Injection Mold Tooling
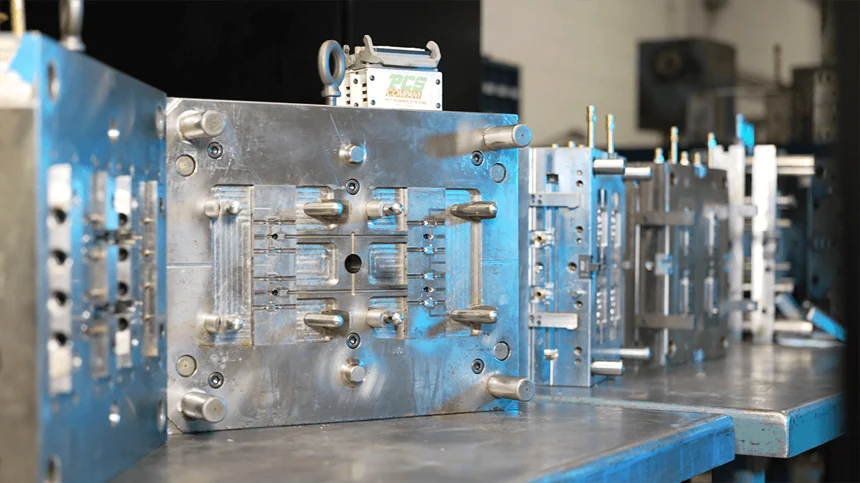
Here's an overview of our capabilities
-
Custom Mold Design & Builds In-House
Our experienced team of engineers and mold designers collaborates closely with you and your specific product requirements, part geometry, and production volume to build new tooling that produces a quality product
-
Complex Geometries
We can handle complex part geometries and challenging design features. With