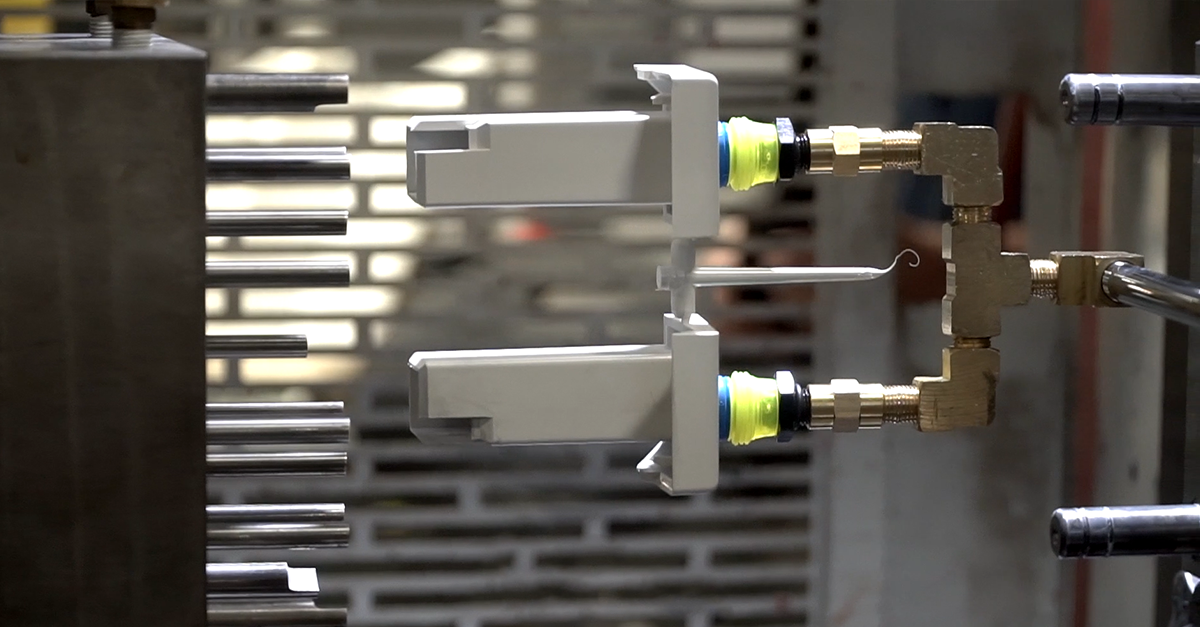
How to Avoid Plastic Injection Molding Flash
Plastic injection molding flash is a thin layer of plastic that flows outside of the cavity, creating a flap or excess material that needs trimming. The defect is common in the process of injection molding and should be avoided because of its negative consequences.
Consequences of Flashing
When flashing occurs, it has to be removed by the plastic injection molding manufacturer via deflashing. Operations personnel or robots must trim the excess material in between cycles. Deflashing is labor-intensive and adds time to the manufacturing process. It can also decrease product quality and ultimately damage the mold, leading to higher costs. For these reasons, the root causes of flash need to be identified and resolved.
How Does Plastic Injection Molding Flash Occur?
In plastic injection molding, the mold consists of multiple metal parts that come into contact with each other and with the molten plastic: Two halves of the mold come together at a parting line. The molten plastic resin material travels through sprues and runners and is injected through openings called gates. After cooling, ejector pins push the molded part(s), the runner, sprue, and gates out of the mold. At any meeting place between these different parts of the mold, a thin layer of plastic could flow outside of the cavity, creating flash. Flash is common along the parting line but can also occur at ejector pin locations and other locations.
Learn how Design for Manufacturability can help eliminate potential problems in the design phase of your project.
Causes of Injection Molding Flash and How To Remove Them
Flash can occur for several reasons, from variations in the process to material to tooling trouble. For example, flash during the injection molding of a part can happen in filling (the first injection stage) or during packing/holding (the second stage). It can occur with conventional parts and with thin-walled parts. Below are some causes of flash and options for fixing it in each case.
1. Parting Line Mismatch
Flash can be caused by parting line mismatch in the tool. To prevent parting line mismatch:
- Clean off any plastic, dirt, or contaminants that could keep the mold from closing correctly, especially behind slides and inside the leader pin bushings.
- Ensure proper mold plate fit and mold seal:
- Clean the molding press from any obstructions.
- Check if mold plates have become deformed from molding pressure during injection and packing. Correct this with pillar supports or by thickening or reducing mold plates.
- Give the mold plates adequate surface areas that seal off at the parting line, evenly distributing the clamping force during molding. Always provide a sufficient "land" of even, adequate seal-off area around the part cavity.
2. Improper Venting
Inadequate vents in the mold can cause flash. To address or rule out improper venting as a cause of flash:
- Check the mold vent size against the supplier's recommendations: Obtain the recommended vent sizes from the supplier of the plastic resin being used. Correct the vent size if the current vents are not the recommended size. If the tool is old and showing wear, re-machine the vents if needed.
