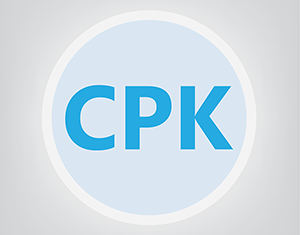
Why CpK is Used in the Custom Plastic Injection Molding Process
In any manufacturing process, there is bound to be built-in variance from cycle to cycle. Even in automated, carefully controlled processes, variance is a natural occurrence. Fortunately, manufacturers have several tools at their disposal to understand the level of variance present, to determine whether it will fit within acceptable tolerance requirements, and to make adjustments as necessary.
Depending on the end use of a molded project, part tolerance requirements can differ greatly. For consumer products, some degree of variance from piece to piece or cycle to cycle is unlikely to make much of a difference to the end user. In critical applications like military, pharmaceutical, and medical components, however, a high degree of accuracy and consistency is required, so injection molding tolerances must be tighter. Process control is the means of monitoring, measuring, and adjusting manufacturing processes to meet customer requirements.
Injection Molding Process Capability Measurements
Injection molding process capability is measured in a variety of ways, using numerous acronyms. The most common ones are Cp and CpK (which are process capability measurements) and Pp and PpK (which are process performance measurements).
The difference between process capability and process performance is based on the amount of historical data available. Process performance depends on historical process data and analysis. Process capability is used for newer equipment or processes where historical data is not as plentiful. Process performance is strictly a measure of past performance, while process capability provides insight into the current and future performance capabilities of the process. In this piece, we will focus on Cp and CpK.
Cp vs. CpK
Cp and CpK injection molding process measurements are similar in that they indicate the amount of variance present in a process. The CpK process capability measurement further measures this variance around a center point.
A useful analogy for Cp vs. CpK is to think of someone shooting a basketball. Cp would indicate how consistent each shot is, regardless of location. Since Cp does not take a centering measurement into account, we do not know whether our shooter is on target with the basket or bouncing shots high off the backboard. With CpK, we can measure the variance in each shot, as well as whether it’s going where we need it to go in the basket or not.
This illustrates why CpK is used for injection molding in most cases. Both the “location” — such as a measurement specification — and the variance are accounted for, providing insight into whether a process will meet customer requirements. When measuring CpK, a higher number is better, as it means the process can more effectively meet these requirements.
The Impact of CpK on Production
As mentioned earlier, CpK can be measured once a process has produced enough data to be considered under statistical control. CpK measurement can be used to make quick production and process decisions, such as:
- Inspection frequency: A higher CpK means that the process will need to be inspected less frequently, allowing for more machine uptime and faster production turnaround.
- Process adjustments: CpK allows operators to identify potential issues and remedy them, whether the need is to reduce variance or to recenter the process.
With accurate CpK measurement, manufacturers can produce higher-quality output with greater efficiency.
At Crescent Industries, we have been in the plastic injection molding business since 1946, continually improving and optimizing our processes based on the latest technology and scientific measurements available. We make use of scientific injection molding principles, including Cp and CpK, to ensure that we meet your needs, providing optimal quality and service. For more information, contact us today.
Resources:
Client-supplied info in a separate document – attached to the task assignment
http://www.injectionmoldingplastic.com/injection-molding-process-control.html
https://sixsigmastudyguide.com/process-capability-cp-cpk/
https://www.plasticstoday.com/injection-molding/tolerances-are-you-hitting-target-or-bull-s-eye/30117612424681
https://www.ptonline.com/articles/improving-molding-process-capability-understanding-the-pvt-graph-part-1
https://docs.oracle.com/cd/A60725_05/html/comnls/us/qa/cpcpk.htm
https://info.crescentind.com/blog/injection-molding-tight-tolerances
Topics:
Related Articles
-
Mar 19, 2025
Top 6 Advantages of Injection Molding for Your Project
Injection molding — the process of injecting molten resin into a mold — is one of the most...
-
Feb 19, 2025
Injection Molding vs CNC Machining: Which Method to Choose?
Every year, humans produce and use countless plastic products in various shapes, sizes, and...
-
Oct 03, 2024
Injection Molding Uses: Exploring Applications Across Industries
Injection molding is one of the most versatile manufacturing processes, with a wide range of...