our advanced tooling equipment, experienced certified journeyperson mold makers that can create molds that accurately reproduce intricate details and precise dimensions to achieve your desired product outcome -
Dedicated Project Management Team
Manages all aspects of new injection mold builds
- Design for Manufacturing (DFM)
- mold design
- mold build
- Debug – document part sizes, appearance, and mold function
- Develop injection molding process and validates
- FAIR for part approval
- After your approval, launch to production
Collaborates, communicates and coordinates critical tasks and deadlines to ensure your new injection mold tooling is built on time.
SAMPLES OF INJECTION MOLD TOOLS
- One parting line and mold splits into two halves
- Sprue, runners, gates, and cavities are all on the same side
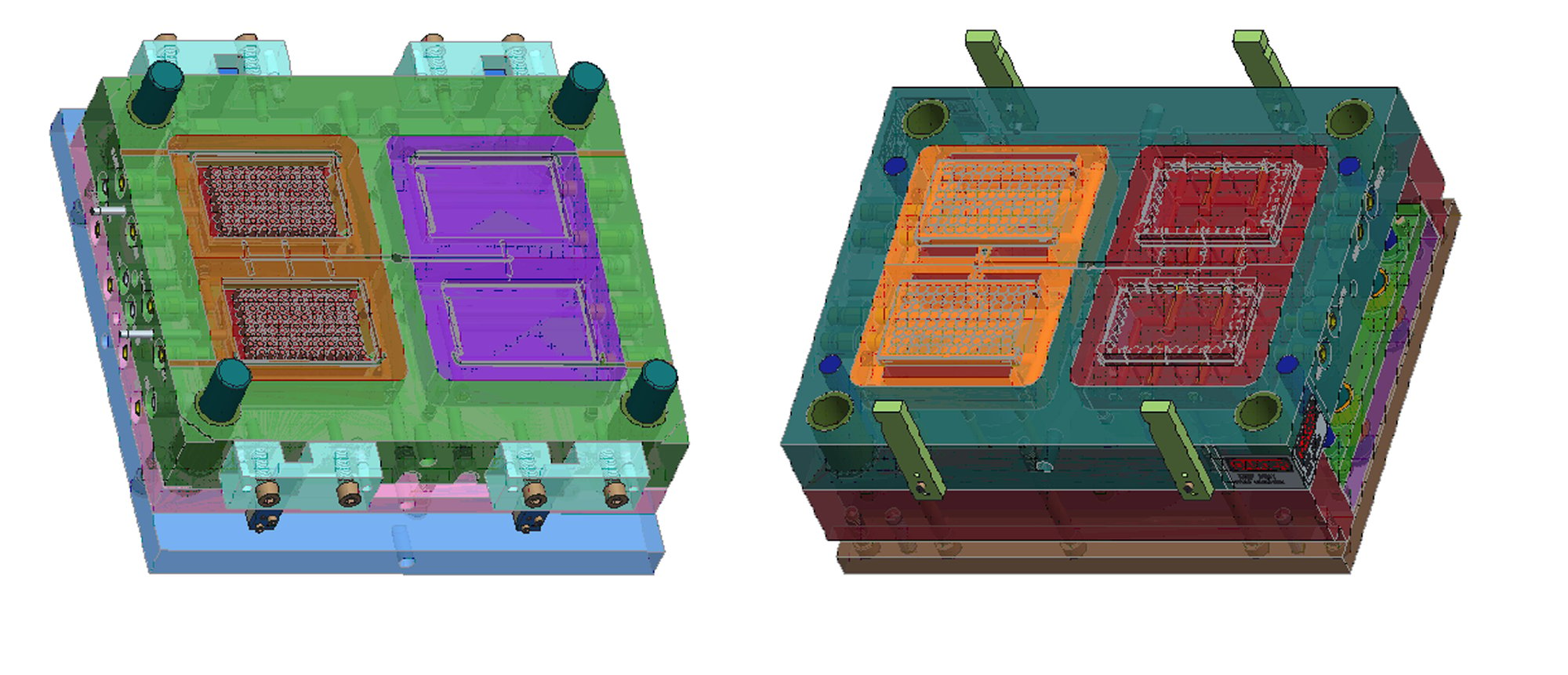
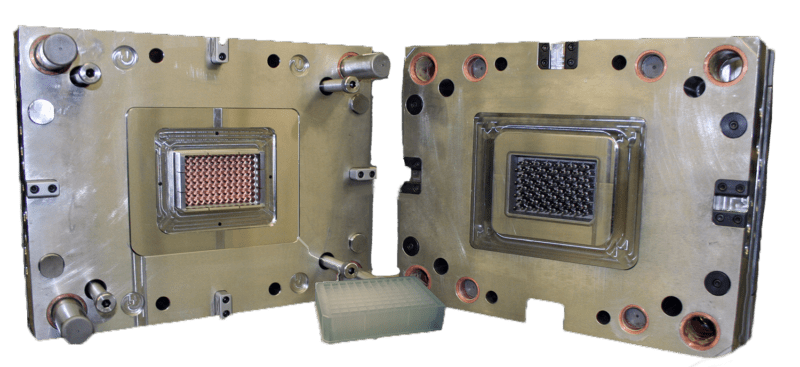
