DESIGN FOR MANUFACTURABILITY CASE STUDY
Learn how DFM Solved Quality Issues for a Client's Medical Device
Crescent Industries was approached by a medical product company that needed help with an existing medical device. The device uses ultrasonic technology to aid in healing broken bones, so a quality product was necessary. The company experienced significant quality issues during the manufacturing process, and Crescent helped resolve these issues.
After learning about the product and some discussions with their team of engineers, we mutually determined that the current injection molding process was the root cause of the quality issues. Crescent developed a new manufacturing approach for this device; our steps included revising the product design to fit the manufacturing process, designing and building new tooling, implementing ultrasonic welding and part decorating in one continuous manufacturing process.
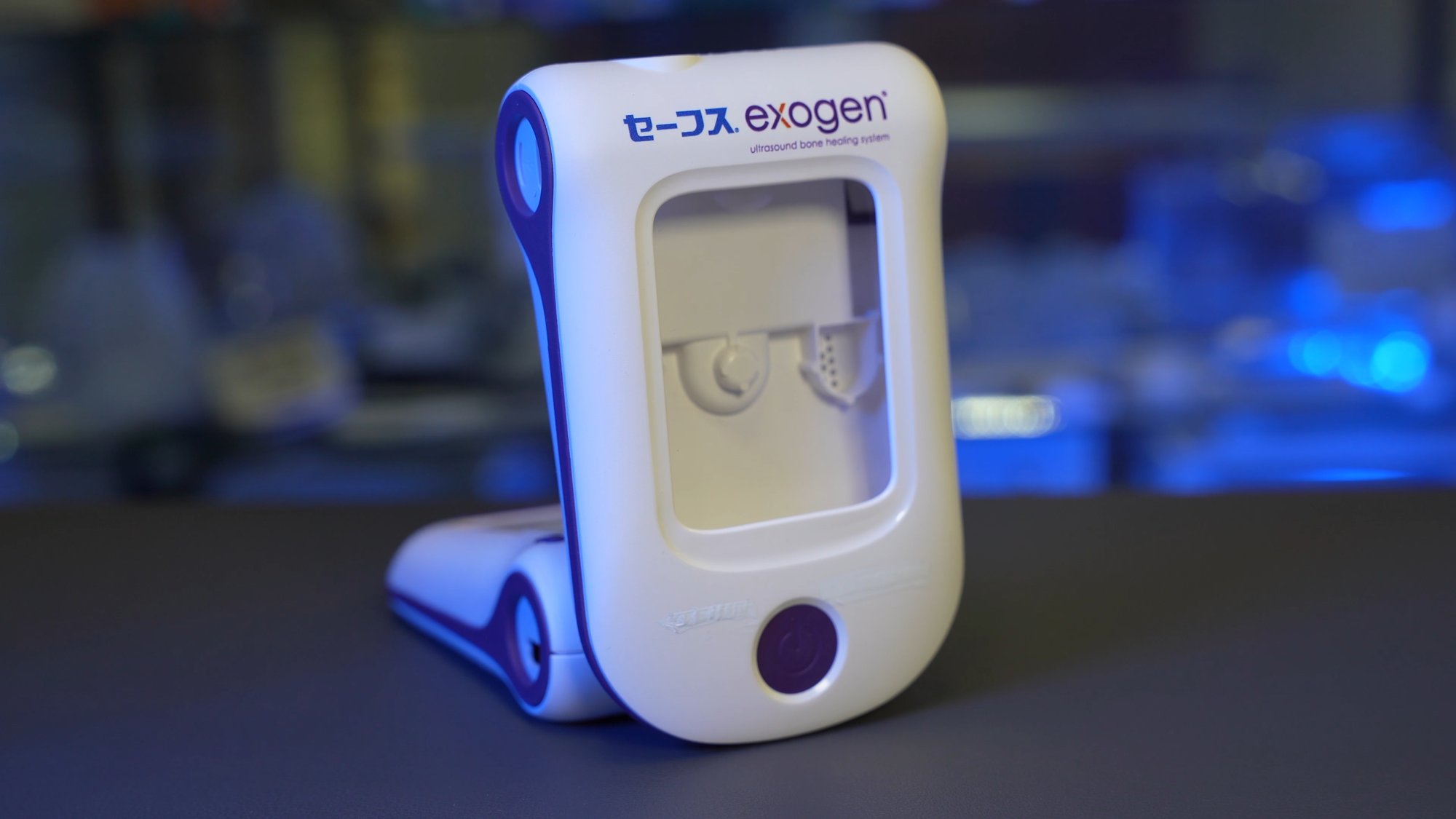
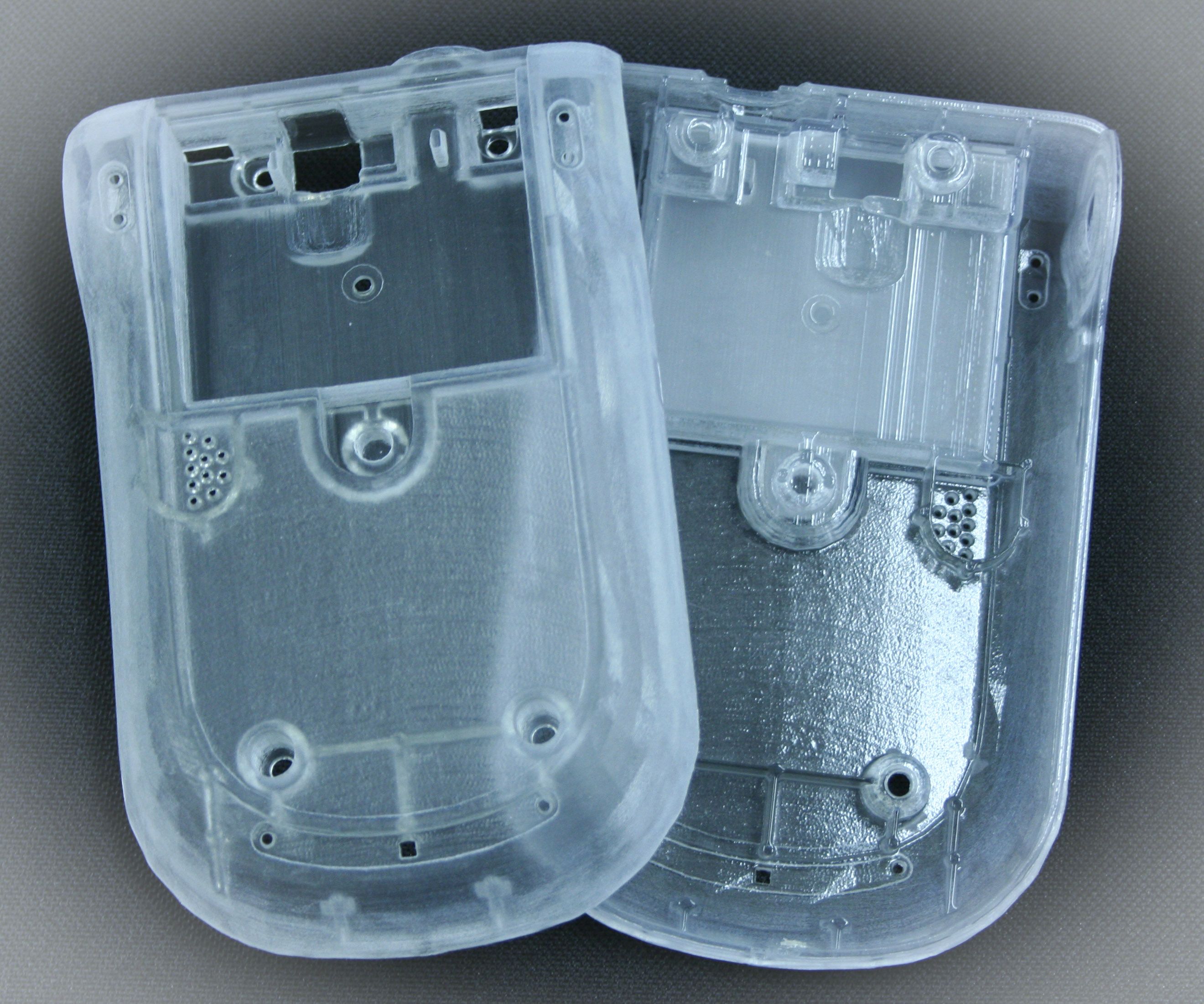
-
Updated Part Designs
The first step of the DFM process included updating the design. But the problem was the client's legacy data - the engineers that developed the original product were no longer with the company, and the CAD solid models for the device were no longer in a state that could easily be modified. Our design engineers created new part design models to match the new manufacturing approach. To give the customer the ability to test and review the new design, we produced 3d printed parts to use as prototypes to test form, fit, and function.
-
3D Printed Prototypes
DFM and 3D printing allowed Crescent to speed this prototyping process up and respond very quickly to the customer's input and direction, rather than relying on only 2D drawings and 3D solid models. Using the 3d printed parts in their completed product assembly as if they were assembling and testing a unit that had gone through the entire manufacturing process. This approach shortened the time necessary to traverse the redesign process and assured the customer they would be receiving a finished medical device that fit their functional and quality requirements. -
Crescent's engineering team works as an extension of yours!
Crescent offers Design for Manufacturability feedback; we provide crucial guidance on materials and part features at the earliest design stages. Our engineers incorporate 3d mold fill simulation into their expert DFM analysis. Identifying design and manufacturing issues early to prevent costly inefficiencies in production and predict quality issues, so modifications to the part, tool, or manufacturing process happen at this early stage of development.
Why Choose Crescent?
Discover the countless benefits of partnering with us for all your injection molding manufacturing needs and let us show you why we are the perfect match for your business.