- Remove air from the mold as fast as possible by making vents as deep as the material viscosity will allow. The viscosity of the plastic being molded determines the depth of the vent. Stiff materials can utilize deeper vents, but fluid materials require thinner vents.
3. Clamping Pressure In the Packing / Holding Phase
In addition to occurring during the injection phase of plastic injection molding, flashing can occur during packing or holding. In packing, pressure is adjusted, and additional material is injected into the mold to account for material shrinkage and backflow. In holding, the material is held in place at a pressure equilibrium until gate freeze occurs and cooling begins. In either of these parts of the process, if there is inadequate clamping pressure, the mold's parting line may be pushed apart, allowing the plastic to flow out and cause flash.
To address or rule out clamping pressure as a cause of flash:
- Do a first stage short shot test: If the product passes this test with no flashing, then the problem is occurring after the injection phase, and you are right to consider clamping pressure as a possible cause.
- Increase the clamp tonnage: The clamp pressure needs to be strong enough to withstand the forces generated by the plastic material flowing through the mold. Size the mold to run in the proper machine to ensure that appropriate clamp pressure will be used.
4. Sprue Bushing Issues
Hardened-steel sprue bushings in the mold provide the opening for molten plastic to be transferred to the mold cavity. Sprue bushing issues can cause flash, either when there is inadequate support for the force of the injection pressure or when the mold is held open.
- Provide adequate support in the mold for the sprue bushing: When the press nozzle seals on the sprue bushing, it can create forces from 5 to 15 tons. If there is inadequate support in the mold for the sprue bushing, this pressure could transfer to the parting line, allowing the plastic to flow out. Address this by adding the needed support in the mold for the sprue bushing.
- Adjust the sprue bushing length: If the face of the sprue bushing is sealing off on the parting line, adjust the length to ensure that nozzle pressure or thermal expansion does not hold the mold open and allow the plastic to flow out.
5. Fixing Process Variables That Can Cause Flash
Numerous process variables can cause flash. Following are some problems in process variables that can cause flash and ways to address them:
Low Material Viscosity
Flash that is caused by low material viscosity can usually be fixed by correcting the following problems:
- The melt temperature is too high
- Excessive residence time, which causes degradation
- Presence of moisture from improper drying
- An excessive amount of colorant that contains a lubricating vehicle
Over-Packing
Over-packing occurs when extra material is compressed in one flow path (the shortest, thickest paths) while other flow paths are still filling. This causes increased localized pressure in the molded part and should be avoided because it causes not just flash but other issues. Over-packing can be addressed by correcting sub-optimal molding conditions caused by:
- Material viscosity
- Injection rate
- Runner system
Injection and Packing Pressure
Reduction of pressure reduces the tendency for the material to flash. If too much pressure is used, the press may not be able to hold the mold closed. Reducing the injection and packing pressure lowers the clamp force requirement. Also, reducing the area where the two mold halves are touching will focus the clamping force and allow less clamp tonnage to be used.
Barrel and Nozzle Temperature
High barrel temperatures increase the temperature of the material, making it more fluid than it should be and more prone to flash. In addition, at a higher temperature, it can enter small openings and crevices that it could not typically enter at the correct viscosity. Reduce the barrel temperature and nozzle temperature to the recommended material temperatures. This will allow the material to be heated properly through the different stages of the barrel and reduce the incidence of flashing.
Metering / Over-Fill
To resolve flashing caused by metering (over-fill):
- Reduce the feed setting (stroke length)
- If the total cycle time is too long, the material will overheat in the barrel. Reduce the cycle time during the cooling phase.
- Use a material that has the stiffest flow possible without causing non-fill. Use the flow rate formulations provided by resin manufacturers. For example, thin-walled products may require an easy-flow resin, while thick-walled products can use a resin that has a stiffer consistency.
Preventing Flash Through DFM
Injection molding contract manufacturers (CM) use design for manufacturability to prevent problems like flash during the design phase. The CM engineers use specialized mold flow simulation software to simulate the injection molding processes, creating a 3D simulation of flow, heat flux, and warpage for injection molding, including the complete mold with all details. During the simulation, they inspect the project for flash and other problems using a checklist for DFM in plastic injection molding. They make changes to the design and plan for the mold, materials, etc., rerunning the simulation and revising until flash and other problems are eliminated.
Topics:
Related Articles
-
Mar 19, 2025
Top 6 Advantages of Injection Molding for Your Project
Injection molding — the process of injecting molten resin into a mold — is one of the most...
-
Feb 19, 2025
Injection Molding vs CNC Machining: Which Method to Choose?
Every year, humans produce and use countless plastic products in various shapes, sizes, and...
-
Oct 03, 2024
Injection Molding Uses: Exploring Applications Across Industries
Injection molding is one of the most versatile manufacturing processes, with a wide range of...