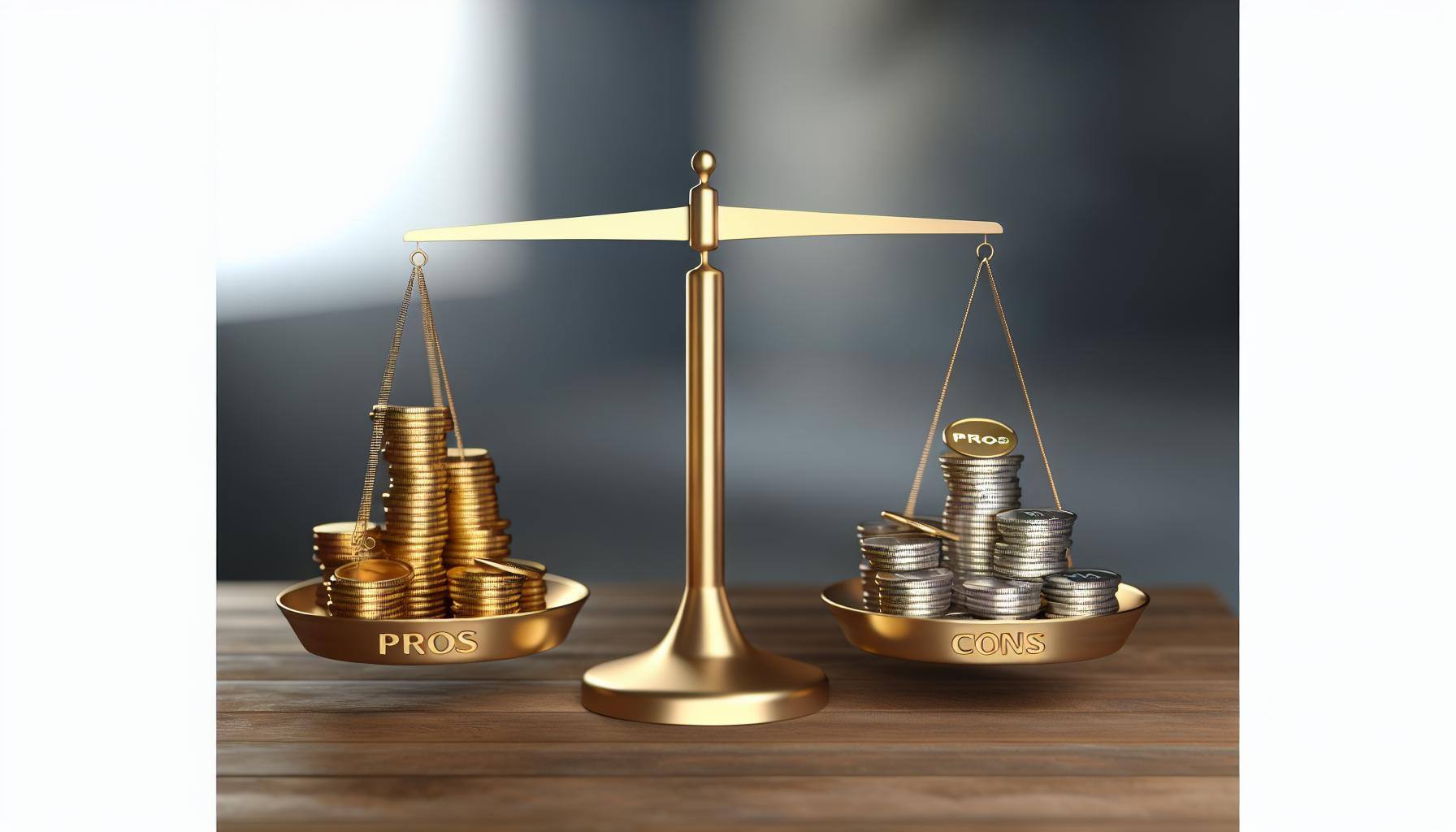
8 Advantages and Disadvantages of Plastic Injection Molding
Plastic injection molding is one of the most widely used manufacturing techniques for producing high-quality plastic components and custom parts. It's popular in the manufacturing industry and has several advantages, but depending on your project requirements, some cons are also associated with plastic injection. You'll need to consider both the advantages and disadvantages of injection molding to make well-informed decisions for your business needs.
