Plastic Injection Mold Design
Crescent’s Injection Mold Design & Engineering Support
At Crescent, we provide high-quality upfront engineering support, starting with efficient injection mold designs. With our expertise and cutting-edge technology, we strive to deliver tailored solutions to meet your project requirements. Whether you want to create a new product or improve an existing one, our team is here to assist you at every step.
Design for Manufacturing (DFM)
Our designers have a deep understanding of injection molding and mold building processes and best practices. We optimize the mold design for easy fabrication, efficient production, and cost-effectiveness by considering factors that align with injection molding best practices.
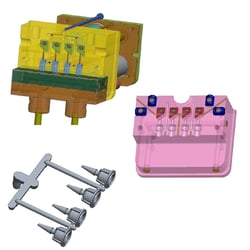
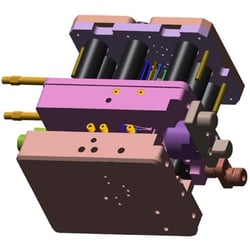
3D Modeling
Creating 3d models of the injection mold design allows the team to visualize the mold’s geometry, identify potential manufacturing issues, and make necessary adjustments before the steel is cut to build the tool.
Tooling Design
Our team has extensive experience designing various injection molds, including single-cavity molds, multi-cavity molds, family molds, tool sets, and hot runner molds. To develop an efficient and robust tooling design, we consider factors such as part geometry, draft angles, gate locations, and cooling systems. We aim to maximize productivity and ensure consistent part quality throughout the production process.
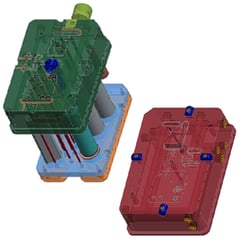
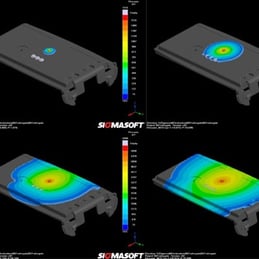
Mold Flow Analysis
We conduct mold flow analysis using specialized software to ensure optimal mold performance. This analysis allows us to simulate the flow of molten plastic inside the mold, identify potential defects or issues, and optimize the design accordingly, all before the steel is cut, saving you time and money.
Resources
Crescent Case Studies
How Design for Manufacturing Solved Quality Issues
The Challange
The Solution
By using DFM and 3D printing, we were able to speed up the prototyping process and respond quickly to our client's input, moving beyond the limitations of traditional 2D drawings and 3D models.
Mold Design & Build for Surgical Device Manufacturing Efficiency
The Challange
Our client wanted to mass-produce their complex orthopedic surgical device. The device required intricately designed components that demanded exceptional precision and quality to ensure the parts fit together seamlessly.
The Solution
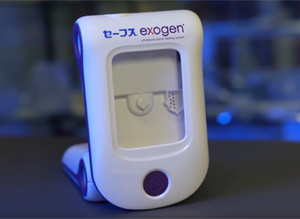
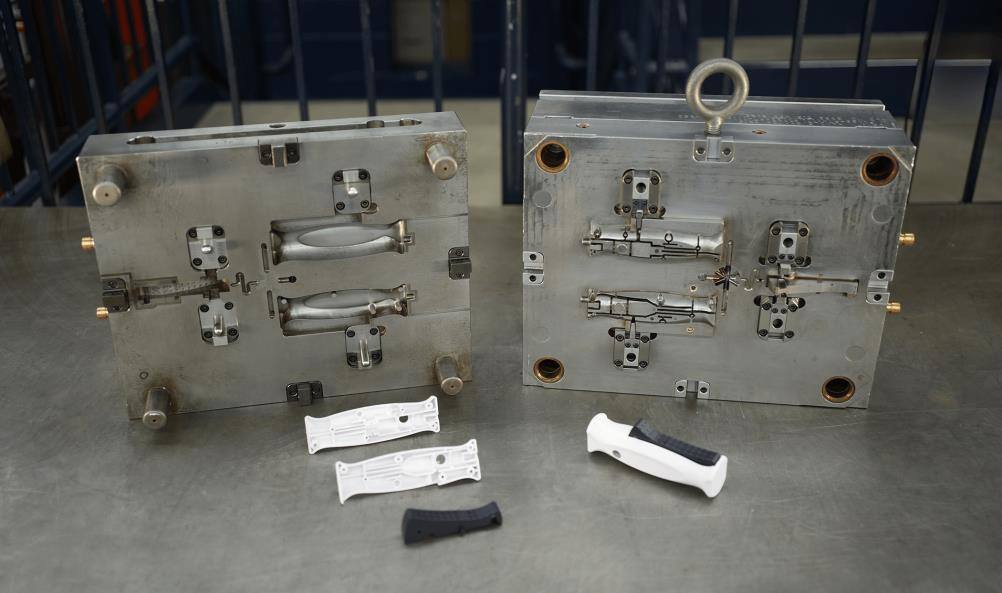
Serving the Following markets
Why Choose Crescent?
Discover the countless benefits of partnering with us for all your injection molding manufacturing needs and let us show you why we are the perfect match for your business.