The Role of injection molding experts in product success
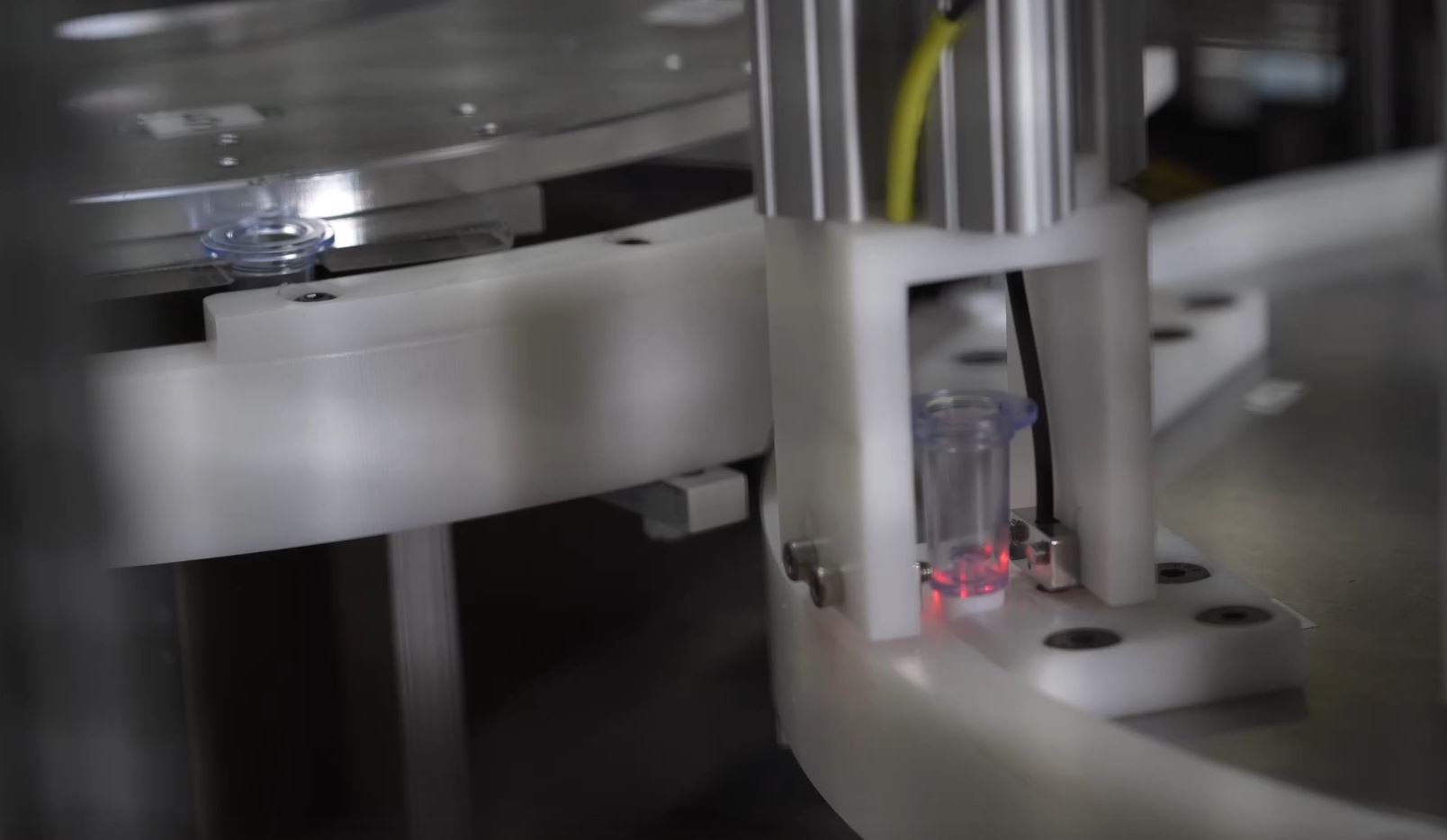
HOW INJECTION MOLDING EXPERTS CAN MAKE A DIFFERENCE
In the complex manufacturing world, injection molding experts stand as the transformative force driving product success. Despite seeming basic, the injection molded plastics are often intricately designed with a wealth of technical expertise.