Advantages of Plastic Injection Molding
There are many benefits to using plastic injection molding to manufacture your custom parts.
1. Production Efficiency and Speed
A key advantage of plastic injection molding is its fast and efficient production and easily repeatable process. Thanks to a relatively short molding cycle, the mold injection process rapidly produces large quantities of product, making it ideal for high-volume production. Not to mention, multiple cavities in the same mold can produce more than one plastic part during the same cycle and time frame.
2. Cost Effectiveness for High-Volume Production
Plastic injection molding is cost-effective for high-volume production. The bulk of the cost goes to initial tooling, but the cost-per-part decreases significantly as the volume of production increases. This is because the average cycle's setup and curing time, including injection, pressure, and de-molding, remain constant per piece regardless of the total number of parts produced.
3. Complex and Intricate Part Designs
Plastic injection molding allows you to create complex and intricate part designs that may be challenging with other manufacturing processes. Injection molds can be designed to include various features, such as holes, tabs, latches, and undercuts. This makes plastic injection molding ideal for producing parts with unique and complex shapes, such as those used in medical devices or military components.
4, Consistent Part Quality and Precision
Plastic injection molding also allows for immaculate final products with tight tolerances for errors and inconsistencies, resulting in nearly identical parts. The injection process lets you fully control the molding parameters, such as temperature, pressure, and cooling times to ensure the plastic parts meet the same quality standards and advertised specifications.
Additionally, the ability to use Computer-Aided Design (CAD) software with advanced molding techniques allows you to be precise about the dimensions and characteristics of the molded parts, ensuring the final results require as few modifications as possible.
5. Wide Range of Materials and Customization Options
Injection molding is compatible with a variety of plastic materials, including thermoplastics and thermoplastic elastomers, that range in consistency, flexibility, color, and translucency.
These options allow you to choose the material that best suits your applications. Using the right materials ensures the final product meets your specifications and branding requirements.
Disadvantages of Plastic Injection Molding
Even though plastic injection molding has numerous benefits, you should consider the disadvantages before making any decisions.
1. High Initial Tooling Costs
One of the main disadvantages of plastic injection molding is the high initial costs. Before production begins, a mold must be designed and manufactured, sometimes from scratch, which can be costly and time-consuming.
The cost of the mold depends on several factors, such as the complexity of the part design, the number of cavities in the mold, and the type of material used. These costs can be a significant barrier, especially for small businesses or those with limited budgets. But, for high-volume production, the price per piece will quickly make up these initial upfront costs.
2. Longer Lead Times for Tooling and Production
Another disadvantage of plastic injection molding is the longer lead times for tooling and production than other manufacturing processes. Months of design drafting may be needed to produce a prototype, depending on the complexity of the part design and the availability of resources.
This longer lead time can be challenging if you require quick turnaround times or have tight production schedules. However, you can mitigate this issue with proper planning.
3. Constraints on Design Flexibility
Certain part features, such as deep undercuts or internal threads, may require additional design considerations or even secondary operations after molding. The process may also have wall thickness, draft angles, or part size limitations. Working closely with your custom injection molding partner ensures your part design is optimized for the injection molding process.
Custom Plastic Injection Molding for Your Business Needs
If you're seeking a reliable and experienced custom plastic injection molding services provider, look no further than Crescent Industries. With decades of experience in the plastic manufacturing industry, we specialize in delivering high-quality injection molded parts for various sectors, including medical devices, automotive, dental, defense, pharmaceuticals, and consumer products. Our state-of-the-art facilities and advanced manufacturing processes ensure that your plastic components are produced to the highest standards of quality and precision.
Contact us today to discuss your project requirements and learn how we can help bring your ideas to life.
Topics:
Related Articles
-
Mar 19, 2025
Top 6 Advantages of Injection Molding for Your Project
Injection molding — the process of injecting molten resin into a mold — is one of the most...
-
Feb 19, 2025
Injection Molding vs CNC Machining: Which Method to Choose?
Every year, humans produce and use countless plastic products in various shapes, sizes, and...
-
Oct 03, 2024
Injection Molding Uses: Exploring Applications Across Industries
Injection molding is one of the most versatile manufacturing processes, with a wide range of...