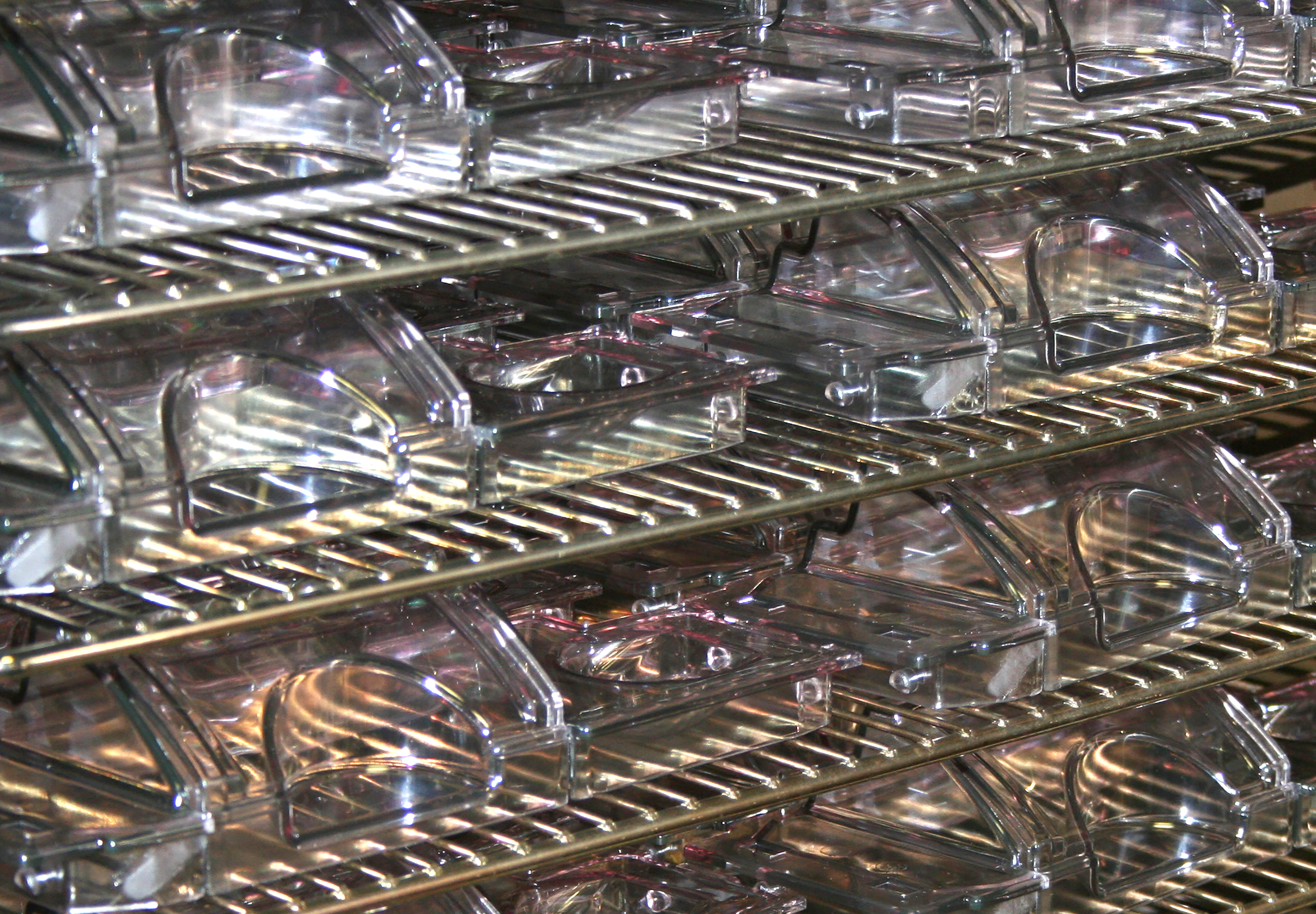
What is the Annealing Procss for Plastic Molded Parts?
Plastic injection molding is a manufacturing process used worldwide, providing an extensive range of parts for medical devices, military products, industrial applications, and more. There are many significant steps in producing these custom parts, along with post-processing steps, and the annealing process is one of them.
Definition and Purpose of Annealing in Plastic Injection Molding
Annealing is a secondary operation in plastics manufacturing that can expand your part design options and make injection-molded parts suitable for a wider range of applications. It's a common heat treatment process used on various materials, including plastics and metals.
You heat the material and allow it to cool back to ambient temperature under controlled conditions, which reduces internal stresses. The resulting parts are tougher and less likely to fail in operation.