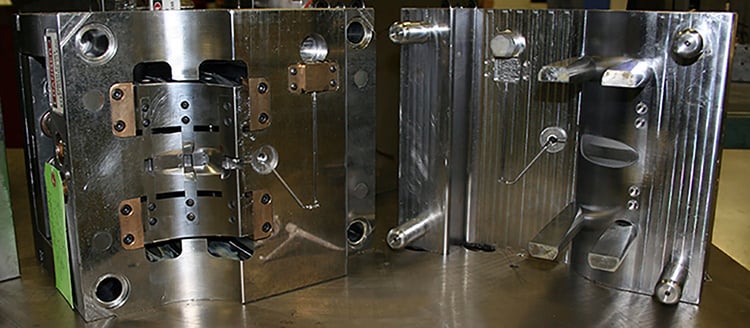
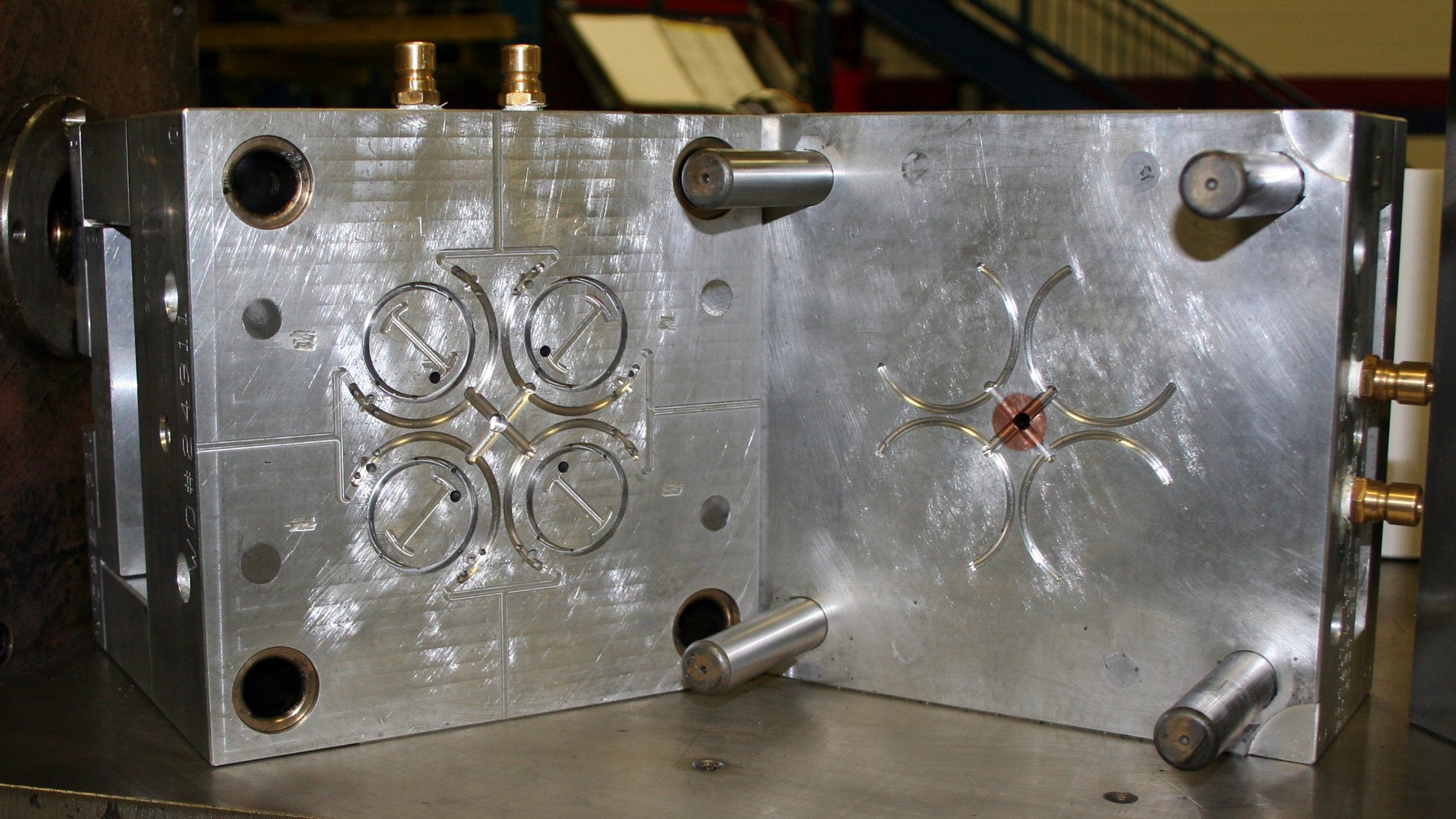
- Two parting lines
- Flexibility in Gating Location
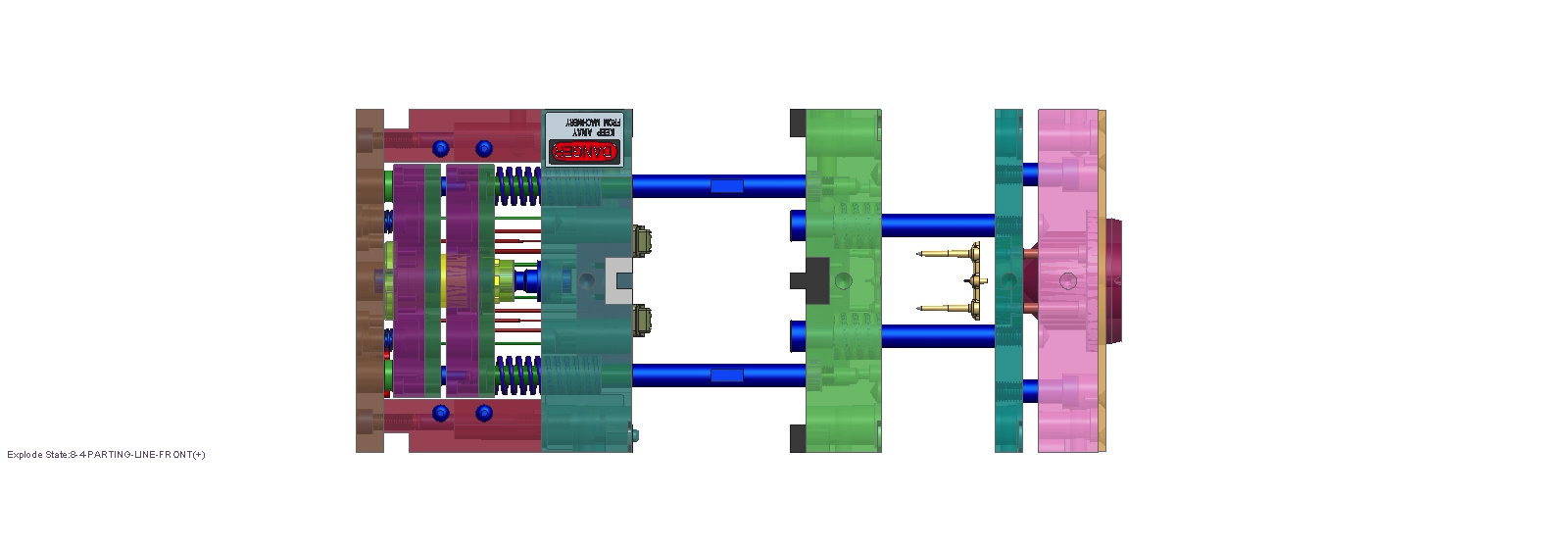
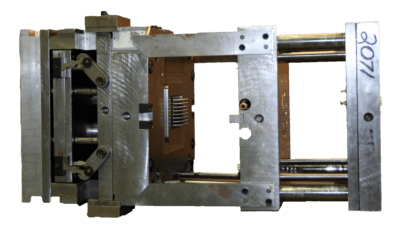
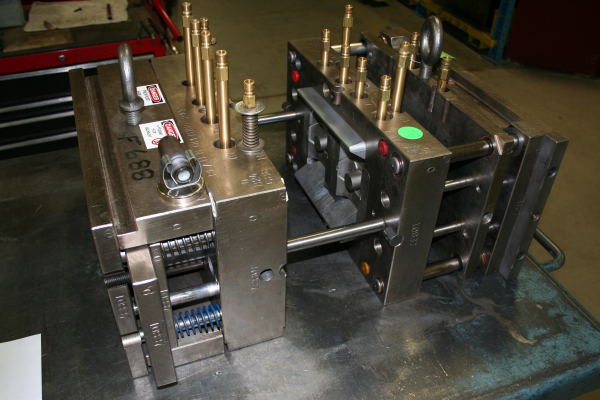
- Produces several parts at one time
- Good for high-volume production requirements
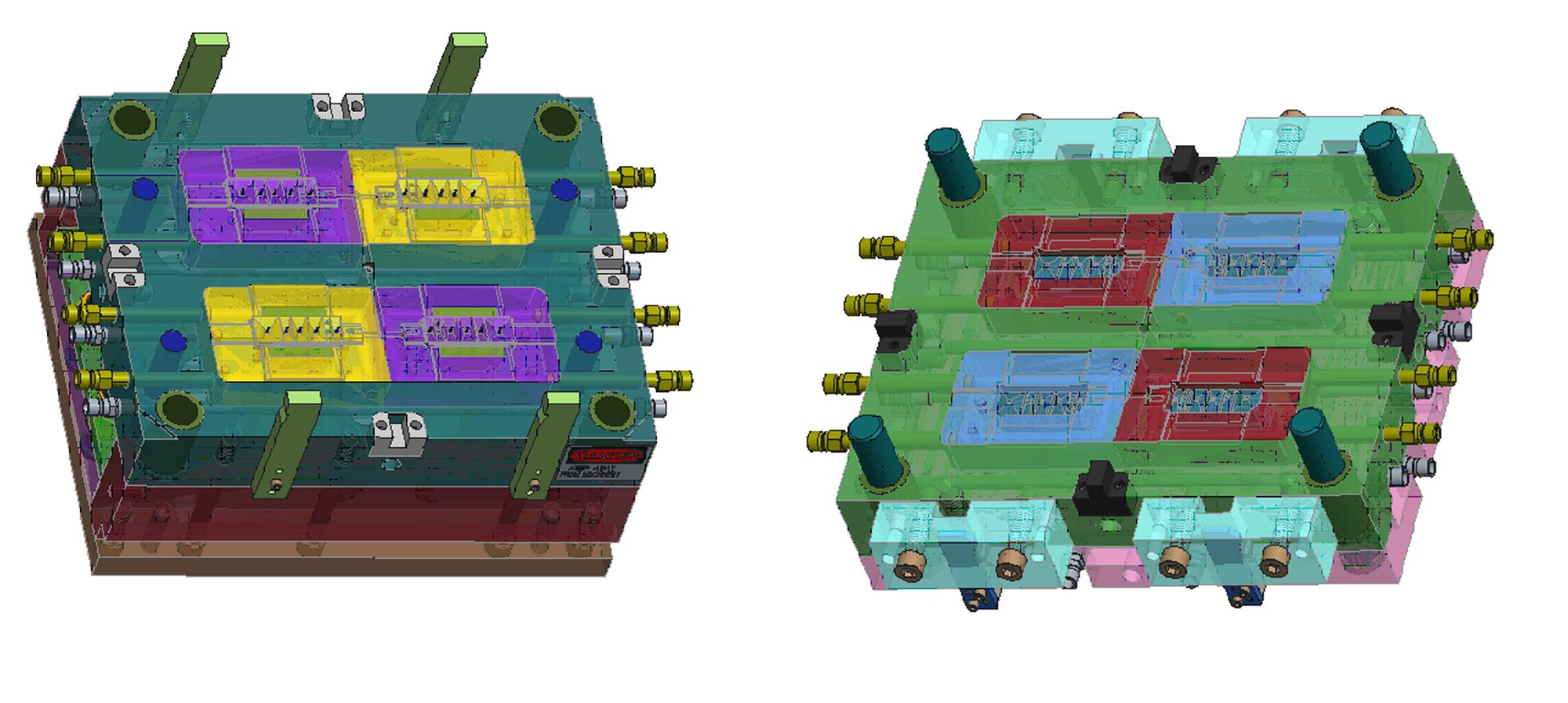
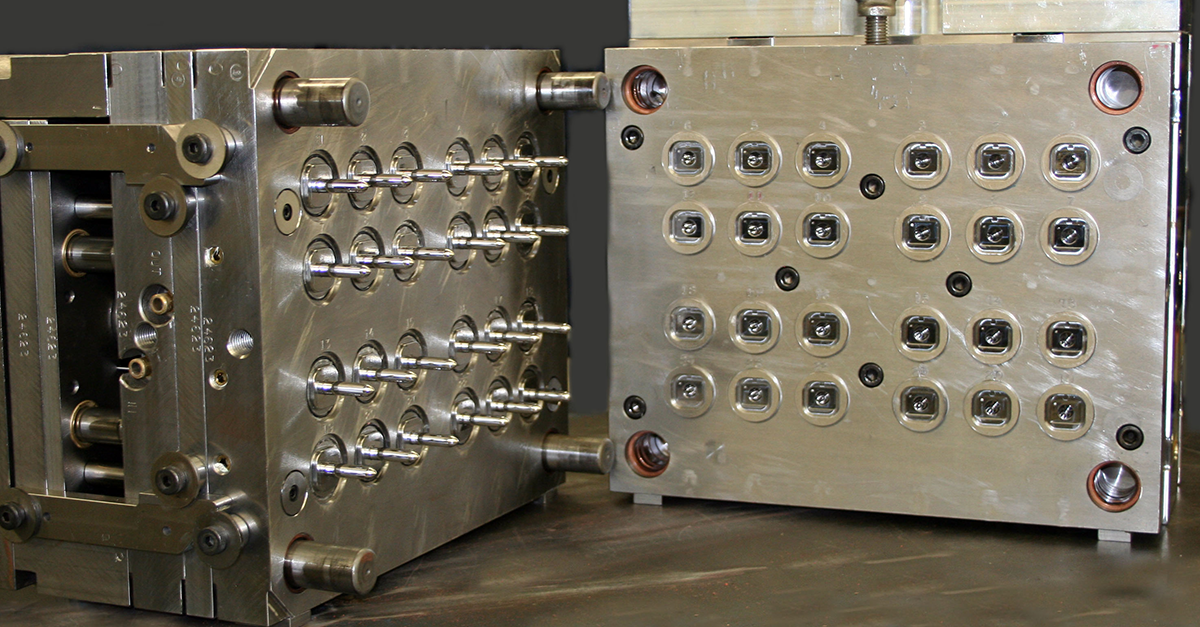
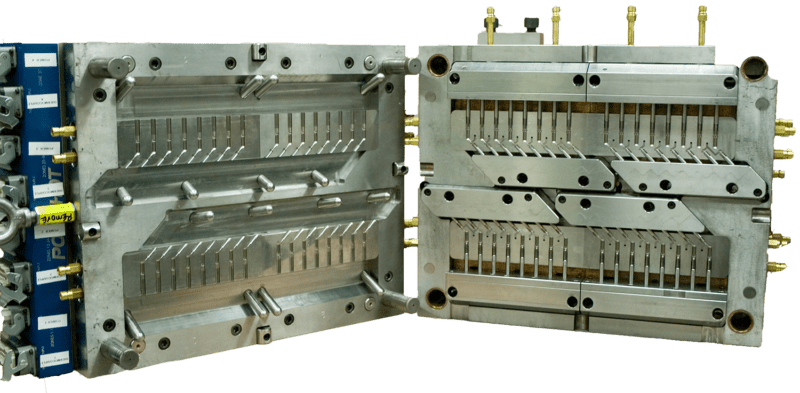
