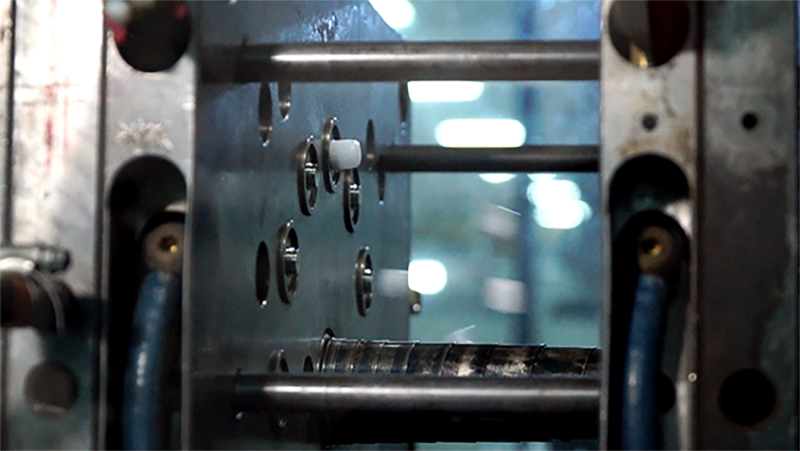
Understand the Factors Affecting the Injection Molding Process
(Updated in 2020)
The rise of the digital and technological era of today has given way to countless breakthroughs that make the injection molding process far more effective and predictable.
Anytime our industry experts apply both knowledge and experience from decades of delivering the highest-quality injection molding services and processes available in the world today - you discover the highest possible quality for designs, processes, and approaches.
The plastic injection molding process has continued to move forward. There are six major factors that remain critical to the plastic injection molding process.
These include:
1) Barrel Temperatures
2) Plastic Flow Rates
3) Plastic Pressure or "Screw Back" Pressure
4) Nozzle Temperatures
5) Plastic Cooling Rates and Times
6) Plastic Melt Temperatures
1) Barrel and Nozzle Temperatures
Barrel and nozzle temperatures are both directly related to the process of plasticizing while directly affecting the flow-ability of the plastics being moved throughout the mold. The actual mold temperature is directly connected to the ability of the plastic to flow smoothly through as well as cool down during the plastic injection molding process.
This reality means that barrel temperatures need to be considered very carefully. Because of this - the temperatures are accurately set between melting points and thermo-decomposition temperatures.
Anytime these temperatures are set too high - overflow and flash are the result. When too low temperatures cause melt lines, slowing of flow, unfilled parts, and even ripples in the product.
2) Plastic Flow Rates
The flow rates for plastic injection molding need to support the ability of the heated plastic to be injected as fast as possible into the cavity until it is at least 95 to 99 percent full.
These flow rates determine the viscosity of the plastic as it flows into the mold cavity. Anytime the hold pressures are too high - the result is both overflow and flash. Yet if the pressure is too low - you will have void problems.
With the plastic pressure settings, it is common and important for the packing of parts to finish filling while adding just enough plastic to compensate for any shrinkage. Pressure needs must be established to give the part the needed cosmetic look and size.
3) "Screw Back" or Plastic Pressure
"Screw Back" pressures are also known as plastic pressures. They are controlled relief valves located in the hydraulic system. With daily use, most products need to be as small as possible so that the pressure can vary from material to material.
When considering injection molding pressures the pressure applied to melting plastic by the head of the screw (hence the name "screw-back pressure") happens when the screw is moving forward, a process controlled by the automated systems of the machine.
When injection pressure is high, the flow-ability of the plastic is increased which can also increase issues such as overflowing and flash. When pressure is too low, it means the flow of the plastic is decreased and problems like bubbles and voids again will arise.
4) Nozzle Temperatures
All nozzle temperatures should always be lower than the barrel temperature. If it is too high - melting plastic will drool inside the nozzle and the plastic will decompose.
Materials may also block the nozzle, which causes bad components. The mold temperature completely impacts the plastic products that are created by the mold. These include:
- Flow-ability
- Cooling speed
- Performance
5) About Cooling Rates and Timing
Cooling rates mean that you have differences between melt and mold temperatures. The mold temperatures become established by the use of materials that manufacturers recommend for those ranges. Also taken into consideration are the temperatures that your customers recommend for that specific part.
Cooling times are often established by basing information on the part and mold designs. They are also based on the materials being used. To best fine-tune your cooling times during the process development - you will always need to consider customer expectations. This is applied to part appearances, desired properties, and the requested size of your plastic injection molded part.
6) Plastic Melt Temperatures
For the most accurate melt temperatures - a combination of multiple factors and settings are applied. The three areas of temperature that need to be considered the most include:
- Barrel
- Nozzle
- Mold
Crescent Industries provides so much more than just access and expertise for your plastic injection molding product. Our employee-owned company has the best reputation in the industry due to our focus on safety, ethics, reliability, and quality control.
Topics:
Related Articles
-
Mar 19, 2025
Top 6 Advantages of Injection Molding for Your Project
Injection molding — the process of injecting molten resin into a mold — is one of the most...
-
Feb 19, 2025
Injection Molding vs CNC Machining: Which Method to Choose?
Every year, humans produce and use countless plastic products in various shapes, sizes, and...
-
Oct 03, 2024
Injection Molding Uses: Exploring Applications Across Industries
Injection molding is one of the most versatile manufacturing processes, with a wide range of...