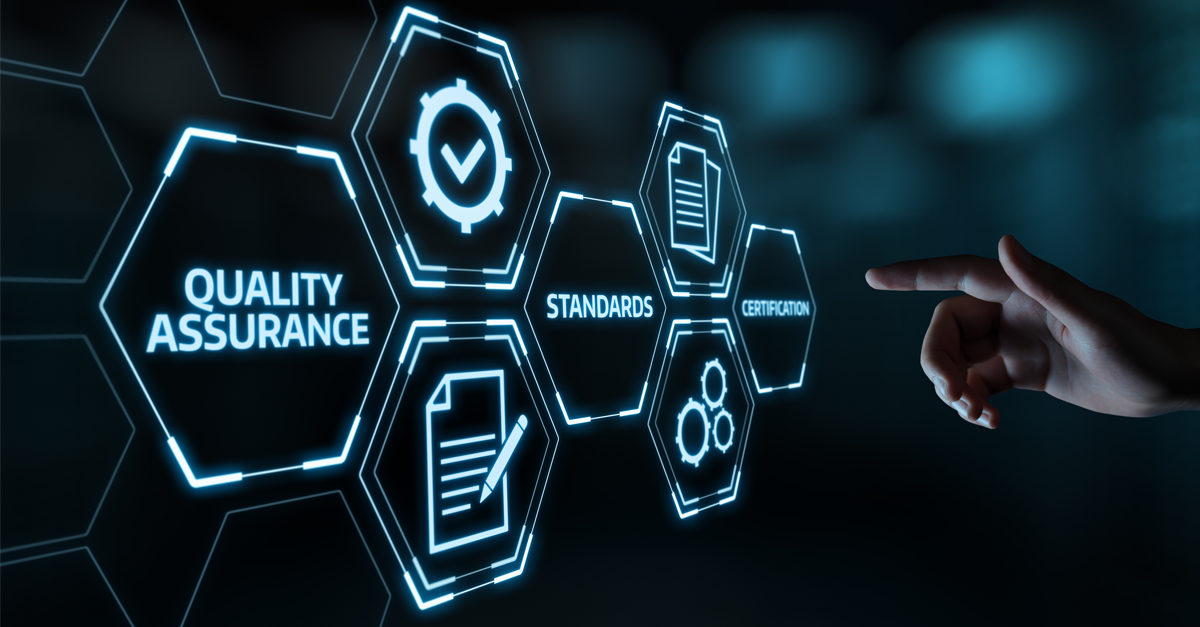
Injection Molding Supplier Quality Standards
Producing precise and custom plastic products requires keen attention to plastic injection molding tolerance standards. As an engineer, product developer, or supply chain manager, the journey from product design to injection mold to the flawless final product depends on following and testing for adherence to these standards every step of the way.
Here’s some insight into the crucial plastic injection molding quality standards you need to understand when choosing a molder. With these standards in mind, you can select a reputable molding company to transform your design into a consistent stream of top-notch plastic parts.
Key Quality Standards for Plastic Injection Molding
Several key quality standards govern injection molding. From general quality management systems to industry-specific regulations, each standard sets the benchmark for manufacturing processes.
ISO 9001: Quality Management Systems
ISO 9001 is a globally recognized standard for quality management systems (QMS). It provides a framework for establishing and maintaining a process-oriented approach to quality control, which is crucial to achieving consistent quality across an organization's operations.
For plastic injection molders, meeting ISO 9001 means focusing on several core principles. These principles can translate into actionable strategies for promoting quality molding standards and meeting tight plastic tolerances:
- Meeting Custom Needs: ISO 9001 emphasizes the importance of active customer engagement in tailoring products that meet market demands and enhance satisfaction.
- Leadership: Effective leadership fosters a culture of quality in plastic injection molding. ISO 9001 encourages clear direction from top management, ensuring optimal resource allocation and consistent pursuit of quality objectives.
- Engagement of People: Skilled and motivated employees are crucial in plastic injection molding. ISO 9001 promotes employee involvement and empowerment, creating a committed workforce contributing innovative ideas.
- Process Approach: ISO 9001 advocates for a meticulous approach to the complex processes involved in plastic production. By defining and monitoring each production step, this principle helps minimize errors across different injection mold classifications.
- Improvement: ISO 9001 champions continuous improvement, prompting molders to regularly evaluate injection molding processes, raw materials, and technologies for enhancement opportunities.