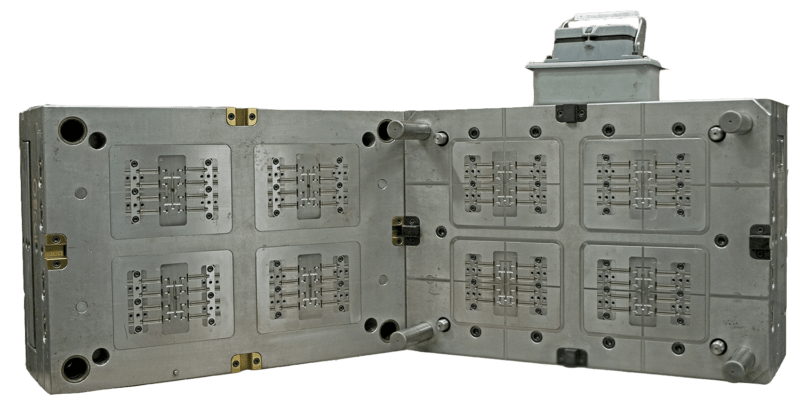
- No runner waste
- Higher upfront tooling cost
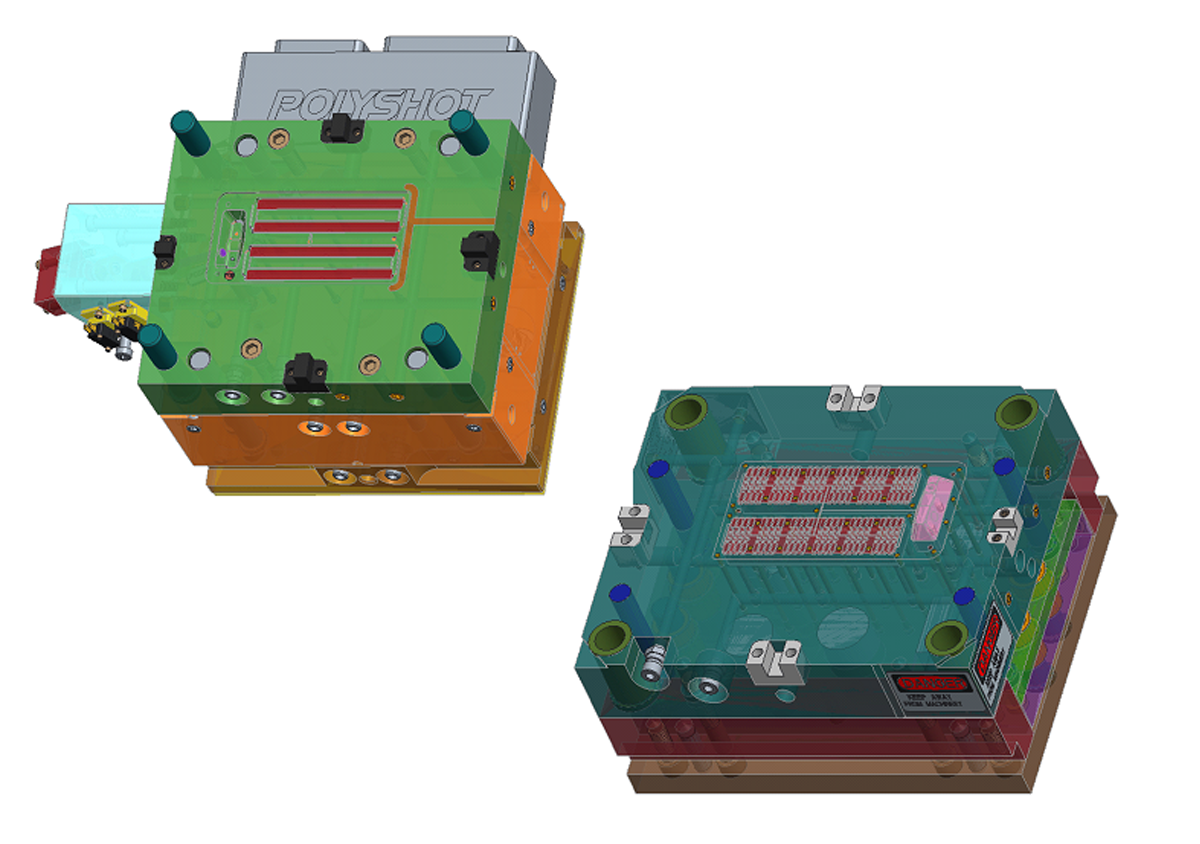
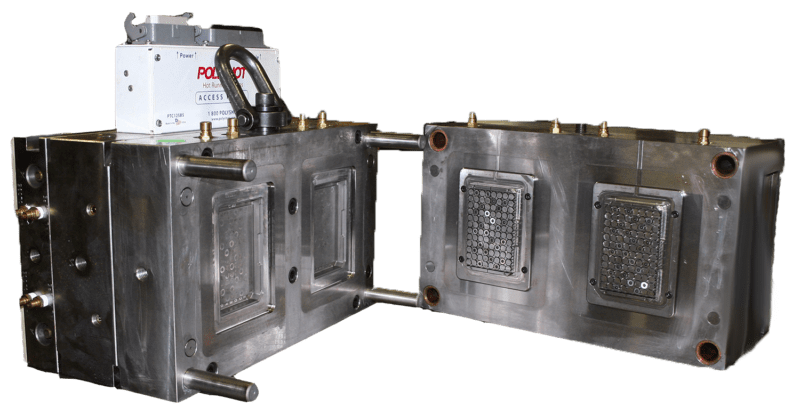
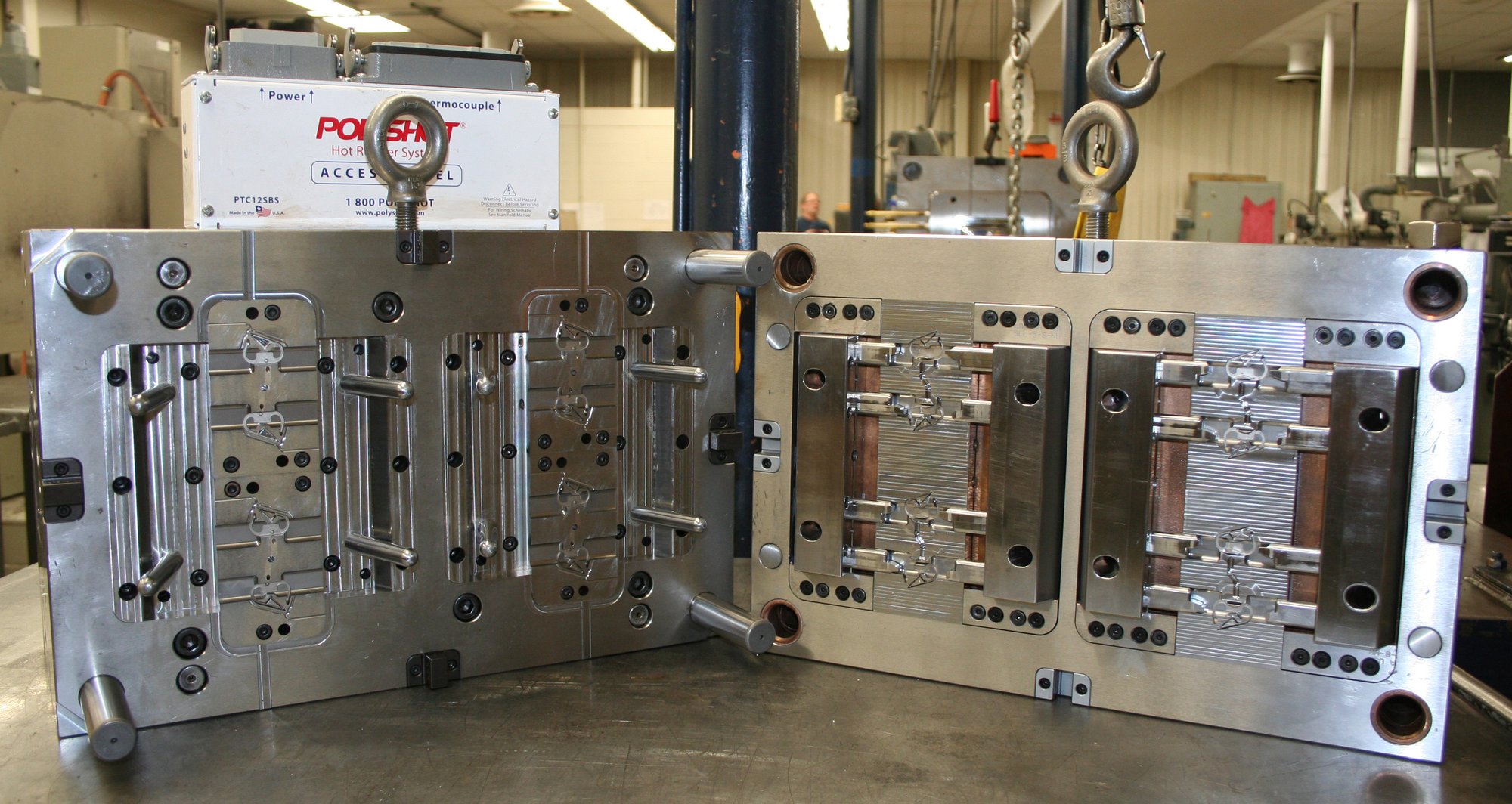
- Used when a requirement for threads on plastic component
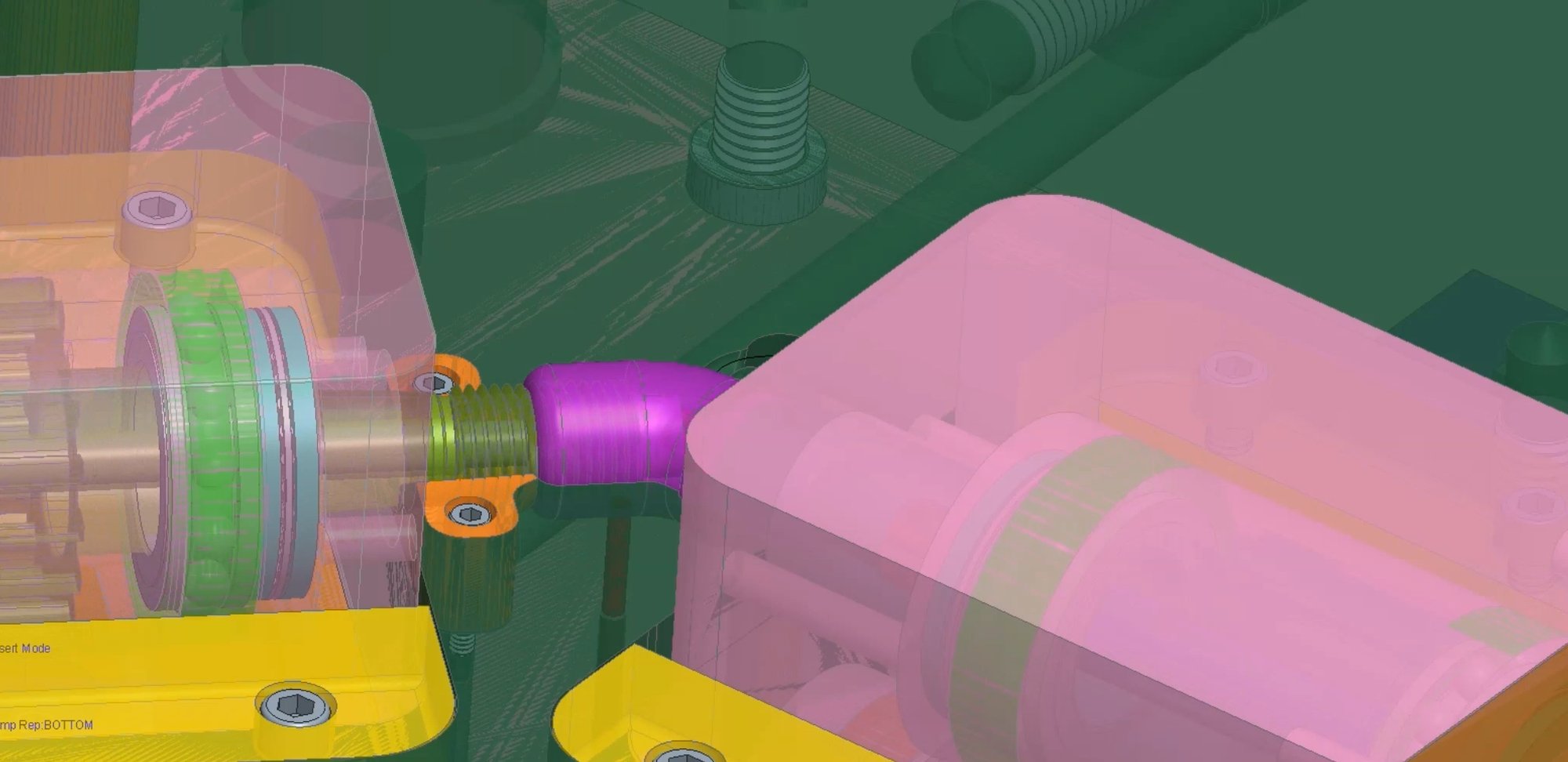
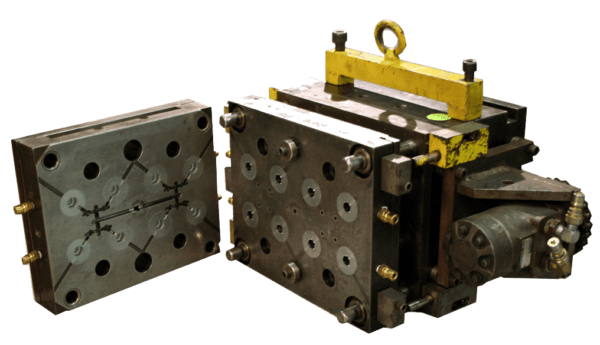
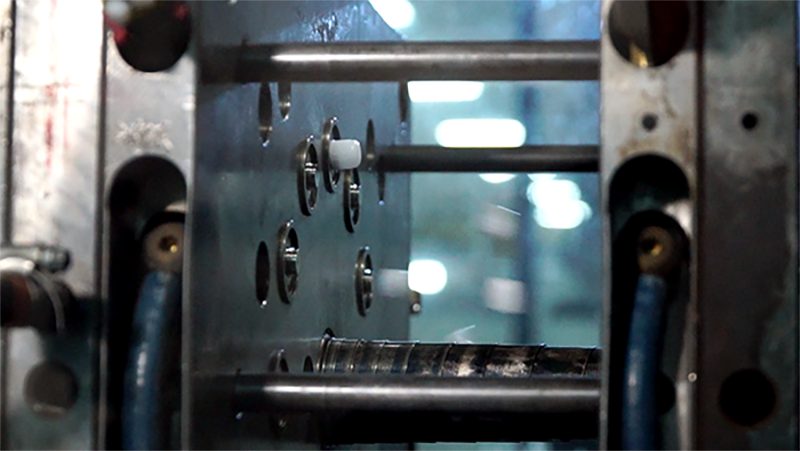
