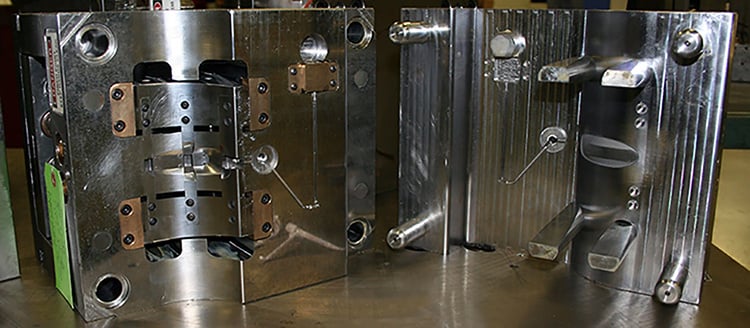
Why You Need the SPI Mold Classifications When Obtaining Quotes
(Updated April 2019)
Unless extremely specified, an OEM can face challenges when sending out an RFQ to their injection molding supply chain. While each supplier has a fundamental basis for why they choose to build the tooling the way they do, setting a general standard on the RFQ will be very helpful in comparing “apples-to-apples”.
Frequently OEMs RFQ’s can be somewhat generic with only part geometry, annual volume, and material selection which leaves a lot of guesswork on the injection molding supplier side. While other OEMs have internal tooling standards and their RFQ’s are extremely specific requesting the same quote from each supplier, these OEMs typically specify the SPI mold classification amongst other items in their “tooling standard”.
By specifying the SPI mold class, you can ensure that each of the injection molding suppliers is in the same general range for the tooling prices. If the OEMs engineering team is experienced enough, then further specifications within the SPI mold class and beyond will be extremely beneficial to the injection molding supply chain.
Following standards or general guidelines will always be the best practice when getting pricing from multiple sources. This will not only save time to get your quotes back, but it will also remove the headache of “back and forth” with the injection molding supplier requesting changes from what they originally quoted.
SPI Mold Classifications
Mold Classification Information for SPI Class 101-103 molds from the Plastics Industry Association (formerly Society of Plastics Industry Inc) “Customs and Practices of the Mold Making Industry”.
The following classifications are guidelines to be used in obtaining quotations and placing orders for uniform types of molds. It is our desire through these classifications to help eliminate confusion in the mold quote system and increase customer satisfaction. The following contains a brief synopsis of the various mold classifications and the detailed descriptions of each mold class up to 400 Tons.
Class 101 Injection Mold
- Cycles: 1 Million or more
- Built for extremely high production, this is the highest priced mold and is made with only the highest quality materials.
- Detailed mold design required.
- Mold base to have a minimum hardness of 280BHN.
- Molding surfaces (cavities and cores) must be hardened to a minimum of 48 R/C range. All other details should also be hardened tool steels.
- Steels moving against one another should be dissimilar and have a hardness differential of at least 4 Rockwell “C”.
- Ejection should be guided.
- Slides must have wear plates.
- Temperature control provisions to be in cavities, cores, and slides wherever possible.
- It is recommended that plates and inserts containing cooling channels be of a corrosive resistant material or treated to prevent corrosion. Corrosion in the cooling channels decreases cooling efficiency thus degrading part quality and increasing cycle times.
Class 102 Injection Mold
- Cycles: Not exceeding one million
- Built for medium to high production, good for abrasive materials and/or parts requiring cost tolerances. This is a fairly high quality, fairly high priced mold.
- Detailed mold design required.
- Mold base to be a minimum hardness of 280BHN.
- Molding surfaces (cavities and cores) must be hardened to a minimum of 48 R/C range. All other details should be made, and heat treated.
- Temperature control provisions to be directly in the cavities, cores, and slides wherever possible.
- Parting line blocks are recommended for all molds
- The following (guided ejection, slide wear plastics, corrosive resistant temperature, control channels, and plated cavities) may or may not be required depending on the production quantities anticipated. It is recommended that the production quantities be made a firm requirement for quoting purposes.
Class 103 Injection Mold
- Cycles: Under 500,000
- Built for medium production. This is a very popular mold for low to medium production needs. Most common price range.
- Detailed mold design recommended.
- Mold base to be a minimum hardness of 165BHN.
- Cavity and cores must be 280BHN or higher.
- All other extras are optional.
Crescent Industries follows the above SPI guidelines when quoting and manufacturing injection molds. We utilize our expertise as injection molders and the most advanced technologies and equipment to produce injection molds for a variety of industries such as; medical, pharmaceutical, dental, defense, and industrial.
Topics:
Related Articles
-
Apr 10, 2025
How Are Injection Molds Made for Plastic Manufacturing?
Do you have a part design and need an injection mold built? Are you interested in finding a tooling...
-
Sep 06, 2023
What is Plastic Injection Mold Tooling?
Injection mold design gives you the ability to create parts with ease. You fill a mold designed to...
-
Nov 16, 2022
Project Management for Injection Molding Means Product Success
There’s a difference between project management and engineering management, and in the field of...