These include technical, cost, and operational considerations.
Technical Considerations
Multiple technical factors play key roles in your injection mold tooling success. Design and material selection are critical as well as the tool construction and components, tolerances and precision, and cycle time and production efficiency. For example, one of the primary considerations in tool construction is the choice between hot runner and cold runner systems. Knowing the advantages and disadvantages of each will help drive the efficiency, quality, and cost-effectiveness of your project. Focusing on getting these technical factors right ensures proper functionality and manufacturing effectiveness.
Cycle Time and Production Efficiency
Cycle time is a critical factor, directly impacting production efficiency and overall costs. Understanding and optimizing cycle time without compromising part quality is essential for a successful manufacturing process.
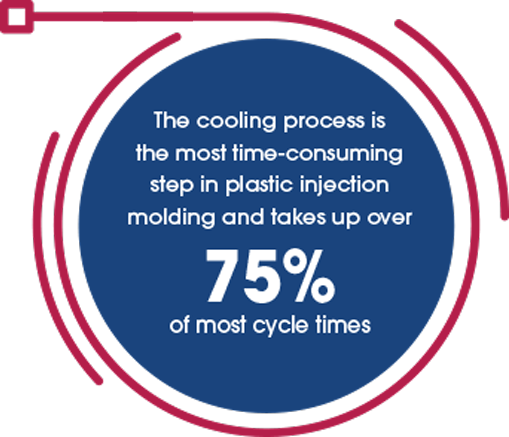
Cost Considerations
Total cost of ownership is on the minds of all manufacturers assessing injection mold tooling partners. The cost associated with successful injection mold tooling varies significantly based on many factors. These include initial tooling costs, maintenance and longevity, production volume and cost-efficiency, and material costs. Paying careful attention to these factors can positively impact your bottom line.
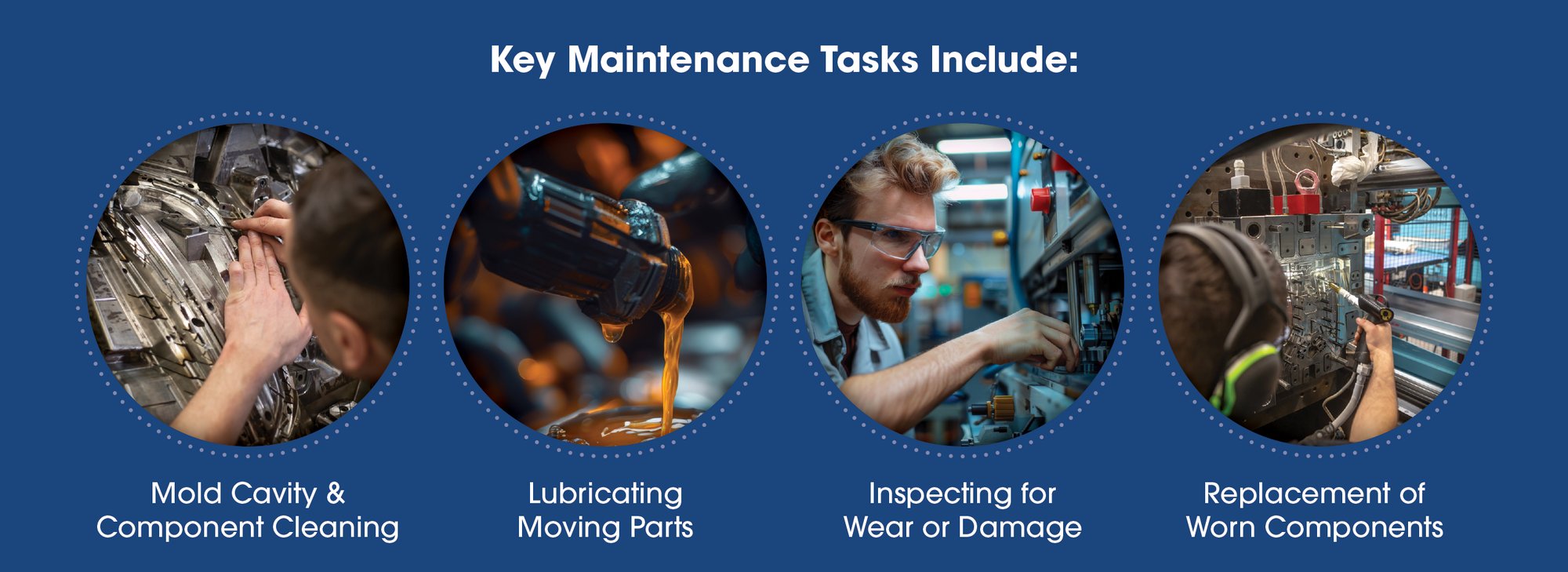
Required Maintenance for Mold Longevity
Effective maintenance of mold tools maintains the mold’s precision and accuracy. This ensures part quality is consistent over time. Predictive maintenance technologies, such as sensors within the injection molding machine, monitor process parameters to ensure that the mold is operating within optimal conditions, further extending its life. For more in-depth investigation of technical and cost considerations, download and read the guide on How to Get the Most from Injection Mold Tooling: An Essential Guide for Decision Makers.