The final plastic component often results from a meticulous process that includes the inception of an idea, material selection, initial draft, simulation, improvement, mold design, tool production, final production, and post-processing. This smooth intricate process is the culmination of decades of injection molding experience our highly trained designers and engineers have, emphasizing the indispensable role of skilled personnel.
For Original Equipment Manufacturers (OEMs) seeking quality plastic products, the need to partner with an expert injection molding company becomes evident. Successfully completing a production job depends on finding the right combination of expertise under one roof. From mold designers, engineers, and quality inspectors, every member utilizes their knowledge to produce and assess diverse plastic parts efficiently.
THE PROJECT MANAGEMENT OFFICE
Project management poses challenges in any industry, but it is particularly crucial in injection molding. Implementing Project Management Offices (PMOs) has become commonplace in this sector, ensuring rigorous oversight, adherence to policies, and meticulous monitoring of processes. As we navigate the complexities of injection molding, it's essential to highlight the indispensable role the PMO plays in steering projects to successful completion.
Role and Functions of the PMO
PMO in injection molding plays a pivotal role in ensuring the smooth execution of projects. It comprises a team of professionals focused on defining the project scope and upholding product quality standards. Each member has a specific role to ensure project success, such as:
- Project Manager: Acts as the primary client contact, overseeing the project's overall objective, cost, and duration. They are responsible for tracking and reporting progress, ensuring the team adheres to the agreed schedule.
- Mold Designer: Plays a crucial role in conducting design for manufacturing, simulation, and mold design.
- Tool Builder: Constructs the injection mold tooling according to the provided design.
- Process Developer: Offers support in simulation and develops the molding process based on scientific principles. This expert also executes the initial Design of Experiments (DOE), Operational Qualification (OQ), and Performance Qualification (PQ) for process validation.
- Manufacturing Support: Represents the manufacturing team. This member provides valuable insights for design improvements and facilitates the implementation of automation for enhanced productivity.
- Quality Engineer: Takes charge of developing quality inspection plans and creating validation protocols. They generate dimensional outputs from DOE, IQ, OQ, and PQ validation needs.
Below is further insight into some of the team’s key functions.
Project Requirement Analysis
One of the foundational tasks of the PMO in injection molding is conducting a comprehensive analysis of project requirements. This role involves carefully examining the specifications and parameters outlined for the injection-molded components. The PMO collaborates closely with key stakeholders like the client, injection molding experts, designers, and engineers, to understand the intricacies of the project.
By analyzing the requirements, the PMO establishes a clear roadmap, outlining the necessary steps for design, material selection, and manufacturing processes. This analytical phase provides the basis for informed decision-making throughout the project lifecycle.
In the context of injection molding, project requirement analysis delves into the unique characteristics of each component. Factors like material properties, dimensions, and intended function are scrutinized to align the project with the highest standards.
Through effective communication and collaboration, the PMO ensures that all stakeholders comprehend the project's intricacies and work collectively towards a unified goal.
Schedule and Quality Management
The PMO also plays a pivotal role in schedule management, crafting timelines that harmonize with the complexities of injection molding processes. Time is a critical factor in manufacturing, and the PMO ensures that project milestones align with production efficiency. The team establishes realistic timelines for design, prototyping, tooling, and production. Accounting for potential challenges and unexpected variables that may arise during the injection molding process further helps with time management.
Quality management is another function of the PMO as the body intervenes at various stages of the injection molding process. From material selection to final product inspection, the PMO oversees the implementation of rigorous quality control measures. This involves setting quality standards, conducting regular audits, and ensuring compliance with industry regulations.
