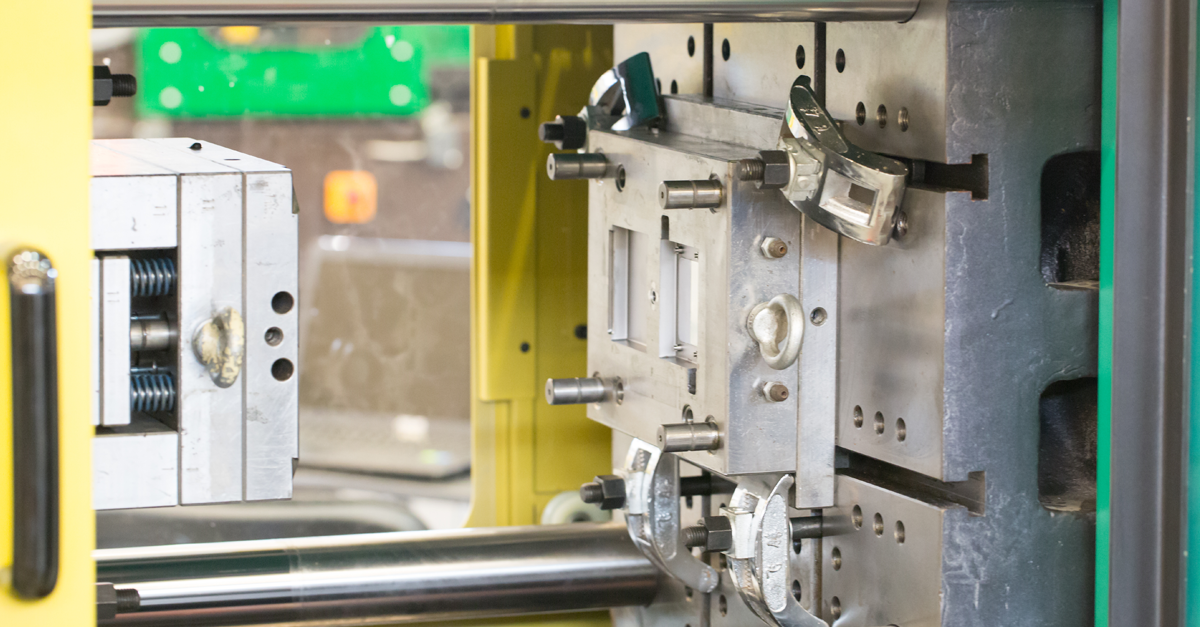
Press Tonnage Calculator for Injection Molding
One of the more frustrating aspects of the plastic molding industry that you have likely encountered is figuring out the press tonnage size needed for your plastic part design. Not only is an understanding of your part or device's press tonnage necessary for the part itself but having an accurate press tonnage calculation beforehand will help you choose the best injection molding partner for your particular needs. In addition, a press tonnage calculator can help you narrow your search for an injection molding partner.
Press tonnage measurements are vital for plastic molding machinery due to the significance of clamping force in a machine during the plastic injection process. A machine's press tonnage is the maximum force it can clamp down as it injects plastic. The injection molding press needs enough clamping power to keep it tightly sealed. Without this clamping force, the machine may leak excess plastic or fail to generate enough pressure to inject adequate amounts of plastic.
In most cases, a press tonnage calculator will provide you with exact specifications of the press tonnage based on the length and width of your plastic part.
Good press tonnage calculators should also account for the differences between solid and cored-out parts since any plastic molded part's exact press tonnage requirements may differ between these two categories. For example, a solid part's press tonnage specifications will come from a basic length and width measurement. In contrast, the specifications for a cored-out part will need to consider the length and width of the cored-out area and remove that from the measurements of the entire part.
Benefits of a Press Tonnage Calculator
If you are working in engineering and procurement, you already know that selecting the right injection molding partner is essential to your job. No matter what your plastic part design looks like, it would be best if you had a rough estimate of the size of the injection molding press needed to produce your component.
While determining exact press tonnage measurements can be time-consuming, generating a rough estimate will go a long way when seeking the right injection molding partner for your product. This is because products of different sizes or weights may require different types of clamping pressure.
For example, a small plastic component with coring would require a smaller injection molding machine versus a part that may be the same size but not cored, which may require a larger injection molding machine to make the parts.
In most cases, a good press tonnage calculator will determine the press tonnage specifications for a plastic part by calculating the surface area of the piece being manufactured and a particular index number. The exact index number will likely depend upon the units with which you measure the part's surface area.
For example, if you measure the surface area in inches, you usually use an index number between 2.5 and 4. On the other hand, if you use centimeters to measure the part's surface area, you will typically use an index number between 0.48 and 0.72.
Finding a Press Tonnage Calculator
Given the importance of a press tonnage calculator when determining the requirements for an injection molding vendor, you should always ensure you have the best tools available. Crescent Industries offers partners an interactive and user-friendly press tonnage calculator that can be used for both solid and cored-out plastic components.
As an employee-owned plastic injection molding leader, Crescent Industries knows how important determining your manufacturing requirements is when selecting a vendor.
Topics:
Related Articles
-
Feb 27, 2024
How To Find a Reputable Plastic Injection Molding Company
There's a lot to consider when searching for the right plastic injection molding company to...
-
Sep 06, 2023
What is Plastic Injection Mold Tooling?
Injection mold design gives you the ability to create parts with ease. You fill a mold designed to...
-
Apr 18, 2023
Why Should you Outsource Custom Injection Molding?
Bringing a product from design to market is challenging. The job gets even more demanding when the...