Operational Considerations
When it comes to operational considerations for injection mold tooling, there are two key factors to consider. Lead times, as discussed above, become important, as managing lead times effectively is crucial for maintaining production schedules. Supplier selection is another key consideration, as a dependable partner with the right expertise and resources can help navigate the potential challenges you may face.
Minimizing Lead Times Without Compromising Quality
One of the key strategies for minimizing lead times while maintaining quality is the use of advanced machining techniques, such as running machining operations “lights out.” This approach allows machining processes to continue unattended during off-hours, enabling skilled operators to focus on other critical aspects of the tool build during regular working hours. This increases overall efficiency without compromising the precision and quality of the mold.
SELECTING THE RIGHT SUPPLIER
Selecting the right supplier for mold tooling influences every aspect of your project and predicts the overall success of your project. The choice of supplier affects the quality and reliability of the molds and has implications for lead times, cost, and long-term production efficiency.
Key Criteria for Selecting a Supplier
When selecting a supplier for mold tooling, consider the following key criteria:
- Tooling Options and Experience: Look for a supplier with a broad range of tooling options and extensive experience with varied materials like aluminum, steel, and composites.
- Volume Capabilities: Ensure the supplier can tailor the injection mold to your anticipated production volume, optimizing cost-effectiveness.
- Quality and Turnaround Time: A reliable supplier balances quality with reasonable timelines, ensuring high-quality tools without compromising delivery schedules.
Evaluating Supplier Capabilities and Reliability
To ensure a mold manufacturer meets your needs, evaluate their capabilities in terms of:
- Total Cost of Ownership (TCO): Consider the long-term costs of maintenance, potential downtime, and overall part quality.
- Lifecycle Support: Choose a supplier that offers support throughout the product lifecycle, from design to high-volume production.
- Integrated Services: Select a supplier that provides both tooling and injection molding services for seamless transitions and minimized risks.
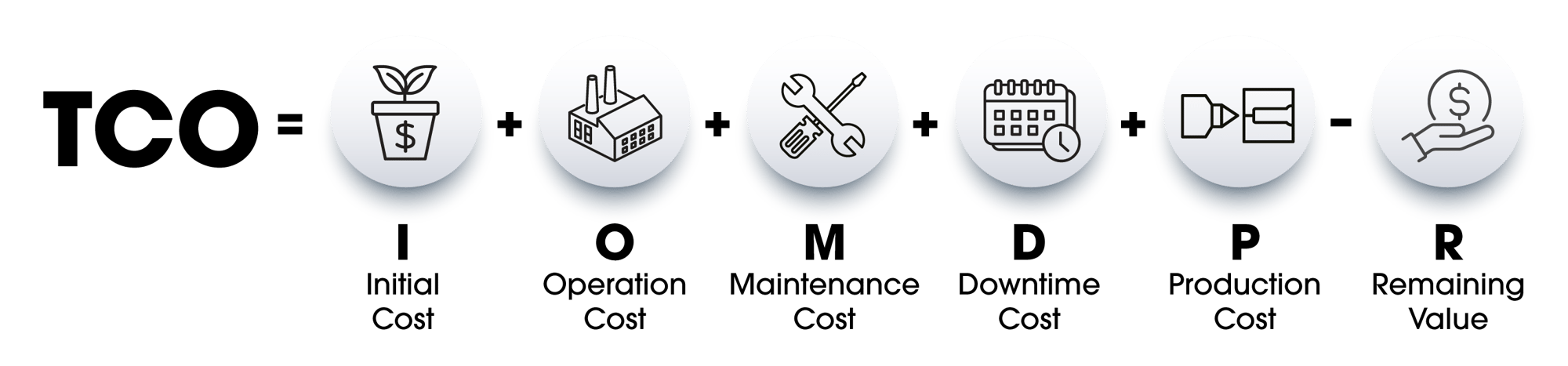
Total Cost of Ownership (TCO)
Calculating the TCO for a mold tool involves considering the initial tooling costs, ongoing maintenance expenses, and the expected lifespan of the tool. Simply put, TCO is the initial cost (I), plus the cost of maintenance (M), minus the remaining value: TCO = I + M – R.