The experts help determine dimensional accuracy, material consistency, and other critical quality parameters. By integrating quality management into the project lifecycle, the PMO upholds the reputation of injection-molded plastics for reliability and durability.
design for manufacturing
DFM emerges as another critical cornerstone when covering the details of injection molding. Below we’ll explore its definition, significance, and the meticulous processes and checklists that guide its implementation. Additionally, we’ll cover the relationship between DFM and mold design, exploring advanced simulation techniques that elevate the precision of injection molding projects.
Why Is DFM Crucial?
DFM is important in injection molding as it bridges the gap between design intent and manufacturability. By incorporating DFM principles early in the design stage, we can identify potential challenges related to materials, tooling, and production processes and address them quickly.
This step reduces defects and ensures a smoother, more cost-effective manufacturing process. DFM is a strategic production tool that enables designers and engineers to collaborate to create products that align with both creative vision and practical feasibility.
DFM Process and Checklists
The DFM process begins with a meticulous examination of the product design, scrutinizing its elements for compatibility with the injection molding process. This involves evaluating features, such as wall thickness, draft angles, and undercuts, ensuring they adhere to manufacturing constraints. We’ve developed DFM checklists at Crescent Industries with over 40 parameters that serve as guides during this assessment.
DFM checklists cover critical elements such as part complexity, ensuring that intricate designs do not compromise manufacturability. They also address material selection, guiding designers toward choices compatible with the injection molding process. Part design considerations like including draft angles and eliminating sharp corners, are essential in optimizing the production process and reducing the risk of defects.
Mold Design and Simulation Techniques
DFM extends its influence into mold design. The synergy between DFM and mold design ensures that the intricacies of product designs seamlessly translate into mold structures. Advanced simulation techniques, such as mold flow analysis and computer-aided engineering (CAE), play a crucial role in this phase.
Mold flow analysis simulates the flow of molten material within the mold, identifying potential issues like air traps and weld lines. CAE facilitates the optimization of mold design, ensuring it aligns with DFM principles and enhances the efficiency of the injection molding process. Incorporating DFM principles with advanced simulation techniques in mold design elevates the precision and effectiveness of injection molding.
robust process development for plastic components
The intricate product development journey reveals injection molding specialists as the often-overlooked architects of product success. Imagine the sleek contours of your favorite gadget or the durable plastic components within your everyday items. These essentials owe their existence to the finesse of plastic injection molding. This article explores the invaluable contributions and technical expertise of Crescent Industries, one of the most renowned injection molding companies.
Insight into expert plastic injection molding is incomplete without covering process development and validation. This critical phase helps guarantee the efficiency of the manufacturing process and the precision of the final product. This section covers roles and approaches to process development and quality assurance.
Process Development and Quality Assurance
Process development in injection molding is a critical endeavor that requires a keen focus on product quality assurance. It involves a systematic approach to refining and optimizing each stage of the molding process to achieve consistent and top-quality products.
Quality assurance protocols are integrated into the development process to ensure that the final product meets strict standards.
Molding Process Validation and Protocol
Molding process validation is a critical step in ensuring the reliability and repeatability of the injection molding process. It involves the systematic collection and analysis of data to verify that the molding process consistently produces components that meet predetermined specs.
The validation protocol includes a series of evaluations such as dimensional checks, material properties verification, and functionality testing. This rigorous validation process ensures the injection molding process is capable of consistently delivering components that meet strict standards.
First Article Inspection Report (FAIR) and Capability Studies
The First Article Inspection Report (FAIR) is a comprehensive verification process conducted on the initial production run. It provides a detailed overview of the inspection of the first set of components produced to ensure they conform to the specified requirements. This meticulous examination includes dimensional checks and aesthetic assessments.
Capability studies complement the FAIR by offering a statistical analysis of the process's ability to produce components within specified tolerances consistently. FAIR and capability studies provide valuable details into the process's abilities and provide a baseline for comparing subsequent production runs.
