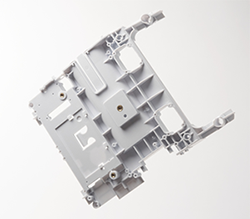
Injection Molding Tight Tolerances
As innovation and technology continue to advance within plastic injection molding, part tolerances are becoming tighter and tighter. Generally, a tight tolerance is defined as +/-.002 inches and a very tight tolerance is +/-.001 inches. Many factors impact tight tolerance including part complexity and size, raw material selection, tooling, and process conditions. As such, getting the design right is crucial when working with a product that requires tight tolerances.
Tight tolerances are usually necessary when manufacturing complex parts, especially when it comes to critical parts in the medical, automotive, or defense industries. Even a few thousandths of an inch can be the difference between a component that fits and one that does not - if tight tolerances are not achieved properly the resulting products may underperform or even fail! This is why it is imperative that OEMs understand the pros and cons of tight tolerances and if tight tolerances are truly necessary for their project.
Pros and Cons of Tight Tolerances
There are benefits to manufacturing parts with tight tolerances. This type of molding ensures parts work together smoothly and fit as intended in their final disposition; for example, gears will mesh well and there will be minimal if any mating issues during assembly. This benefit leads to another advantage which is lower failure rates – resulting in higher client satisfaction and maintaining a positive reputation for the OEM. Tight tolerances can also result in fewer post-molding processing requirements. Additionally, a benefit that is sometimes overlooked is that tight tolerances sometimes allow for parts to be transitioned from metal to plastic, reducing the overall weight and cost of the final product. This can be very advantageous in some industries, especially medical.
On the con side, tight tolerances often demand more advanced tooling and manufacturing processes that drive up costs. Additionally, every plastic behaves differently, specifically concerning shrink rates that significantly impact repeatability. Thus, products with tight tolerances may require a higher grade or specialized polymer that also increases costs.
Design Considerations for Tight Tolerances
It should be noted that not every plastic injection molding project requires tight tolerances – in fact, OEMs often spend more than is necessary for tight tolerances on non-critical features! Many products only require standard tolerancing because the consequences of failure are low. As a general rule of thumb, designers should keep tolerances as large as possible while maintaining the desired functionality of the part. Manufacturers may think using methods such as Geometric Dimensioning and Tolerancing (GD&T) results in tighter tolerances; however, they result in more manufacturing flexibility and larger tolerances, especially for intricate or complex designs – lowering overall costs!
By engaging the production team during the design phase, part functionality and fit can be discussed upfront and the team can jointly develop a manufacturing process that will produce high-precision components. For these reasons, it is crucial for OEMs to partner with an injection molder, such as Crescent Industries, who have Design for Manufacturability (DFM) expertise; this simply means the design and manufacturing teams are integrated to allow manufacturability issues to be identified and addressed during the design process – saving significant time and cost! Crescent works with customers to design a product with the right tolerances using methods such as mold fill simulation as well as assist with material selection and tooling design; Crescent then uses techniques such as Scientific Molding to obtain a repeatable and controlled process during manufacturing – providing a cost-effective solution that meets the customer’s needs!
Establishing the right process for each product and repeating it is key to manufacturing tight tolerance parts. While every application is different, some process conditions impact tolerances. For example, quick cavity filling and uniform cooling at the desired temperature are conditions that are crucial to achieving repeatability, and thus, parts with tight tolerances.
Crescent Industries
Utilizing scientific injection molding principles that provide repeatable manufacturing and state-of-the-art injection molding machines, Crescent’s focus is to provide customers with a robust process that manufactures components at the highest level of quality. We consistently meet high standards and tight tolerances due to our disciplined and data-driven engineering and production processes including:
- Multiple Inspections: incoming material, first article, in-process, and final
- Capability Studies
- Control Plans
- Validation Protocols (IQ, OQ, and PQ)
- Risk Mitigation via PFMEA
Crescent Industries is an employee-owned custom injection molder providing an integrated single source solution for your custom plastic injection molded components utilizing our advanced engineering capabilities. Our capabilities allow us to mold a comprehensive range of engineered and commodity grade resins. We currently provide high-surface finishes and tight tolerances for critical components and products for military & defense, electronics, dental, medical & pharma, industrial, aerospace, and other markets.
Topics:
Related Articles
-
Mar 19, 2025
Top 6 Advantages of Injection Molding for Your Project
Injection molding — the process of injecting molten resin into a mold — is one of the most...
-
Feb 19, 2025
Injection Molding vs CNC Machining: Which Method to Choose?
Every year, humans produce and use countless plastic products in various shapes, sizes, and...
-
Oct 03, 2024
Injection Molding Uses: Exploring Applications Across Industries
Injection molding is one of the most versatile manufacturing processes, with a wide range of...