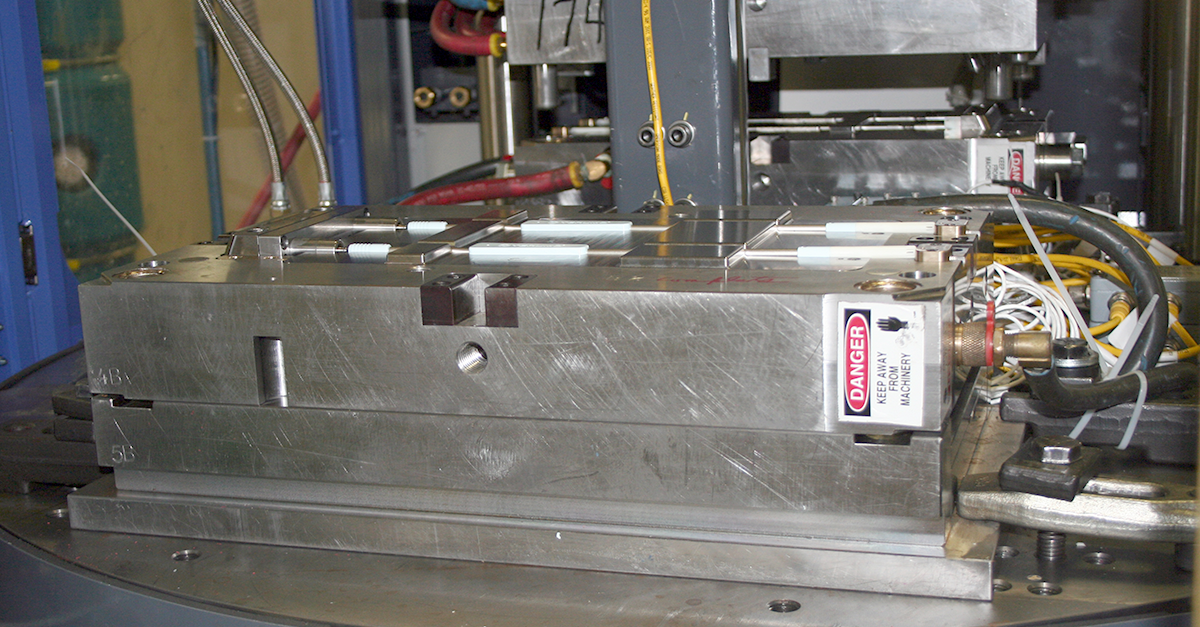
How Vertical Injection Molding Assists the Insert & Over Molding Process
One of the most standard injection molding machines utilized by injection molders is the horizontal press. In horizontal injection molding machines, the mold opens and closes in a horizontal direction, and the injection unit of the machine follows in a horizontal direction.
Since maintaining heat stabilization is vital for an ideal injection, the sprue bushing stays in contact with the injection unit on horizontal presses. The result means that the process has reduced the amount of excess material, as well as reduced the common defects. Once the molten plastic has been injected into the mold and is ready for ejection, the horizontal press then helps. Since the mold is on a horizontal path once open, gravity assists with the ejection of the part causing it to fall from the mold.
With vertical injection molding - the mold will open and close in a vertical direction. Vertical injection molding machines are primarily used for applications that create finished products that contain two pieces utilizing the concept of over molding or insert molding. With the mold opening vertically, there is easier access to insert substrates and metal inserts. In addition, gravity aids in holding the inserts or substrates in position during mold closing. This also provides easier access to retrieving finished parts, instead of the parts dropping to a conveyor or bin, which is especially useful if the components are fragile.
Vertical/vertical injection molding takes advantage of gravity instead of trying to fight it due to the vertical mold alignment. Another advantage of vertical/vertical injection molding machines is the ability to work with multiple molds and simultaneous operations on a rotary turntable by utilizing multiple bottom halves allowing inserts to be loaded in one bottom while the other is molding with the top half. The result is greater efficiency and faster productivity.
Over Molding
The process of over-molding is molding two different plastics one on top of or around the other. The mold must be meticulously designed and the molding process expertly executed. If the balance between the pieces is off - the resulting product will become distorted or fail. The pieces must fit together so it is a single component free of gaps and stress. This results in a single structure that is strong and rigid on the inside yet flexible, colorful, and easy to hold on the outside. This makes hand held items ergonomically and aesthetically pleasing and makes products effective with shock absorbency, which can help eliminate noise and vibration. It can also cover sharp corners and edges, and it can increase the longevity of your devices and tools by helping to keep out dust, water, and vapor.
Besides adding style - the process can:
- Add handles to products without grips and
- Make sleek or coarse surfaces easier to grab
Insert Molding
Insert molding is a manufacturing process that combines thermoplastic and metal components into a finished part. This involves placing various types of inserts into specially designed molds; the plastic is then injected into the mold, and quickly fills in the features around the insert. This creates an assembled and incorporated component that is ready for use.
Utilizing engineered plastics improves wear resistance, tensile strength, and weight reduction - and metallic materials for both strength and conductivity. This process utilizes methods like over molding, which helps to strengthen the part and provide resistance to both vibration and shock.
The variety of inserts that can be molded into plastic components vary widely from;
- Screws
- Studs
- Contacts
- Clips
- Pins
- Rivets
- Threaded fasteners
- Bushings
- Tubes
- Magnets
and made from materials such as;
- Brass
- Stainless steel
- Bronze
- Aluminum
- Copper
- Monel and nickel/nickel alloy
Insert molded components are used in housings, instruments, knobs, devices, and electrical components for a wide array of applications in the medical, defense, aerospace, electronics, industrial, and consumer markets.
Crescent Industries is a custom injection molder that utilizes both horizontal and vertical/vertical injection molding presses. Skilled in the processes of over molding and insert molding to manufacture numerous products for the medical, pharmaceutical, dental, defense, safety, aerospace, and electronics markets. For more information, contact Crescent Industries.
Topics:
Related Articles
-
Mar 19, 2025
Top 6 Advantages of Injection Molding for Your Project
Injection molding — the process of injecting molten resin into a mold — is one of the most...
-
Feb 19, 2025
Injection Molding vs CNC Machining: Which Method to Choose?
Every year, humans produce and use countless plastic products in various shapes, sizes, and...
-
Oct 03, 2024
Injection Molding Uses: Exploring Applications Across Industries
Injection molding is one of the most versatile manufacturing processes, with a wide range of...