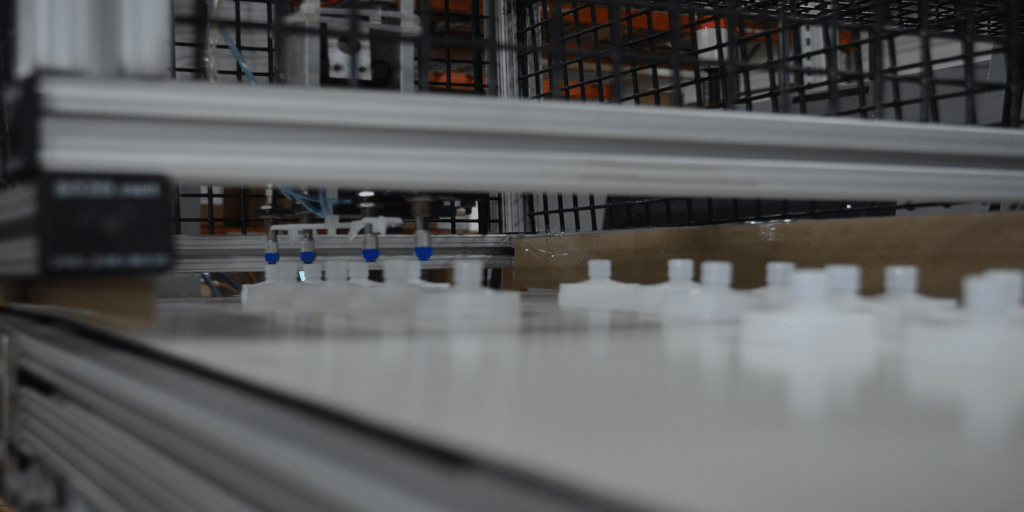
Understand Quality Validations for Injection Molded Components
When working to validate injection molded components, it is essential to understand how your supplier will address how they can assist you with validation activities by sharing their expertise, experience, and previous validation processes.
Your company 510K application is a pre-market submission made to the FDA. This is done to demonstrate a device is safe, effective, and similar in intended use, materials, components, operating principles, and method-of-use to a legally marketed device.
FDA Compliance
The FDA’s review of the 510 (k) application and notification of clearance is required before placing any moderate-risk device into the market.
Because FDA classification of medical devices is what governs the design verification - design validation and the design's clinical testing are required. This requirement directly affects how long it takes to get a device cleared for market.
Compliance Actions
Document Control –means the creation of documents and records. It enables users to attach files and documents of any size or type to be routed through document review and approval phases. This means that any changes to documents follow change procedures and processes. The solutions deliver traceability into processes for total control over compliance. This is especially critical when it becomes necessary to conform to FDA’s cGMP and ISO 13485 requirements.
Employee Trainee – this ensures employees remain knowledgeable on all processes and responsibilities. This offers automated tests to verify that training requirements are completed and supervisors can review to determine if certain elements may need more or future training.
Risk Management – identifying trends in risk and taking the initiative to mitigate the risk of a specific event and its recurrence. This should be incorporated within all processes to ensure a high level of compliance.
Corrective Action – record of an event such as a complaint, audit, non-conformity, or any other type of event and escalate the process for each corrective action using an intuitive rules based workflow.
Complaint Handling – an important part of compliance is how a company handles complaints by making sure they are recorded, reviewed, and measured and action is taken promptly.
Quality Management Injection Molding System Controls
A lack of quality management systems and controls for a vendor are far more costly than maintaining personnel or performing audits. This is because the costs to rework or scrap material - or shut down lines, freight costs, recalls and potentially even incur penalties if your product fails an audit.
Suppliers for injection molding components are now held responsible for making certain that all their processes are validated. They have to have high-quality systems in place for things like:
- Product risk management
- CAPA’s
- Design change control
- Root cause analysis
- Complaint handling
- Non-conformance
Partnering with experienced plastic injection molding manufacturer makes it possible to anticipate and plan for device production processes that meet all necessary regulatory, quality and commercial standards.
Injection molding experts must maintain procedures for monitoring and controlling process parameters for validated processes. They must also guarantee that validated processes are performed by qualified individuals. These re-validations can be required anytime processes or equipment are changed.
Validation Of Processes
Process validation means “collection and evaluation of data - from the process design phase - thorough production." This approach establishes evidence that a process is capable of consistently delivering quality products. This description is also a verbatim definition from the FDA.
This validation needs to be performed when the process is not yet fully verified by inspection or testing. For injection molding for these specific critical components, the detailed and successful process validation needs to be defined and approved - especially after producing parts that consistently perform according to customer specifications - before production runs can be begin.
Before beginning process validation for injection molding - experimentation needs to happen by changing process parameters. This is done to better determine which process variables have the most impact on the product as-well-as how far these process variables can be varied.
At every stage documentation must be kept which details inspection results, parameter settings and any other deviations from the expected performance including every reason for them. Only after all process validation procedures have been successfully completed and approved - can production begin.
These controls use a combination of resources including technology, equipment, materials and personnel. Documentation of the process validation is kept in order to show the achievement of planned results - and the ongoing maintenance of the procedure. If any part of the proving process is changed, the changed process must be re-validated.
For the market expertise in injection molding validation - consider working with the industry experts - those of us who have been on the guiding-edge of the injection molding processes for as long as plastics have been around.
Call on Crescent Industries - the market experts and industry leaders for well-over two decades.
Article Citations;
- Medical Design & Outsourcing Nov 2016 : “What is validation and why is it perceived as so complex?” – written by Oscar Ford, Business Development Manager for Preh IMA Automation.
- Medical Design & Outsourcing: “What the 10 Keys to the US pathway to medical device approval? – written by Debra Grodt – Director of Regulatory Affairs Medical Device & Diagnostics Novella Clinical
- MPO June 2016 Magazine article: “Tools for Maintaining an Audit-Ready State to Ensure Compliance” written by Emily Ysaguirre – VERSE Solutions
Topics:
Related Articles
-
Feb 15, 2024
How to Ensure High Quality Injection Molding: 6 Best Practices
The widely used practice of injection molding is a highly versatile and efficient manufacturing...
-
Feb 01, 2024
Why Should You Work With an ISO 13485 Certified Injection Molder?
In medical device manufacturing, it's important to have a business partner who understands the...
-
Jun 13, 2023
Quality Control for Injection Molding of Dental Components & Devices
While injection molding has existed since the 1800s, its use for dental components and devices has...