You can add other aspects, including Cost of Operation (O), Cost of Maintenance (M), Cost of Downtime (D), and Cost of Production (P). A well-maintained mold tool significantly lowers the TCO by reducing the frequency of repairs and the need for early replacement, making regular maintenance a cost-effective strategy.
LONG TERM RISK MANAGEMENT
Forming a long-term partnership with your supplier is essential for managing risks and ensuring consistent quality. A strong partnership is built on trust, clear communication, and the supplier’s ability to adapt to your evolving needs, ultimately contributing to the long-term success of your projects.
Key Performance Indicators (KPIs) for Supplier Assessment
Track specific KPIs to ensure consistent quality and reliability:
- On-Time Delivery Rate
- Quality Metrics
- Customer Satisfaction
Avoid Hidden Costs
Low upfront costs can lead to significant expenses down the road. When evaluating quotes, consider the long-term implications of the supplier’s capabilities and how well they can support evolving production needs.
Injection Mold Tooling Partnership in Action
Crescent Industries partnered with a leading manufacturer of orthopedic surgery devices to overcome complex production challenges, resulting in higher-quality, more cost-effective results for our client. This case study details the intricate process of creating 13 high-precision components for orthopedic devices, utilizing mold simulation and advanced engineering techniques. By proactively addressing potential issues and leveraging scientific data, Crescent ensured seamless integration, cost-efficiency, and uncompromising quality throughout production.
From upfront design to final production in an ISO 7 cleanroom facility, this project exemplifies Crescent’s ability to deliver innovative solutions for demanding manufacturing needs. Want to see the full step-by-step process and the benefits of partnering with Crescent Industries? Read the case study for actionable insights for your manufacturing success.
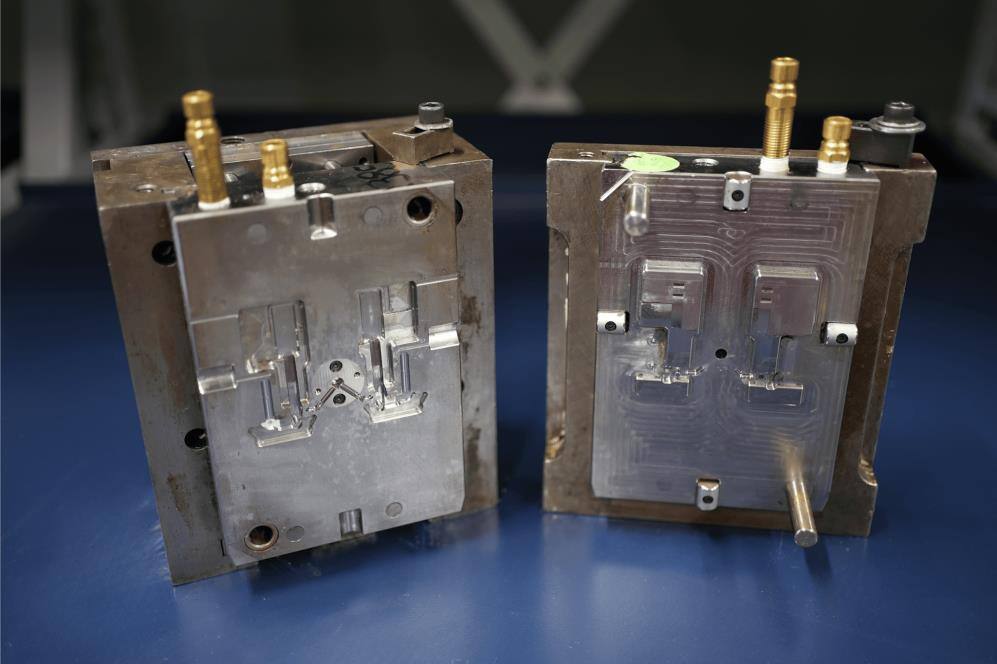
Crescent Industries is a USA-based, employee-owned plastic injection molding company offering single-source solutions for all your manufacturing needs. Our injection molding experience spans many industries, including medical, pharmaceutical, dental, defense, and industrial markets.
To learn more about how we can help you get the most out of your next injection mold tooling project, reach out to Crescent Industries today.
STEPS TO GETTING STARTED WITH INJECTION MOLD TOOLING
Achieve Quality & Success for Your Project!
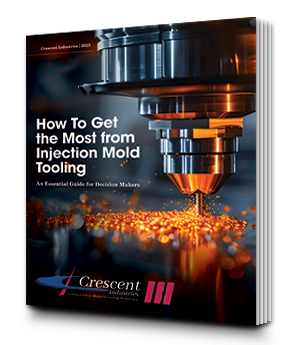