Benefits of Annealing for Plastic Molded Parts
So what does annealing do for parts? The process of annealing can make most plastic parts:
- Stronger
- Crack-resistant
- More dimensionally stable
- Wear-resistant
Annealing plastic can also provide greater control over expansion and shrinkage, allowing manufacturers to maintain tighter tolerances around design specifications.
Annealing Techniques and Process Parameters
Learning how to anneal injection molded plastic parts requires some understanding of several different processes. Each uses different heating and cooling methods to take the part through the appropriate temperature range with sufficient time to achieve the desired properties. The medium, temperature, and time vary based on the material and part design. Depending on the size and specifications of your part, any of these methods could be a part of your overall plastic injection molding process.
Heat Treatment in Conventional Oven or Furnace
Using a conventional oven or furnace for annealing is one of the most common processes today. It involves placing batches of parts in an industrial oven or furnace and bringing them up to the annealing temperature for a set period.
The process begins with the recovery stage, where the temperature increases to relieve residual stresses. The parts then enter the recrystallization stage, where crystallization can occur without internal stresses. The gain growth stage allows the pieces to cool at a set rate, which lets new grains develop.
Thermal Cycling and Stress Relaxation
Thermal cycling heats and cools plastic parts at specific temperatures that vary depending on the material's composition. Temperatures are carefully controlled to ensure optimal stress relaxation.
The cooling rate is of primary importance in this process so that the part doesn't develop new stresses during cooling. The thermal contraction of the material can cause new stresses if the process is not carefully controlled.
Hot Water or Oil Bath Annealing
Plastic parts placed in an oven or furnace rely on air to transfer heat to the pieces. Other methods use water or oil as the annealing medium. The liquid is heated to the correct temperature, and the parts are dipped into it for the appropriate time.
Liquids must sometimes be used to avoid the oxidation of plastics, and oil is often substituted for water to achieve temperatures above the water's boiling point. Oil or water can also increase the heat transfer rate, allowing for faster annealing time.
Infrared Annealing Technology
The more traditional annealing methods like those above have been used for millennia, dating back to the oldest metalworking civilizations. Today, new technologies open the door to a broader range of opportunities. Infrared annealing enables incredibly fast and precise annealing for injection molded plastic parts. This process heats parts directly using energy from infrared transmitters, so no annealing medium is required. This process is beneficial for in-line applications due to its speed.
Key Considerations for Annealing Temperature and Time
Annealing temperature and time are critical factors that impact the quality of your parts. A variety of factors go into determining the appropriate annealing parameters, including:
- The specific material (ABS, nylon, polypropylene, polyethylene, etc.)
- The thickness of your part
- The annealing medium (air, oil, water)
- Desired physical, mechanical, and electrical properties
Annealing can provide durable, strong plastic parts suitable for many applications. However, issues can arise if you don't have the correct annealing parameters.
For plastics, the melting point is the critical temperature. Annealing processes must pass the crystallization temperature, which is often close to the melting point. Lax temperature control can lead to deformed and destroyed parts.
Controlling heating and cooling time is just as important so that the internal structure recrystallizes properly. If done too quickly, the process can create new internal stresses that make the part brittle.
Due to the number of factors and their variance, there's no one-size-fits-all solution to annealing. Working with the right value-add supplier can help ensure annealing and other secondary operations in your part design are handled correctly.
Impact of Annealing on Material Properties and Performance
The annealing process can help ensure dimensional stability. The heat treatment removes defects in the internal structure of the part, so it's less likely to undergo warping and suffer other defects affecting its shape.
Annealed parts are also less likely to experience cracking. It increases the toughness of the outer layer, providing a crystallized skin layer highly resistant to cracks that can seriously impede the overall strength of parts.
However, the benefits of annealing parts aren't restricted to mechanical properties alone. Several other essential criteria can be controlled through annealing, including electrical properties and thermal resistance.
Ensure Optimal Quality With Crescent's Post-Molding Services
The various types of annealing provide plastic parts that deliver the strength and durability your customers expect in their final applications. But achieving your desired physical properties is a challenging task that's best left to the experts.
At Crescent Industries, our team provides custom injection molding solutions and engineering support to many industries. Our production capabilities include a wide range of secondary operations, including annealing processes. Contact us today to see how we can fulfill your manufacturing and supply chain needs.
Topics:
Related Articles
-
May 07, 2024
How Focused Factory Work Cells Impact Speed-to-Market Goals
Factories and manufacturing lines are under more pressure than ever to optimize production. Whether...
-
Aug 01, 2023
What is the Annealing Procss for Plastic Molded Parts?
Plastic injection molding is a manufacturing process used worldwide, providing an extensive range...
-
Jul 11, 2023
Design Considerations for Laser Marking on Plastic Parts
In the world of plastic parts manufacturing, laser technology has emerged as a versatile and...