Production Quality Approvals (PQ) and Their Impact
Production Quality Approvals (PQ) are significant milestones in the plastic injection molding process. They signify that the validated process is ready for full-scale production. These approvals are granted after successfully completing rigorous testing and validation protocols. They ensure that the manufacturing process consistently meets quality standards.
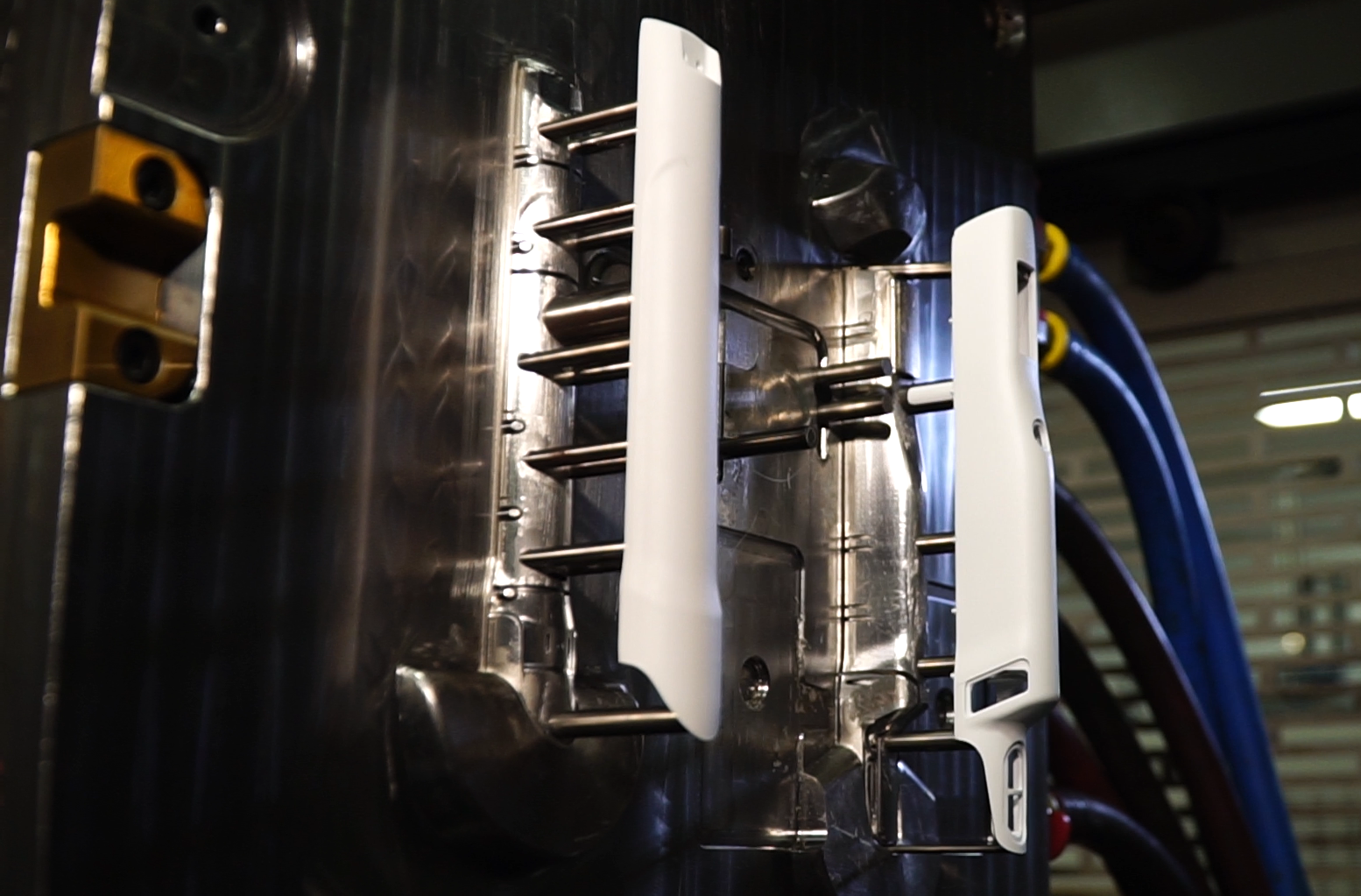
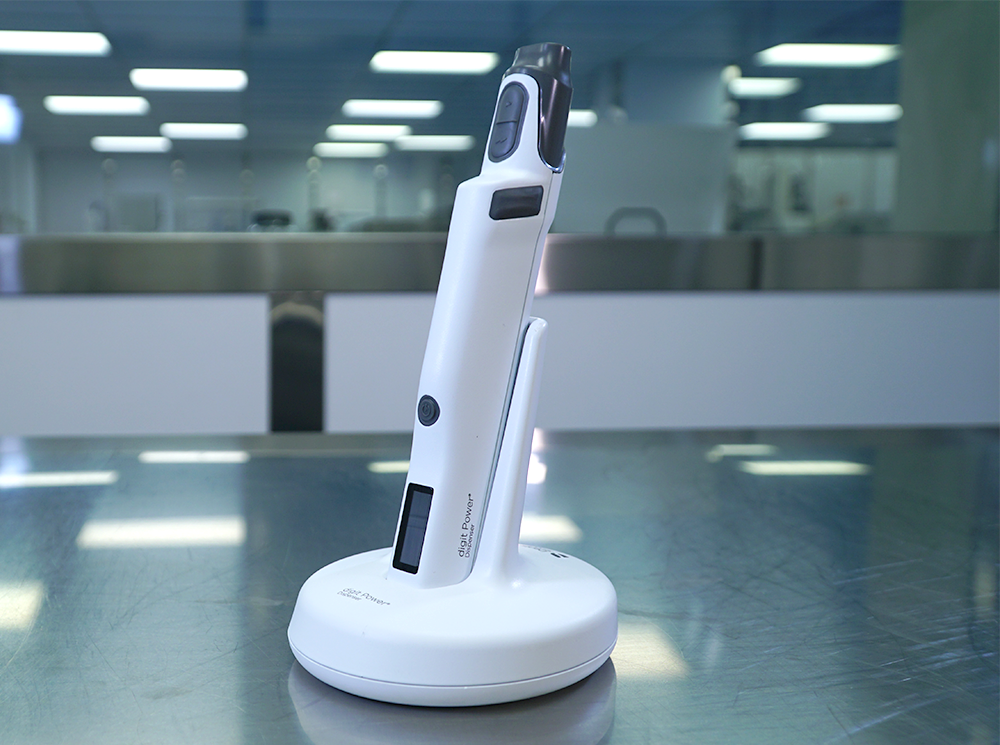
crescent industries approach to injection molding
We at Crescent Industries take up injection molding projects with a commitment to innovation, precision, and client satisfaction. At the forefront of our strategy is a proactive stance on embracing cutting-edge technologies and methods. Integrating the latest equipment and leveraging R&D initiatives, position us as a leader in the industry.
The approach further emphasizes a collaborative partnership with clients, where open communication and a deep understanding of project requirements guide the molding process. Quality assurance is another crucial component as our strict validation protocol ensures each component meets the highest standards. The molding company’s commitment extends beyond manufacturing. We are dedicated to providing comprehensive solutions, from design optimization through production, that align with the dynamic needs of diverse industries.
Leverage 75 Years of Expertise
Our exploration of the intricate world of injection molding reveals the various processes and technologies that underlie the success of projects across industries. The pivotal role of injection molding experts, PMO, DFM, and additive manufacturing guarantee each meticulous step in process development and validation are executed seamlessly. Crescent Industries' 75 years of expertise stand out in this sector, championing innovation, collaboration, and quality assurance.
Why Choose Crescent?
Discover the countless benefits of partnering with us for all your injection molding manufacturing needs and let us show you why we are the perfect match for your business.