Custom Swiss Screw Machining
Crescent Industries manufactures precision Swiss screw machined components.
We offer these services for either finished products or as inserts for the insert molding process. Our Swiss-screw machining services allow us to support a broad array of materials and industries we serve, with high surface finishes and tighter tolerances. Our capabilities allow for larger diameter bar stocks (up to 3″) available in various materials, which include Monel™, Brass, Molybdenum, Copper, Plastics, Nickel/Nickel Alloy, Titanium, Bronze, Aluminum, and Stainless Steel. We also offer finishing services for machined parts such as passivation, deburring, plating, laser etching, anodizing, assembly, and packaging.
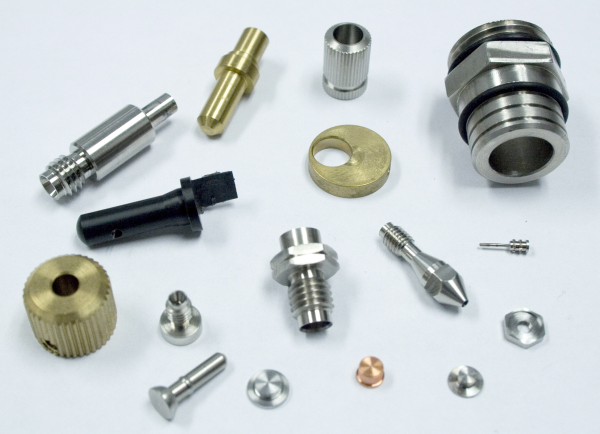
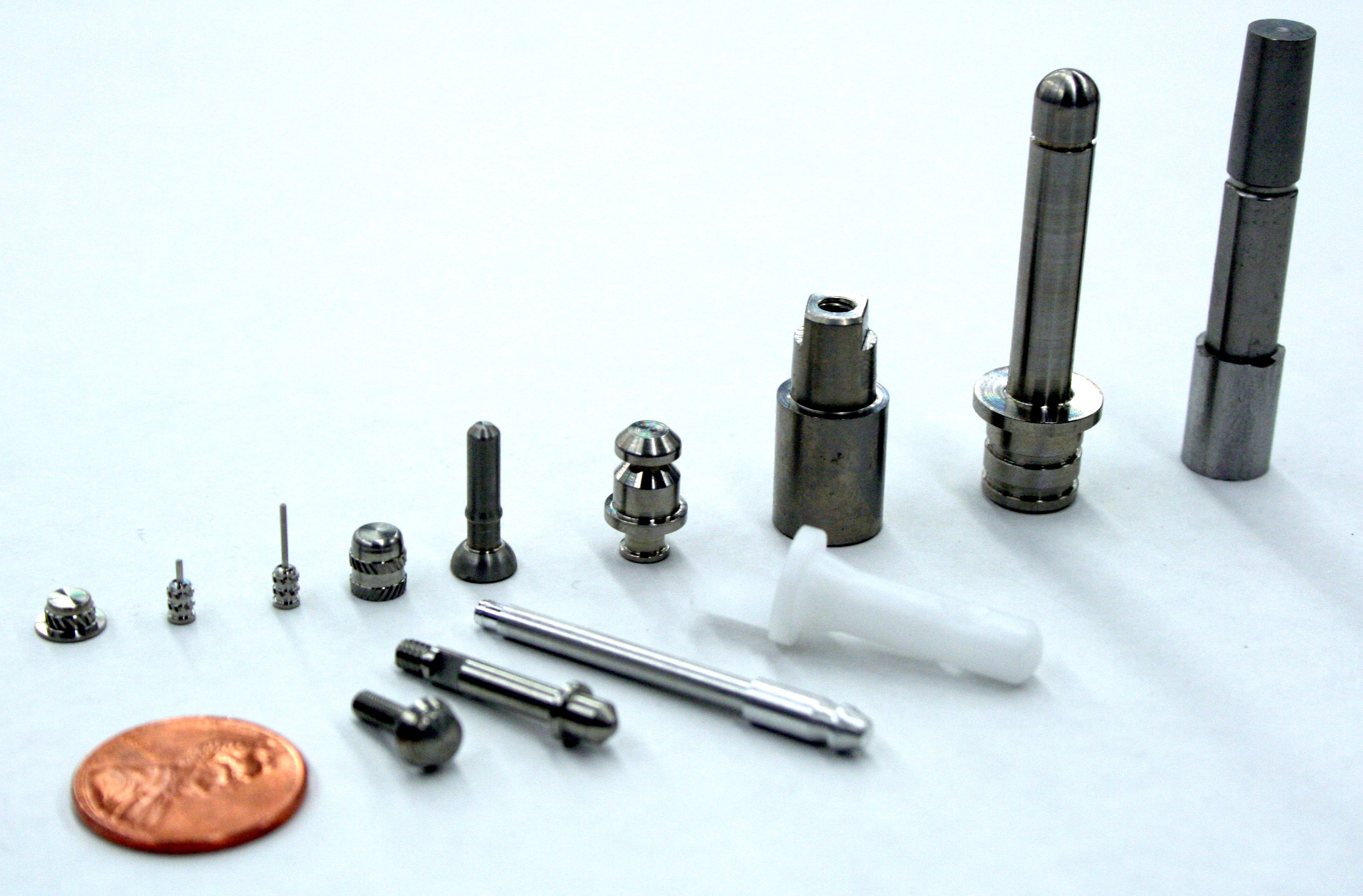
TYPES OF SWISS SCREW MACHINED COMPONENTS
The custom inserts come in a diverse range used in various critical plastic components. Examples include housings, instruments, knobs, and electrical devices used in the medical, pharmaceutical, dental, defense, and industrial markets.
