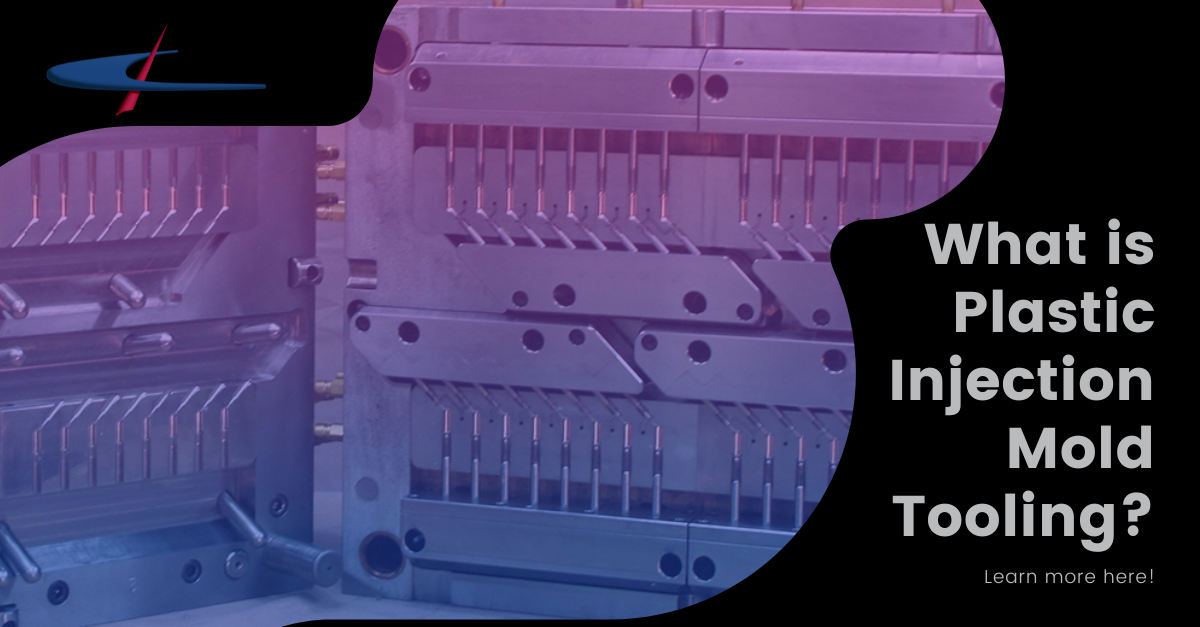
What is Plastic Injection Mold Tooling?
Injection mold design gives you the ability to create parts with ease. You fill a mold designed to your specifications using molten plastic or other materials. The resulting components can be easily duplicated, allowing for low- or high-volume production of the plastic pieces you need for your business.
To get the high-quality products you want, read on to learn about plastic injection mold tooling, injection cycles, tooling design, and all aspects of the injection molding process.
Critical Components of Injection Mold Tooling
Many components go into stainless steel injection mold tooling, aluminum molds, or mold machines. Here are some common pieces of terminology you should know.
1. Cavity and CoreCavity and core components create the final shape of the part. A cavity is a hollow area in a mold. The injection unit fills it with molten plastic to create the part. The core then makes the interior aspects of the part.
2. SprueTo get molten plastic into the mold, you use a sprue, which is a kind of channel. Usually, the sprue is the largest channel leading into the mold.
3. Runner
A runner is a channel that helps to distribute the molten plastic throughout the mold without air bubbles or blockages. It ensures that the material enters smoothly and evenly so the final piece is uniform.
4. Gates
The gate allows hot, molten plastic to enter the cavity and pour through the structure until all the features are filled with the correct amount of fluid.
Some types of gates include:
- Edge Gate
- Tunnel Gate
- Cashew Gate
- Sprue Gate
- Pin-Point Gate
- Hot Tip
- Valve Gate
- Hot Edge
Each serves a different purpose based on the design. For example, edge gates are positioned on the edge of the piece.