- Evidence-Based Decision Making: Data-driven decision-making involves proactively analyzing quality, efficiency, and customer feedback data to address issues.
ISO 13485: Medical Devices Quality Management
The stakes for ensuring quality are even higher when manufacturing medical devices through plastic injection molding. Even minor inconsistencies can have life-altering consequences.
ISO 13485 builds upon the foundation of ISO 9001 by providing additional requirements tailored to the medical device industry. These requirements focus on aspects like:
- Management Responsibility: Management is tasked with formulating a high-value quality policy, setting clear quality objectives, and conducting regular reviews. This highlights the crucial role of management in implementing and maintaining a robust quality management system.
- Resource Management: ISO 13485 outlines the resources needed to implement and maintain an effective quality system. They include qualified personnel, proper infrastructure, and a controlled work environment to minimize contamination risks.
- Product Realization: ISO 13485 mandates thorough planning. This entails defining product quality needs, determining injection molding parameters like injection speeds, and maintaining proper documentation. Verification, validation, meticulous tracking, and material selection are also crucial.
- Analysis and Improvement: ISO 13485 stipulates that organizations must plan and execute monitoring, measurement, analysis, and improvement processes related to the QMS. This injection mold standard involves demonstrating product conformity and maintaining the overall effectiveness of the QMS.
Crescent Industries leverages its ISO 13485 injection molding certification to ensure the highest quality standards for medical device components.
ITAR Compliance for Military Applications
Defense and military device production often involves handling specialized products that require strict adherence to government regulations. The International Traffic in Arms Regulations (ITAR) dictates the export and import of military appliances. ITAR compliance ensures that these sensitive technologies are not transferred to unauthorized entities.
Crescent Industries, an ITAR-registered manufacturer, has decades of experience in military injection molding and mold-building. Being ITAR-registered, we strictly observe legal requirements and have robust measures to handle and protect classified data.
Why Are Quality Standards Important in Injection Molding?
Rigorous quality standards act as a control mechanism, ensuring each injection molded component meets the precise specifications outlined in the design phase. These specs translate to a properly functioning product with high-quality aesthetics. Adherence to quality standards in injection molding also prevents costly delays associated with rework or product recalls.
Compliance with established injection mold standards further helps to minimize flaws in production runs. Frequent occurrence of defects can significantly negatively impact a project and a brand's reputation. By meeting the set standards, manufacturers ensure high-quality production that enhances customer satisfaction.
For engineering and product development teams, these standards provide a blueprint for meeting mold design specifications and client expectations. For purchasing and supply chain managers, the quality standards ensure reliable sourcing and consistent supplier performance.
How To Select the Right Plastic Injection Molding Company
Selecting the ideal injection mold manufacturing company is critical when bringing your product idea to life. To find the right manufacturer, start by having a clear design concept from the outset. Consider the type of material, production volume, and capacity needed for your project.
You'll also want to consider looking for a company that offers comprehensive, start-to-finish manufacturing services. By working with a single partner through every stage of the production process, you can gain valuable insights about what works and what doesn't.
Finally, evaluate the company's adherence to quality standards and plastic molding tolerances. Factors like pre-production inspection, the efficiency of injection molding machines, industry recognition, and ISO plastic certification are crucial in this final step. A molder with a proven track record of quality can guarantee top-quality plastic parts.
Leverage Our 75+ Years of Manufacturing Solutions
Key quality standards like ISO 9001 and 13485 guarantee safe, high-precision parts, while ITAR registration safeguards sensitive military projects. These standards are critical, but selecting the right injection molding partner for your project doesn't stop there. Choosing a molder with clear communication, a commitment to quality, and the capacity to meet your volume demands is essential.
With over 75 years of experience, Crescent Industries has been a trusted partner for companies seeking exceptional plastic injection molding solutions. Our industry certifications, cutting-edge technology, and meticulous approach to designing mold tools and products enable us to prioritize quality systems.
Contact us today to discuss your next injection molding project and discover how our innovative manufacturing solutions can turn your vision into reality.
Topics:
Related Articles
-
Apr 10, 2025
How Are Injection Molds Made for Plastic Manufacturing?
Do you have a part design and need an injection mold built? Are you interested in finding a tooling...
-
Mar 19, 2025
Top 6 Advantages of Injection Molding for Your Project
Injection molding — the process of injecting molten resin into a mold — is one of the most...
-
Feb 19, 2025
Injection Molding vs CNC Machining: Which Method to Choose?
Every year, humans produce and use countless plastic products in various shapes, sizes, and...