From Concept to Reality:
Crescent Industries' Role in Mass Producing a Medical Device
Demonstrates Crescent's Capabilities from the Design Phase to Full Production
THE CHALLENGE
Our customer faced the complex task of scaling their 3D-printed ProPatch patient monitoring device prototype for mass production. This device required a sophisticated assembly process that included electronic components. They needed a partner who could provide Design for Manufacturability (DFM) support to ensure moldability and efficient production. The customer sought a manufacturing partner capable of managing the entire process, from tool building to molding and assembly.
THE SOLUTION
Crescent's exceptional expertise in injection molding and comprehensive manufacturing processes made us the ideal partner for this project. Our extensive support, which included the DFM process, mold design and building, and final production, streamlined Lifeware Labs' supply chain and facilitated a smooth transition from prototype to mass production. This collaboration resulted in an initial production volume of hundreds of units, targeting the U.S. Military and domestic first responders with the ProPatch device. Explore more into this process....watch the video!👉
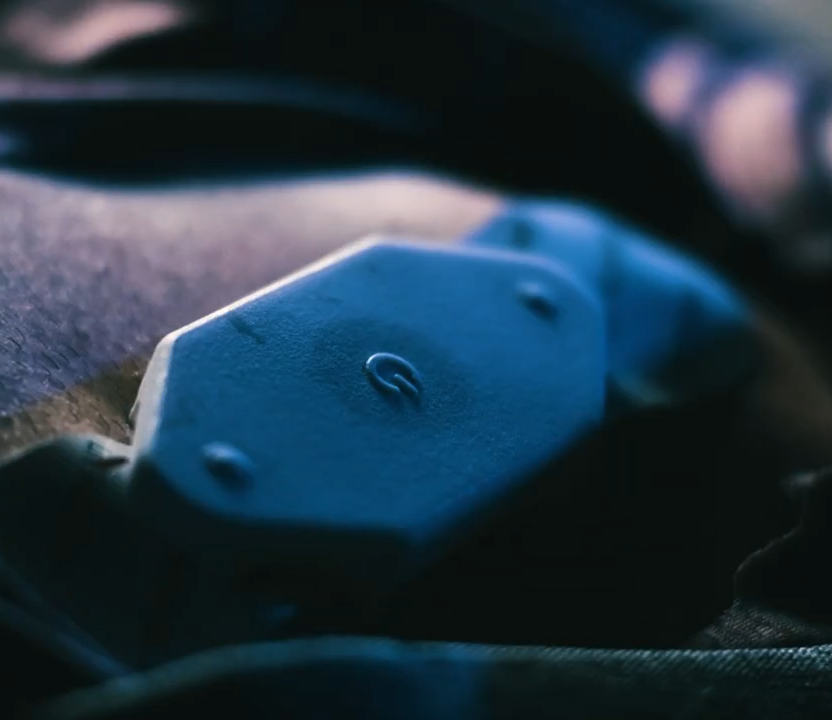
The Process: From the Early Design Stages to Production Launch
-
Why Did You Choose Crescent?
Crescent's expertise in injection molding and comprehensive manufacturing capabilities made them a compelling choice. According to Alexi Harlambidis, CEO and Co-founder of Lifeware Labs, "I think one of the main reasons we went with Crescent is we got the sense early on that Crescent would at least help answer some of the questions we didn't even know to ask. And that's huge when you're a small startup."
-
Early Engagement with Crescent
The customer was excited about a captivating 3D prototype, yet they faced a critical challenge ahead. The intricacies of assembly and the delicate electronics nestled within their design posed a hurdle they couldn't tackle alone. Determined to bring their vision to life on a larger scale, they sought a partner who could provide expert design-for-manufacturing support.
-
What The DFM Process is Like at Crescent
Crescent's ability to provide foresight for assembly design and markings to accommodate the electronics inside the part made the transition to production and assembly smoother.
The DFM process was particularly helpful, as Crescent's team explained the reasoning behind each design choice, giving Lifeware Labs valuable insights into designs for function and manufacturing.
-
Why is Having a Partner that Builds Tools and Performs Injection Molding a Benefit?
This was a benefit to the customer to provide a "one-stop-shop" and simplify their supply chain and feel confident that in production the assembly and manufacturing would be smooth and easier with the electronics.
-
What's the Injection Mold Building Process Like at Crescent?
Once the mold design receives approval, Crescent expertly handles the construction of the injection mold. Our team is committed to maintaining close collaboration with our customer, ensuring seamless preparation for production upon the tool's completion.
-
Customer's Testimonial
Alexi Harlambidis emphasized the importance of the human aspect of this partnership, saying, "Life is more enjoyable when you're working with people that you like to work with. The human aspect of it, I think can't be understated because you spend a lot of time with them. It's invaluable to me."
Why Choose Crescent?
Discover the countless benefits of partnering with us for all your injection molding manufacturing needs and let us show you why we are the perfect match for your business.