5. Ejector System
Ejector systems help to remove plastic parts from the molds once they cool.
6. Cooling Channels
Cooling channels are used to cool down the molten plastic for removal from the mold. These channels are machined into the mold in lines.
7. Venting System
A venting system helps air leave the mold so the molten plastic can get to every mold cavity without air bubbles or resistance.
Most molds are usually made to be nearly airtight. This can make it difficult for injections of materials to enter it smoothly. A properly placed vent removes enough pressure to let the molten material enter. Venting also helps prevent burn marks on the final piece since high pressure can produce enough heat to burn the plastic as it attempts to cool.
There are several kinds of venting, including:
- Runner venting
- Peripheral venting
- Ejector pin venting
Each one helps prevent blemishes and improves the quality of the final piece.
Types of Injection Molds
There are multiple kinds of injection molds used in injection molding machines. Here is how each one differs from the other.
- Single-Cavity Mold
Single-cavity molds only create one component per cycle. This mold has a few benefits, including upfront cost savings and affordability for lower-volume production of 1,000 parts or fewer.
- Multi-Cavity Mold
Multi-cavity molds create at least two copies of a part per injection cycle. The mold has runners and gates designed so all parts heat and cool at the same rate. Benefits of multi-cavity molds include lower pricing per part and reduced cycle times.
- Family Mold
Family molds have two or more cavities per mold layout. These molds produce several pieces per cycle, similar to multi-cavity molds. The main difference is that various parts are made with a family mold compared to multi-cavity molds for the same parts.
Family molds are a good choice for producing complex projects where you have several components or parts. They're also suitable for creating opposites; opposite halves can remain together in a mold, forming during the same cycle. Since family molds can handle complex parts and different parts at once, the entire process proceeds more quickly.
- Hot Runner Mold
A hot runner mold is a system that uses heated components to inject the molten plastic into the mold's cavities. Hot runner systems help reduce cycle time and improve part quality. They can also help to minimize waste since they stabilize the molten plastic and keep it liquified until the part is ready to cool.
For parts with a particular surface finish, using a hot runner mold helps balance the heating and cooling processes for more control during manufacturing.
Factors That Affect Mold Tooling Design
Mold tooling design is impacted by several factors, such as:
1. Part Complexity and GeometryThe complexity and geometry of a design play a role in the type of mold you'll want. For example, complex designs work well with family molds since all the parts can stay together. The complexity of a part might require specific types of gates or vents to help it flow freely and cool consistently, as well. Since molds have tight tolerances, getting the mold right before the injection process is key.
2. Material Selection and PropertiesThe injection process is different for all materials. Material selection and the materials' properties must be considered, as resin that doesn't flow well or that flows too well will impact how quickly the plastic gets into the design and begins to cool. As such, the materials dictate the gate locations and if you'll need multiple gates.
3. Production Volume and Cycle Time
The type of mold used can impact production volume. Single-cavity molds work well for lower-volume production, whereas family molds work well for complex production needs. For instance, trying to produce the same multitude of parts with single-cavity molds would be inefficient compared to using multi-cavity or family molds.
Partner With Experts in Injection Molding and Tooling
If you're thinking about upping production and creating hundreds or thousands of parts at a time, consider plastic injection molding with an industrial expert skilled in each process step.
Would you be ready to get started? We're here to help you grow your business. Contact us at Crescent Industries today at 717-928-8820 or visit us online.
Topics:
Related Articles
-
Apr 10, 2025
How Are Injection Molds Made for Plastic Manufacturing?
Do you have a part design and need an injection mold built? Are you interested in finding a tooling...
-
Feb 27, 2024
How To Find a Reputable Plastic Injection Molding Company
There's a lot to consider when searching for the right plastic injection molding company to...
-
Sep 06, 2023
What is Plastic Injection Mold Tooling?
Injection mold design gives you the ability to create parts with ease. You fill a mold designed to...