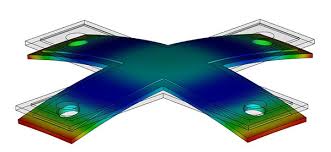
Avoid Plastic Part Warpage: Simple & Effective Techniques
Successful part designs and material selection are built on an understanding of potential process-related issues such as the potential for warpage – thus, it is very important to understand the causes of warp in order to avoid this defect!
Shrinkage is a reduction in the size of the molded part as it cools. All injection molded parts shrink, but they do so by different degrees.
During the cooling step in injection molding, if a component cools and shrinks uniformly in all directions, the part becomes smaller but retains the desired shape. However, if the part does not shrink uniformly due to variation in shrinkage both globally and through the cross section of a part, internal stresses or residual stresses are created. These stresses act on a part with effects similar to externally applied stresses. If the residual stresses induced during molding are high enough to overcome the structural integrity of the part, the part will warp upon ejection. Warp, or warpage, is simply a distortion in the intended shape of the molded part that occurs during cooling. Warping can make the parts twist, fold, bend, and bow.
The design of the part should evaluate the potential for warping which is mostly caused by non-uniform cooling.
How to Avoid Warpage?
Achieving low and uniform shrinkage is a complicated task due to the presence and interaction of many factors such as molecular and fiber orientations and operating conditions such as temperature and pressure. However, below are a few recommendations to help OEMs avoid part shrinkage and warpage.
- All injection molded parts shrink as they cool, therefore differences in the thickness of the part will cause the part to shrink at different rates. As a part cools, the thin sections cool first. As the thicker sections cool and shrink, stresses occur between the thin and thick walls. The thinner section does not yield since it has already hardened, resulting in warp. Avoid non-uniform wall thickness to facilitate a more uniform flow and cooling across the part.
- Sometimes coring out a part leaves it structurally unsound or can cause the part to warp. Ribs can be added to compensate for this, adding strength and stability to the part.
- Allow adequate cooling time and ensure it is slow enough to avoid the creation of residual stresses in the part.
- Poor venting may also be a source of warpage. Consider increasing the size or number of vents, or perhaps a different vent location may resolve the issue.
- The cooling system should be designed to apply uniform cooling throughout the part; consider conformal cooling if traditional cooling methods are not adequate.
- Check the gate design and locations to ensure they provide a uniform flow pattern through the part to avoid shrinkage variations.
- Mold cavity pressure is highest near the gate - so plastic near the gate area tends to shrink less than the material farthest from the gate. Balance the filling pattern, and use a proper packing pressure level. This allows sufficient packing time and removes the pressure after the gate freezes. Additionally, consider reducing the plastic viscosity.
- Different plastics shrink more than others. Some plastics shrink differently in one direction than in the other. Select raw materials that are less likely to shrink and deform such as filled resins or amorphous polymers.
- If you are using a molding technique, such as overmolding, where two or more plastic materials are being used to create the final part, material selection is critical. The materials do not have to be the same but they must be compatible and bond together chemically and/or mechanically to avoid defects such as warpage.
The amount of shrinkage needs to be accurately predicted during the part design phase. This can best be determined by part size and resin selection. Additionally, simulation can assist the part designer in determining if the part will have excessive shrinkage and warpage. OEMs should work with their molding partner to perform a DFM, Design for Manufacturability, analysis to model the part, identify potential shrinkage or warpage concerns, and adjust the design as necessary to address the issues.
Crescent Injection Molding Capabilities
For 70+ years, Crescent has been providing an integrated single source solution for customer’s plastic injection molded components utilizing our advanced engineering capabilities, in-houses tooling, and production facilities. Our capabilities allow us to mold a comprehensive range of engineered and commodity grade resins. We currently serve the medical, pharmaceutical, dental, defense, safety, electrical/electronic, aerospace, and OEM/Industrial markets.
Contact us today to learn more about our in-house tooling and complete manufacturing solutions.
Related Articles
-
May 20, 2025
Designing for Injection Molding Success: What Every Engineer Should Know
Designing plastic parts for injection molding is both a science and an art. From material selection...
-
Mar 19, 2025
Top 6 Advantages of Injection Molding for Your Project
Injection molding — the process of injecting molten resin into a mold — is one of the most...
-
Feb 19, 2025
Injection Molding vs CNC Machining: Which Method to Choose?
Every year, humans produce and use countless plastic products in various shapes, sizes, and...