- When a part feature requires a hole, slot, or undercut not perpendicular to the parting line
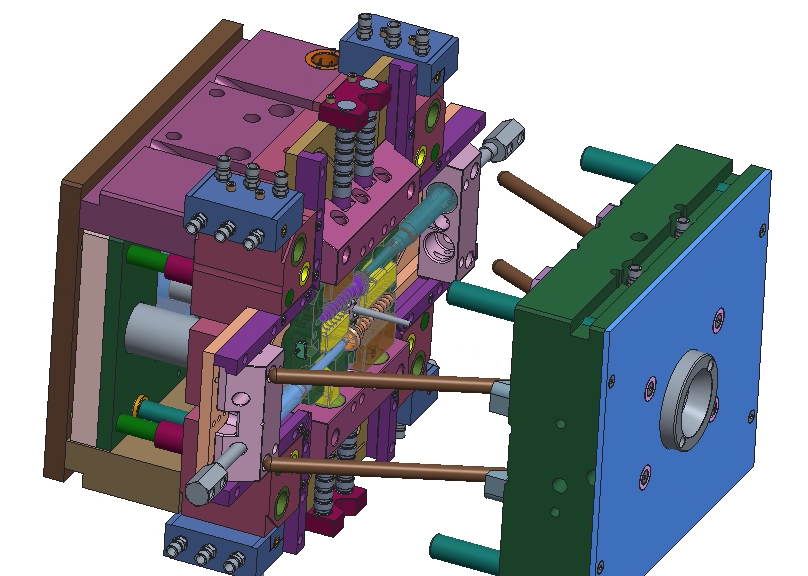
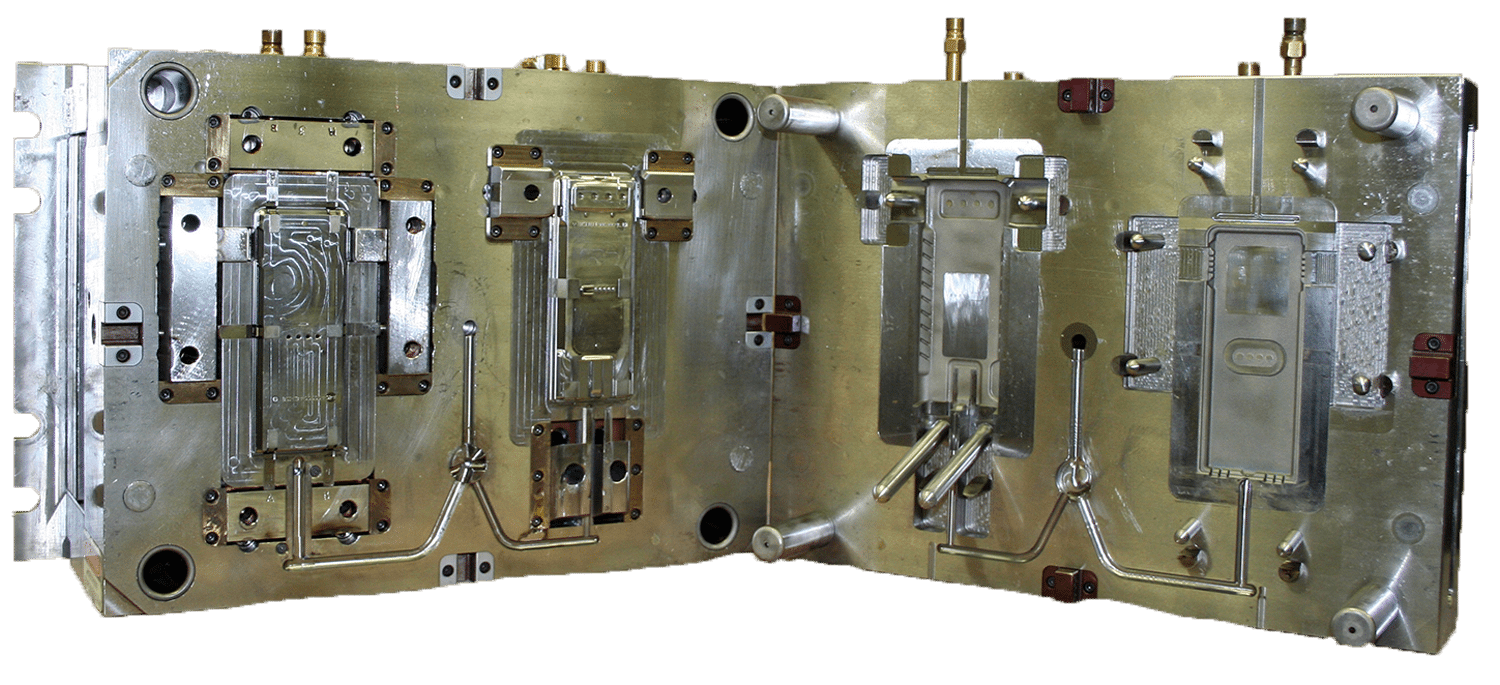
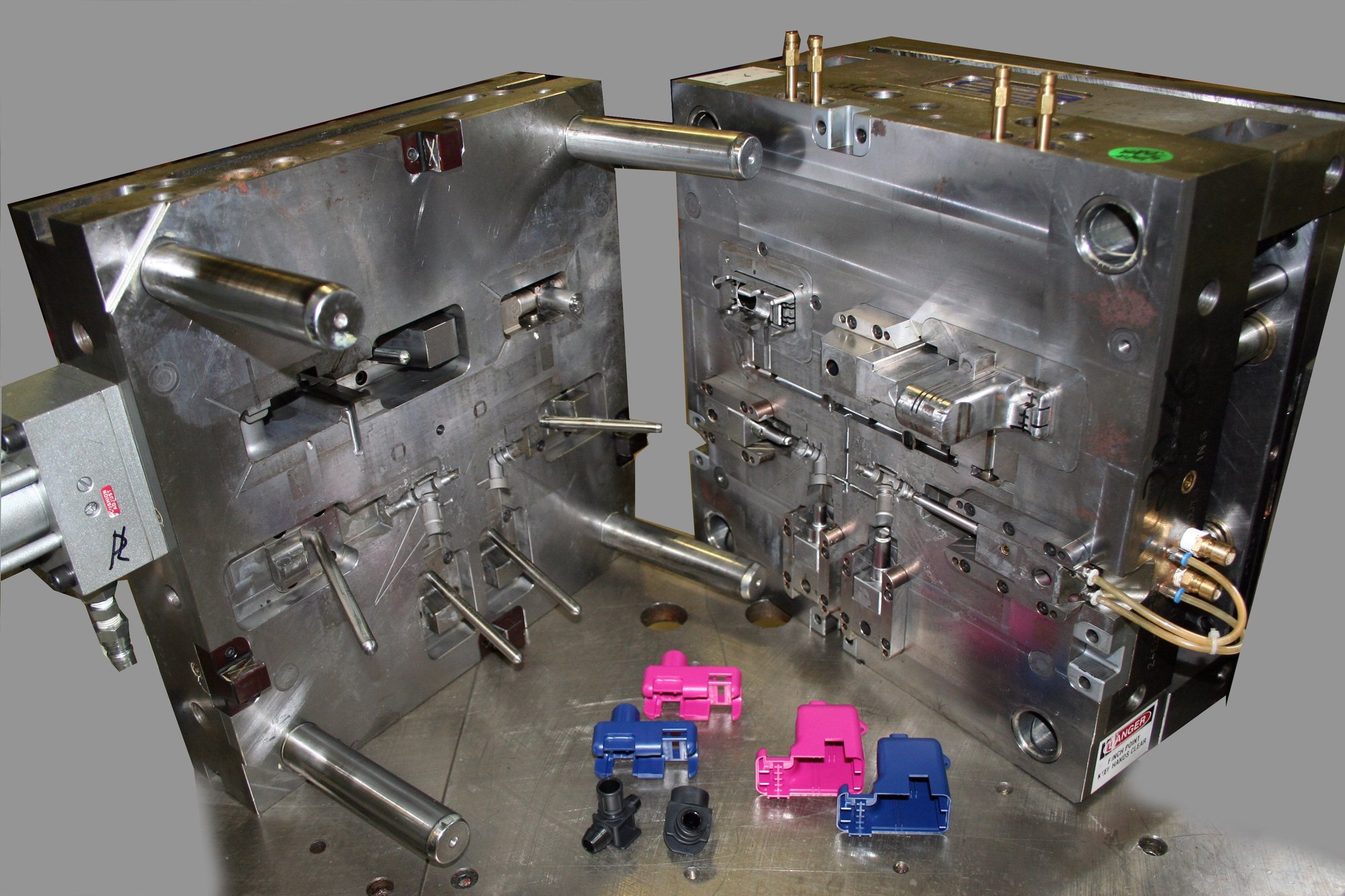
- Cost saving tooling solution
- a stand-alone or dedicated mold base is not required
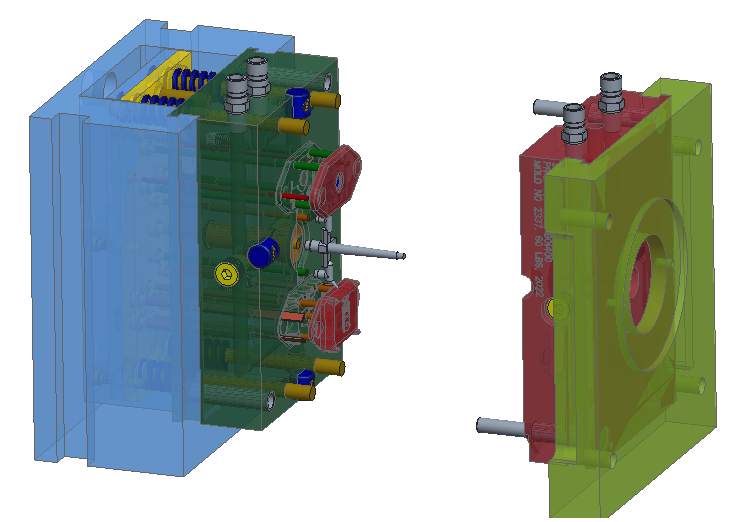
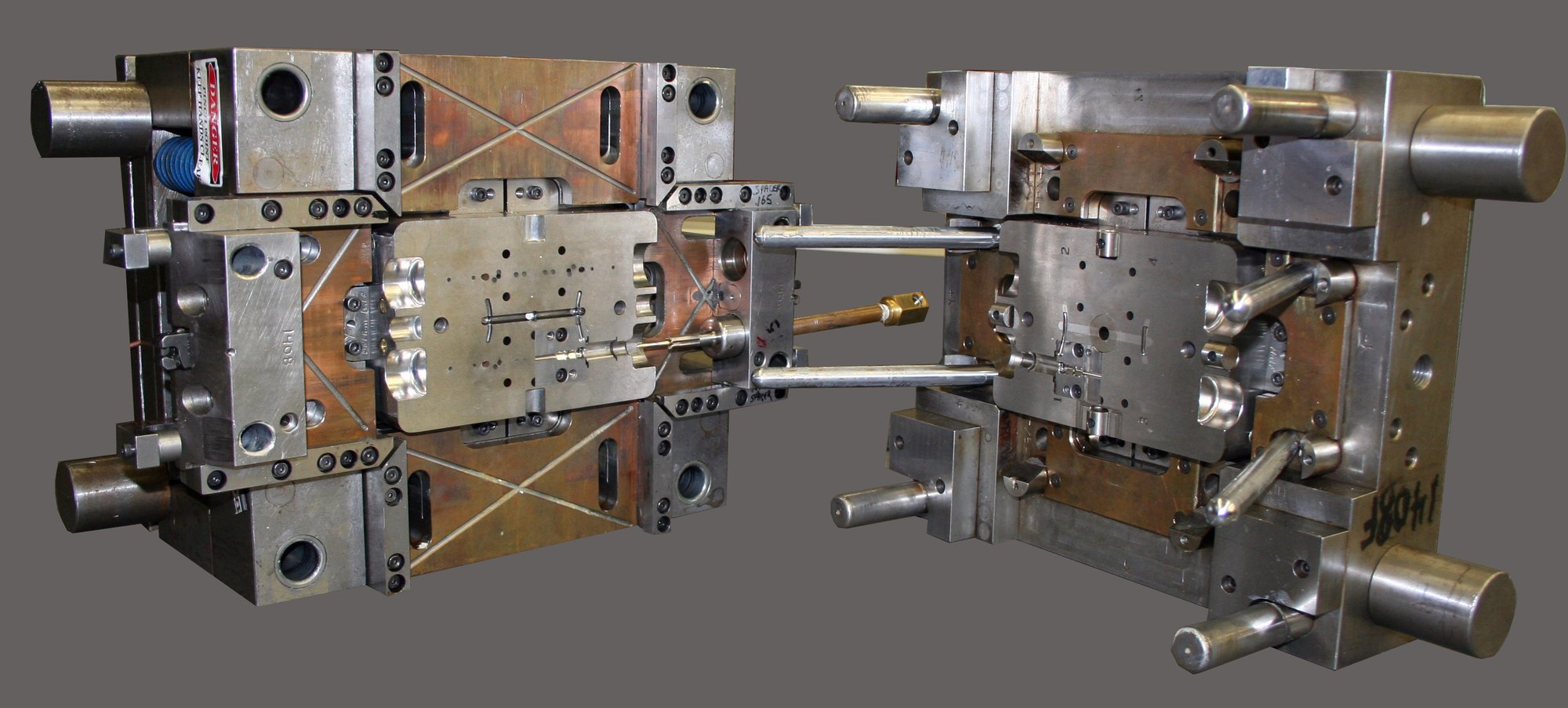
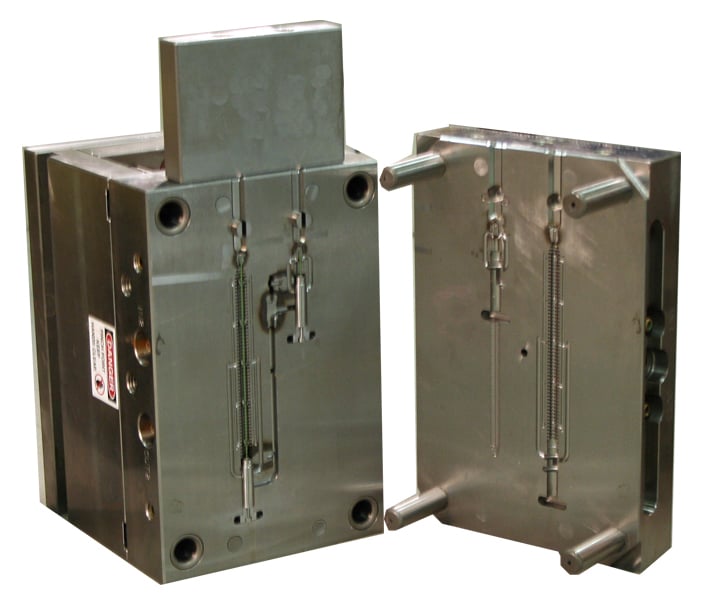
"Our experience has taught us how to build and maintain the highest quality injection molding tools to ensure the production of the highest quality plastic components."
Crescent Team
Protecting Your Plastic Injection Mold Investment
Preventative Maintenance Schedule

Electronic Documented mold maintenance schedule specific to your tool

Based on a set number of cycles

Inspects, cleans and performs standard maintenance
Resources
Imagine the power of having industry-leading expertise at your fingertips. Our Resource Page is a comprehensive hub dedicated to injection mold building and molding services. It's packed with informative articles, insightful videos, case studies, and in-depth guides that will turn complexity into clarity.
Go to the Resource Center
Why Choose Crescent?
Discover the countless benefits of partnering with us for all your injection molding manufacturing needs and let us show you why we are the perfect match for your business.