- Rivets
- Fasteners
- Clips
- Pins
- Bushings
- Tubes
- Magnets
- Screws
- Studs
- Contacts
- Spring Contacts
- Surface Mount Pads
INTEGRATED MANUFACTURING SOLUTION
With over seven decades of experience in machining and injection molding, Crescent Industries has honed its expertise in delivering manufacturing solutions that are tailored to your unique needs. We harness the power of engineering, technology, and an unwavering commitment to quality and exceptional service standards to ensure that every job is completed to your utmost satisfaction.
We invite you to explore our comprehensive range of injection mold building solutions, injection molding operations, and post-processing services, all designed to provide a personalized experience at every step of your project.
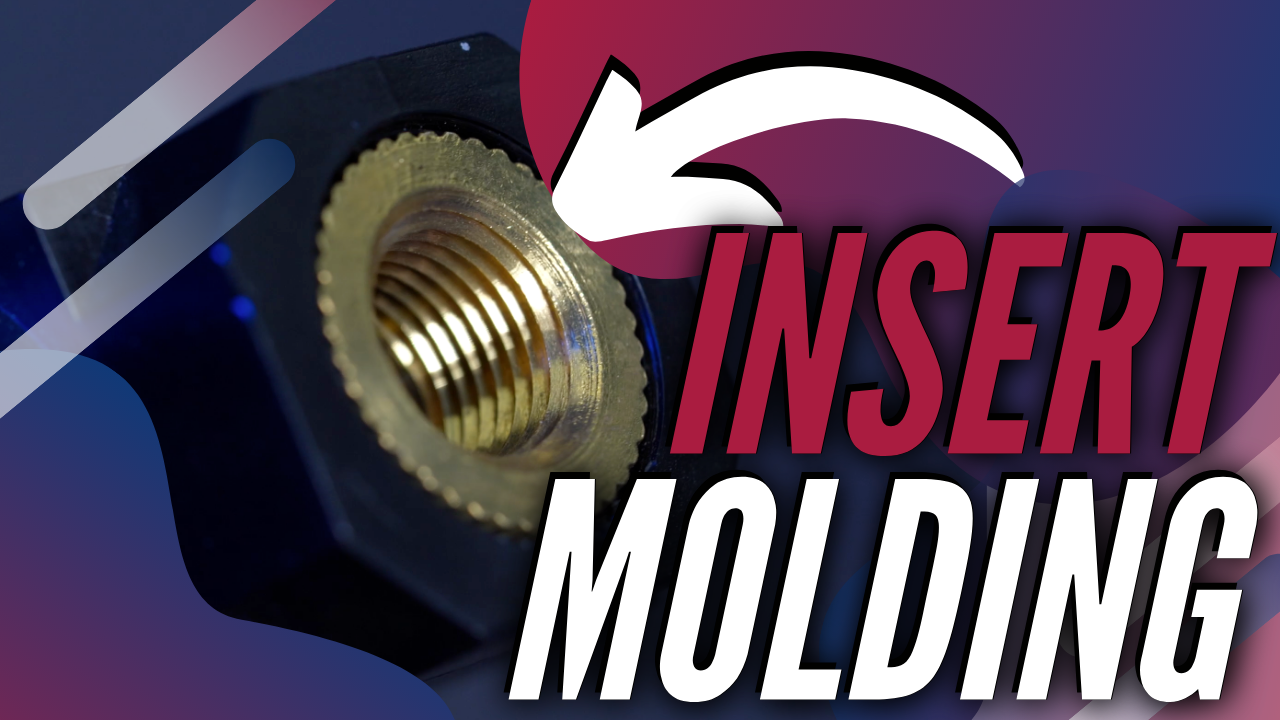
SECONDARY OPERATIONS FOR INJECTION MOLDED PROJECTS
- Device Assembly
- Ultrasonic Welding
- Solvent or UV Bonding
- Heat Staking Inserts
- Annealing
- Vacuum/Pressure Testing
- Sterilization Ready
- Cap Lining
- Product Kitting
- Product Packaging
- Pad Printing
- Inkjet Printing
- Laser Marking
- EMI or RFI Shielding
- CNC Machining
- Ultra-Sonic Cleaning
Why Choose Crescent?
Discover the countless benefits of partnering with us for all your injection molding manufacturing needs and let us show you why we are the perfect match for your business.