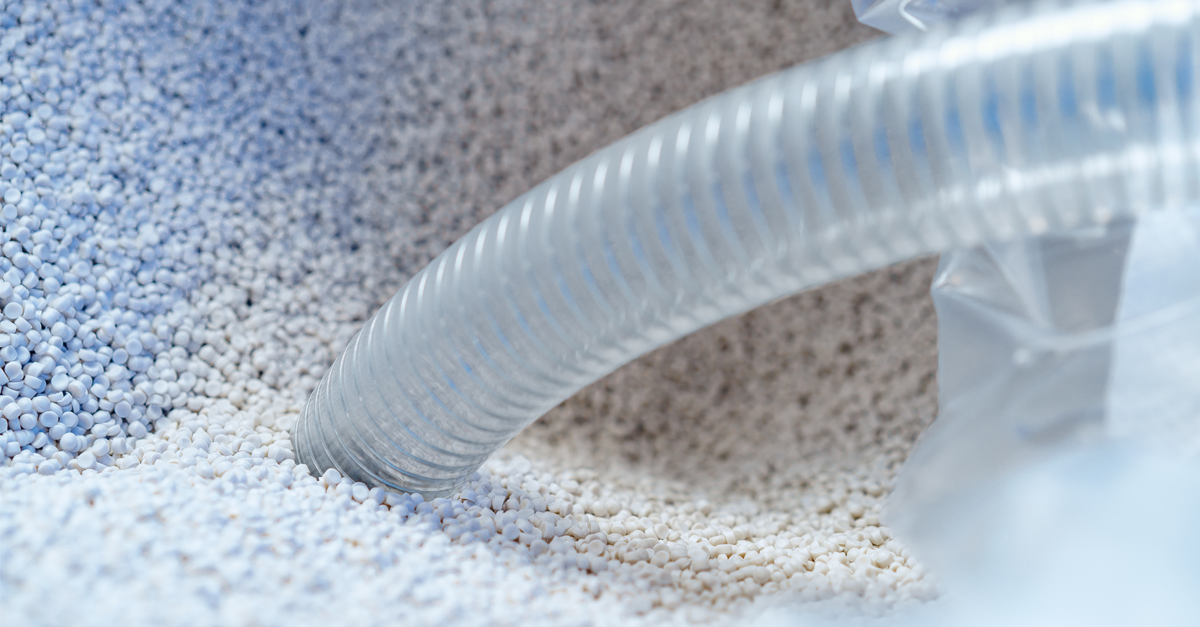
High Heat and Engineered Resins for Injection Molding
One of the major benefits of plastic injection molding is the broad range of base resin materials available. This wide selection and versatility mean extensive flexibility in material properties, product applications and cost.
Injection molding material selection is a critical factor — in conjunction with part design and engineering — in determining whether a component will perform at the required level.
Broadly, injection molding resins can be separated into two performance categories:
- Commodity resins: These materials are, as the name implies, frequently used for high-volume, commodity-type products and components. There are numerous commodity resins, offering differing material properties and price points. Typically, these materials are ideal for general-use products that will not require special material properties or environmental resistance. Examples include ABS, HDPE, PP and PVC.
- Engineered resins for plastic injection molding: Engineered resins offer more specialized material properties for scenarios such as extreme temperature resistance, wear resistance, improved strength and more. We will explore engineered resins for plastic injection molding in more detail below — but examples include high heat resins for plastic injection molding and materials such as PEI, PSU, PPS, PEEK, etc.
Engineered Resins for Plastic Injection Molding: Types and Properties
From high heat resin for plastic injection molding to increased strength and wear resistance, engineered resins offer properties that aren’t frequently associated with plastics. These materials have been developed to meet demanding requirements and are frequently used to replace wood or metal components while reducing weight.
Engineered resins and their properties include:
- Acetal: High chemical resistance, low sensitivity to moisture and condensation, low fatigue.
- PBT (polybutylene terephthalate): High electricity resistance, high impact resistance. Used for electrical housings, connectors and other electronic components. Can include glass additive to improve strength while keeping weight low.
- PET (polyethylene terephthalate): Ideal for transparent components such as lids and containers. High chemical resistance. Can include a glass additive for improved strength and impact resistance.
- PC (polycarbonate): High strength and impact resistance, retained at high temperatures. Ideal for protective lenses and various component covers.
- PEEK (polyether ether ketone): Extremely high strength and impact resistance — resistant to chemicals, wear and abrasion, corrosion, and hydrolysis. Receptive to various types of additives to increase strength. Can be sterilized at high heat.
- Nylon (polyamide): Impact-resistant and is of midrange cost and easy to process.
- TPE (thermoplastic elastomer): High impact resistance, resistant to environmental wear and UV, can include dyes to meet appearance requirements.
What to Consider in Engineered Resin Selection
The following properties are some of the most important and common considerations when selecting your plastic material.
As with any project, it is best to identify all potential requirements needs through design and application analysis:
- Material strength requirements in all probable environments: Even in engineered resins, material strength properties may change at extreme temperatures, especially high heat. Be sure to consider all environments in which that component will operate, as well as the circumstances. For instance, will it be under constant high heat? Will it be changing temperatures frequently through operational cycles?
- Stress and strain: Higher temperatures can reduce stress resistance and lead to creep strain or deformation. Be sure to select a suitable material or design the component accordingly.
- Degradation potential: In extended exposure to harsh environments such as high heat, materials may be subject to more rapid degradation and loss of strength and structural integrity.
- Expansion: For assemblies and mating components, factor in any thermal expansion that may occur in high heat, or choose a material more resistant to expansion.
As leaders in plastic injection molding — with extensive experience across materials and applications — Crescent Industries is ready to assist you in material selection for your custom injection molding requirements.
Contact us for more information about resins and injection molded parts.
Resources:
https://www.apisolution.com/basic-resin-guide.php
https://www.plasticcomponents.com/blog/key-qualities-of-high
Topics:
Related Articles
-
Mar 17, 2025
Advancements in Plastics Additives – What to Consider
Plastic additive technology has made some massive advancements over the past 10 years, but with all...
-
May 13, 2024
ABS Injection Molding: Benefits and Process
The types of plastic used to create components and products depend on its strength, heat...
-
Feb 20, 2024
What are Thermoplastic Elastomers?
Have you ever wondered about the versatile materials that seamlessly blend rubber's flexibility...