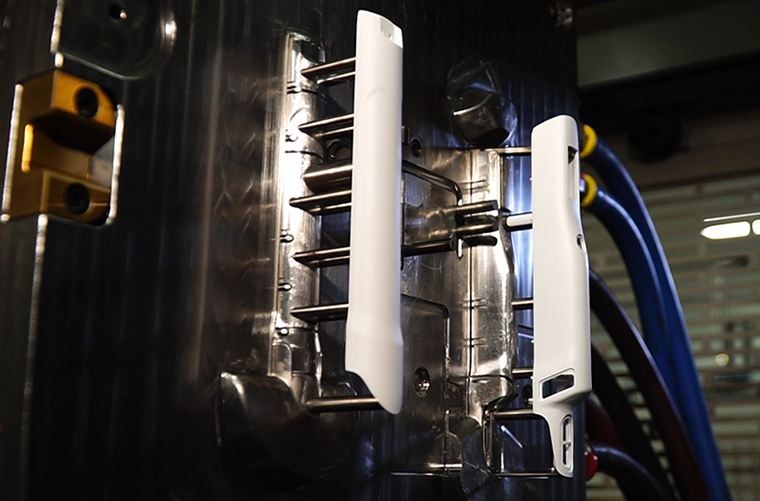
4 Factors Critical to the Injection Molding Process
The injection molding process is a vital manufacturing method for mass production in almost every industry worldwide. With the industry reaching over $284 billion worldwide, a lot of research and development has gone into perfecting the injection molding process.
Developing the injection molding process for a given part takes expert knowledge and years of experience. Four key factors must be considered to ensure quality and consistency in injection molding.
1. Temperature
Injection molding for plastic components or parts relies on melting plastic to allow it to match the shape of the mold. Controlling temperature is critical, as the plastic must assume the correct properties for the process.
Within the injection molding process, there are several vital temperatures to consider:
- Plastic melt temperature
- Barrel temperature
- Nozzle temperature
- Mold temperature
The plastic melt temperature will vary depending on the plastic, blend, and additives used. Understanding the properties of the plastic is essential to designing the process, as many plastics can suffer defects when outside a tight temperature range.
Within the barrel, plastic must be maintained at a temperature that provides the proper consistency for adequate flow. The barrel must always remain above the melting point but avoid thermos-decomposition temperatures that will degrade the plastics. Too high a temperature can also lead to overflow and other issues.
The nozzle temperature must remain high enough to ensure that material doesn’t block the nozzle and cause insufficient material to be injected into the mold. Process engineers keep the nozzle temperature slightly lower than the barrel temperature to prevent drooling.
The temperature of the mold itself plays a vital role in the flow and cooling rate of the plastic, both of which will significantly impact the quality of the plastic components or parts.
2. Plastic Flow Rates
A rapid injection rate is essential for quality parts and an efficient injection molding process. If the plastic flow rate is too low, the plastic will cool too quickly, leading to higher shrinkage and compromising the quality.
Plastic flow rates that are too high can increase the pressure required to fill the mold, causing further issues. Process conditions for custom injection molding processes don’t allow for much deviation. The plastic flow rate must be carefully controlled to prevent void problems, shrinkage, and other quality issues.
Attempting to raise plastic flow rates to improve cycle time can often lead to a significant increase in defects. Excess gas can be trapped inside, causing burn marks visible as spots or streaks on the component or part. Controlling the plastic flow and proper vent maintenance is essential to avoiding these burn marks.
3. Pressure
Pressure is another crucial factor in custom injection molding processes. Many parts and components require high injection pressures due to their small size and the speed at which molds must be filled to avoid quality issues.
Pressure is imparted to the plastic in the barrel by the screw, which is why it’s called “screw-back pressure.” Increased pressures can increase the flowability of the plastic, potentially leading to issues like flash, where a thin layer of plastic flows outside the cavity.
On the other hand, low pressure leads to numerous quality issues. Voids and bubbles will form in the plastic, impacting the plastic components' or parts' appearance and strength.
4. Cooling
The cooling rate is a factor that must be carefully controlled in any injection molding process. The plastic begins cooling as soon as it enters the mold, rapidly at first and slowing as it approaches the mold temperature.
Different plastics will require different cooling rates to avoid defects such as shrinking, delamination, and warping. Cooling channels are often necessary for mold designs to ensure even cooling throughout the entire part.
Determining the correct cooling rate is a challenging process that must consider the material, geometry, wall thickness, and other properties of the part.
Finding the Right Injection Molding Solution for Your Project
Each of these four factors plays an essential role in the results. Creating process parameters with these factors in mind enables manufacturers to strike a balance between quality, cycle time, maintenance, and other factors that affect their bottom line. With so much at play, you must ensure that true industry experts develop your process.
Crescent Industries provides integrated single-source solutions for custom molded components. Our advanced engineering capabilities allow us to optimize design factors to deliver the precision and quality you need in your plastic components and parts.
You can contact Crescent Industries today to see how we can help realize your next injection molding project.
Sources:
https://www.grandviewresearch.com/industry-analysis/injection-molded-plastics-markethttps://www.sciencedirect.com/science/article/abs/pii/S1359835X16300999
https://www.sciencedirect.com/science/article/abs/pii/S1755581721000092
https://damassets.autodesk.net/content/dam/autodesk/www/mech-eng-ressource-center/cae-analyst/assets/fy17-mold-engineer-11-factors-mold-cooling-ebook-en.pdf
Topics:
Related Articles
-
Dec 10, 2024
Injection Molding Burn Marks: Causes and How To Avoid Them
The injection molding process can be complicated. If you rush your project or do not pay close...
-
Apr 02, 2024
An Expert's Approach to Injection Molding Process Development
Are you curious about the innovation behind your flawlessly molded plastic products? Welcome to the...
-
Nov 29, 2023
What is Important to the Plastic Injection Molding Process?
Plastic injection molding is a smart and flexible way of making different products. It’s a method...