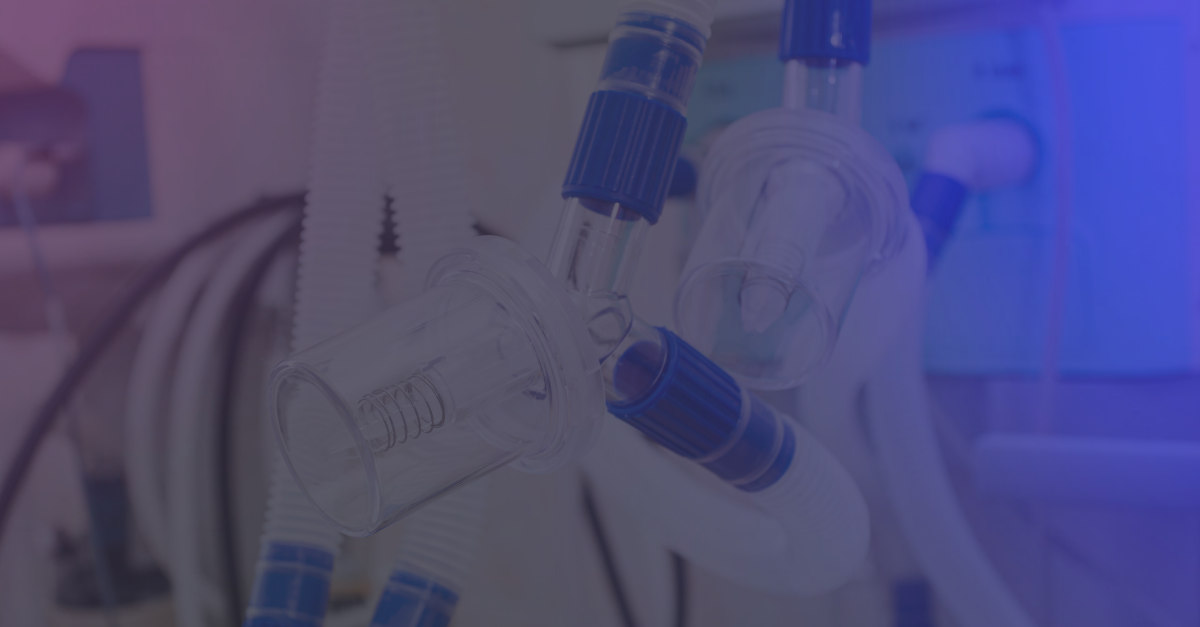
Why Should You Work With an ISO 13485 Certified Injection Molder?
In medical device manufacturing, it's important to have a business partner who understands the industry's sensitivity and complexity. They should be able to meet regulatory requirements and provide high-quality products. One of the many markers of a reliable partner is one holding an ISO 13485 certification.
But what does being an ISO 13485-certified company mean, and why should it matter to you?
What Is the ISO 13485 Certification?
The ISO 13485 certification is a voluntary standard set by the International Organization for Standardization (ISO) targeting medical device manufacturers. To be certified, manufacturers must provide irrefutable proof that they consistently meet specific regulatory and quality requirements when manufacturing devices and products. ISO quality standards are recognized globally instead of varying between countries or regions, making it easy to trust partners and suppliers.
The ISO 13485 certification isn't a simple checklist. It evaluates a facility's approach to a quality management system that focuses on key areas such as risk management, regulatory compliance, and the maintenance of effective processes. There have been many versions of the certification that have evolved following the latest research on device safety.
The current version, ISO 13485:2016, requires applicants to pass three separate phases, including documentation and a quality manual review, to ensure the manufacturing methodology isn't compromised. It's followed by a rigorous internal audit by certified bodies, reviewing all aspects of a company's operations. Everything from design and development to production and post-production activities are scrutinized to ensure they meet stringent ISO requirements.
The certification is challenging to achieve, but once gained, it provides a seal of approval that resonates with customers, peers, and regulators alike. Note that it's only valid for three years, and awarded manufacturers must reapply and go through the three inspection phases once more to renew their certification. Not to mention, the certificate can be revoked if a manufacturer is found to be in breach of the ISO international standards.
The Importance of ISO 13485 Certification in Injection Molding
Because injection molding facilities supply plastic components and devices to many clinics, hospitals, and dentist offices, working with ISO 13485-certified partners is crucial.
Regulatory Compliance and Quality Assurance
When you work with an ISO 13485-certified injection molder, you're partnering with a company that has proven its commitment to meeting the highest regulatory requirements and quality assurance standards. This certification serves as a stamp of approval trusted by governmental bodies and corporations from around the globe, verifying that the company follows the strict guidelines in the ISO 13485 standard.
A manufacturer with this certification also demonstrates reliability, in which different batches of the same device, purchased at different times, are all consistently held to the same standards of quality. This is a critical factor in the medical device industry, and any variation can impact patient safety. Also, an ISO-standard medical device manufacturer is more likely to prioritize continuous improvement to avoid errors or defects that may threaten its certification. This constant striving for improvement assures that your ISO 13485-certified partner is working to deliver the best possible product.
Focus on Patient Safety and Product Quality
Compared to plastic injection manufacturers in other industries, companies working with healthcare providers are responsible for ensuring the health and safety of their patients. By complying with this standard, an injection molder demonstrates its commitment to these values and its ability to produce medical devices that are not only effective but also safe for use.
An ISO 13485-certified injection molder will have systems in place to identify and manage risks at multiple points throughout the production line to confirm that the medical devices it produces meet the required specifications and function as intended. One example would be easily traceable lot numbers that allow it to halt the sale, recall, and destroy any products that have failed to meet the standard of quality to minimize the risks to its business partners and their patients.
Work With Crescent Industries a Certified ISO 13485 Injection Molder
Choosing a plastic injection molding supplier that can consistently guarantee the quality and safety of its devices is crucial, especially if you're a provider of medical products and devices. At Crescent Industries, we're an ISO 13485:2016 certified, FDA-registered, U.S.-based company with a new cleanroom facility to ensure that all medical components can be fabricated under the required conditions.
We're more than just an injection molder. We’re a partner dedicated to helping you succeed. We understand the vital role that our products play in patient safety and healthcare, and we take that responsibility seriously. When you work with us, you can be confident that you're getting top-quality products from a partner that understands and respects your industry's stringent ISO standards and regulatory requirements.
Don't leave your injection molding needs to chance. Choose a partner that has proven its commitment to quality and compliance. Choose Crescent Industries and contact us today to learn more about how we can help you.
Topics:
Related Articles
-
Mar 17, 2025
Labware & Diagnostic Injection Mold Building and Molding
Medical device molding requires much higher levels of precision injection molding and tolerance...
-
Jan 10, 2025
Benefits of a Plastic Medical Device Manufacturer
Reusable and single-use plastic medical devices are held to high standards of sanitation, texture,...
-
Jun 07, 2024
The Key Benefits of ISO 7 Cleanroom Standards for Injection Molding
The International Organization for Standardization (ISO) sets strict standards for the safety and...