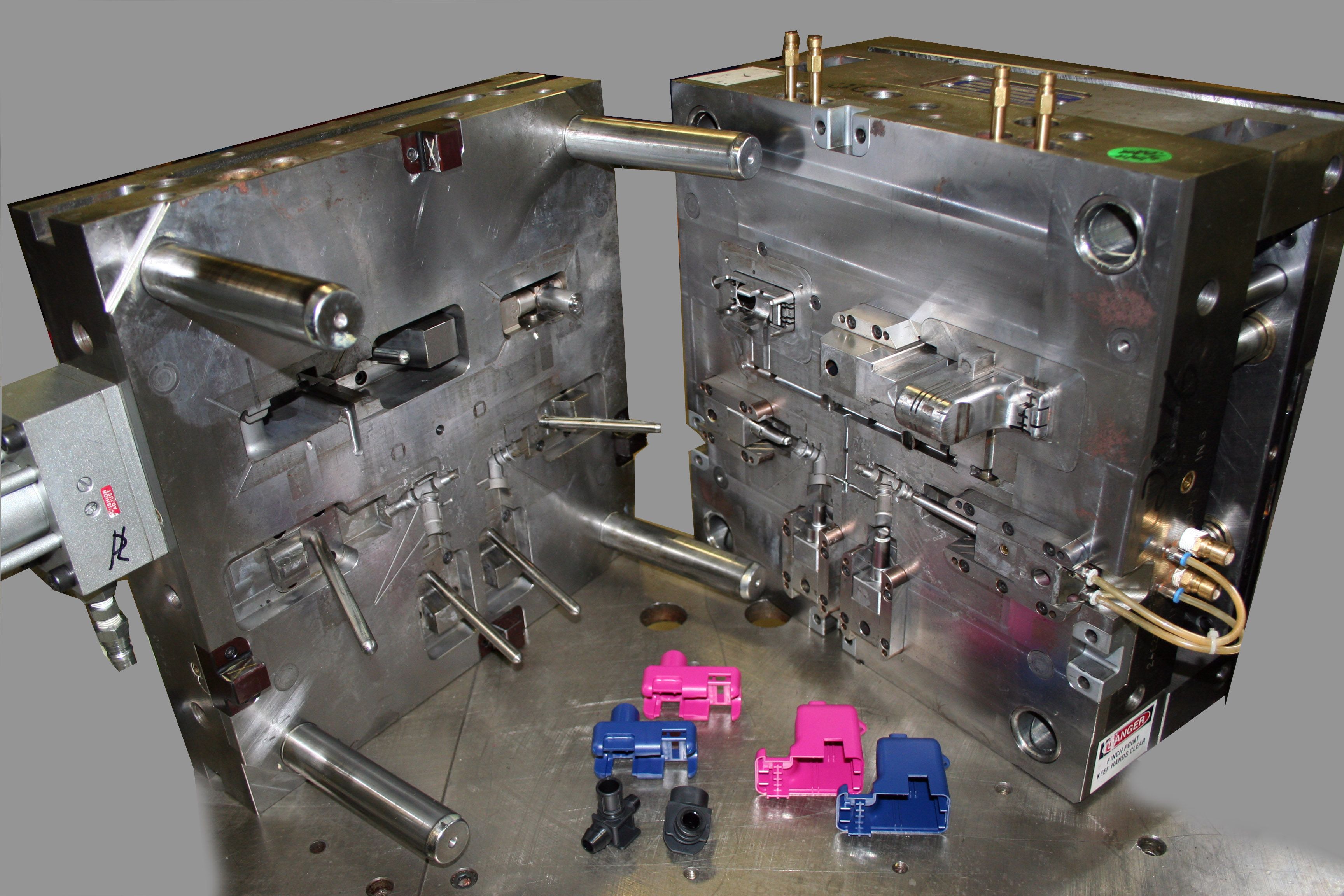
Understanding Undercuts in Plastic Injection Molding
Injection molding undercuts are features of a plastic part that are not perpendicular to the mold parting line. Because of this, they, by their design, prevent them from being ejected from the mold in the direction of the mold opening. Types of design features that may constitute injection molding undercuts include recessed areas, hooks, overhands, holes, and any other aspect of design that prevents ejection from the mold.
Throughout the rest of this piece, we will explore the most effective ways to design parts and molds to deliver features that require undercuts.
Why Undercuts Are Used in Injection Molding
Injection molding is a versatile, effective method of manufacturing high-quality parts at a reasonable cost — especially as volumes increase. Injection molding is frequently drawn upon due to the range of designs that the process can deliver — from relatively simple geometries to more complex designs, such as those requiring undercuts.
The use of undercuts in injection molding fulfills requirements that may otherwise need to be executed through secondary processes or assembly functions. For example, incorporating threading into an injection molded part design introduces an undercut feature, but prevents the need to machine threads into the plastic part post-molding.
As another example, undercuts are often used in mold designs to add assembly features to the injection molded part, allowing parts to easily and securely snap together. This eliminates the need for a secondary assembly process.
How Undercuts Affect the Injection Mold Design
Features of plastic parts that require undercuts require a more complex mold design which could include an action, lifter, handload inserts, or unscrewing cores.
- Actions: Actions are sliding parts of the mold that move into place during the filling and packing part of the cycle. Once the part cools and is ready to be ejected, the action pieces retract as the mold is separated. Undercut features are created such as recesses and barbs, while the ability to eject the part is maintained
- Lifters: A lifter is a mold component that travels with the ejection stroke and moves on an angle to slide/pull the cavity steel away from the undercut feature or detail not in the die draw.
- Hand loads: Hand loads, or hand-loaded inserts, are a method of achieving a part feature without designing it into the mold, but rather by hand-loading a piece into the mold cavity as it is being filled. The hand-loaded piece (or pieces) are later ejected along with the finished part and reinserted in the next cycle.
- Unscrewing Cores: This action is coordinated with the injection molding press cycle, so it occurs when the mold is opening, which results in cycle time reductions. Used for parts requiring molded threads either internally or externally.
For more information, contact us today.
Resources:
https://www.xcentricmold.com/2018/06/20/undercuts-in-plastic-injection-molding/
https://www.protolabs.com/resources/design-tips/6-ways-to-achieve-undercut-success-in-molded-parts/
https://www.injectionmould.org/2019/04/19/undercuts/
Topics:
Related Articles
-
Mar 19, 2025
Top 6 Advantages of Injection Molding for Your Project
Injection molding — the process of injecting molten resin into a mold — is one of the most...
-
Feb 19, 2025
Injection Molding vs CNC Machining: Which Method to Choose?
Every year, humans produce and use countless plastic products in various shapes, sizes, and...
-
Oct 03, 2024
Injection Molding Uses: Exploring Applications Across Industries
Injection molding is one of the most versatile manufacturing processes, with a wide range of...