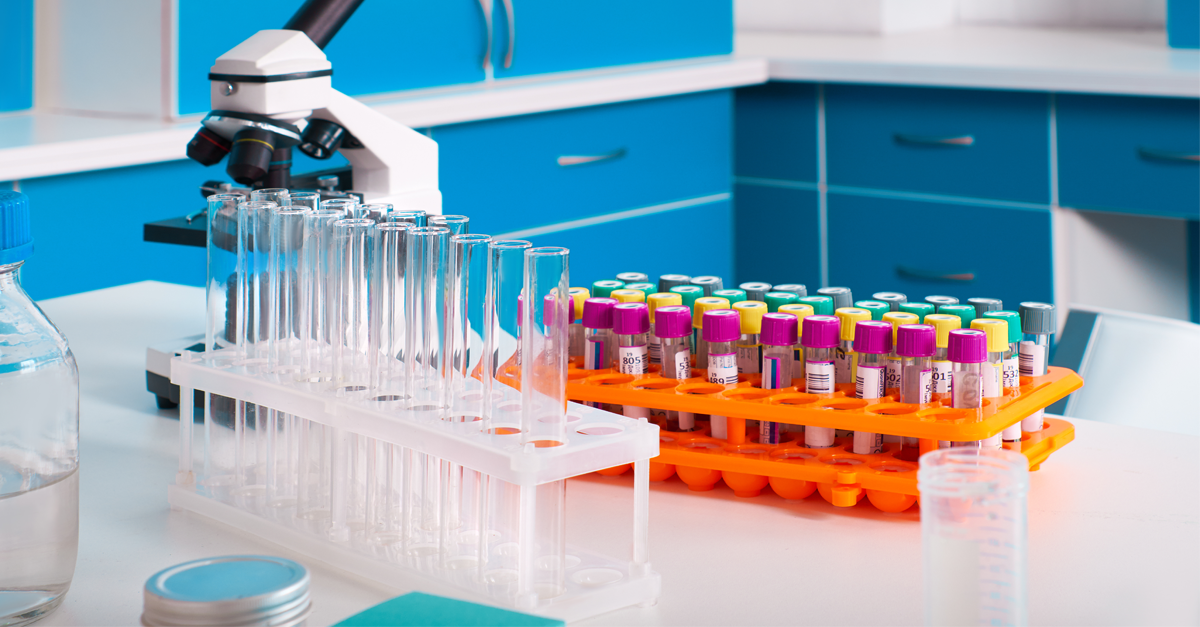
Top 6 Advantages of Injection Molding for Your Project
Injection molding — the process of injecting molten resin into a mold — is one of the most effective manufacturing techniques to meet the needs of many applications and industries. It helps (mass) produce high-quality and high-strength products that are durable for many uses.
These benefits make injection molding one of the best decisions your company can make for your devices or components, and in the process, you can improve processes, ensure quality, and save on costs. It’s important, however, to consider the advantages and disadvantages of injection molding to determine whether injection molding is the perfect fit for your particular project.
This guide will explain the top six advantages of injection molding and where to turn for expert injection molding services.
Top 6 Advantages of Injection Molding
Other types of product manufacturing can be expensive, especially when you need large quantities or repeatable processes. Injection molding allows you to increase volume, obtain quality parts, and improve the bottom line.
Consider these six key advantages of plastic injection molding and what they can mean for your business:
1. Efficient Production
What does the injection molding process look like? First, the injection molder inserts molten resin into a preset mold to fill the cavities. This is done under high pressure for speed and accuracy, and then each piece is cooled so it hardens and is ejected.
The plastic injection molding machine is streamlined and efficient, so production happens quickly — even as fast as every 10 seconds. This means faster cycle time, quick high-volume order fulfillment, and ease of use. These benefits apply even if you need a lower volume produced.
One example of the efficiency impacts is how Crescent Industries helped out a customer who was looking to reduce labor costs and guarantee quality parts. They needed 19 diagnostic plates that had different internal geometries, and the Crescent team automated parts of the production process and relied on four molds that had four cavities with varying internal geometry. The customer saw a 54% reduction in labor and 100% in-line inspections.
2. Wide Material Selection
With injection molding, there is a wide range of plastic materials options, making the process even more versatile and customizable. You can choose from options like engineered and commodity-grade resins and combinations of filler materials. This flexibility allows your needs to be met with the best material to create the highest-quality product possible.
3. Design Complexity
Design fulfillment can be one of the biggest challenges in manufacturing, especially when intricate designs are required. With injection molding, the material is injected under very high pressure, ensuring better mold wall contact. This guarantees that each and every detail of the design guidelines is captured effectively.
Crescent Industries brings more than a century of experience in injection molding and mold building, ensuring you get the outcome you desire. We take steps like ensuring uniform wall thickness and applying draft angles for easy removal for an injection mold tool that produces a product reliably and repeatably.
4. Cost-Effectiveness
The right injection molding solutions provide greater efficiency, leading to cost and time savings that impact the entire organization. When processes run smoothly, and fewer errors occur, no time is wasted dealing with problems or handling time-consuming manual tasks.
Consider one case from Crescent, in which we helped a global original equipment manufacturer (OEM) double its production capacity while cutting costs by 18%. The customer needed customization, automation, and high throughput for the success of a new product, and they were able to accomplish this with a stronger bottom line.
5. High Precision and Consistency
Injection molding is made even more efficient when you work with a good injection molder who has experience in developing a robust, repeatable process. The format is highly precise, ensuring each detail of the design is properly captured and clearly defined.
With Crescent Industries’ focus on quality, we ensure accuracy, close attention to detail, and repeatability. Devices like our 3D scanner and video measuring and inspection equipment ensure precision with every job.
6. Reduced Waste
Gone are the days of excess waste that often comes with a more traditional manufacturing process. With injection molding, only the exact amount of material needed is used to fill each mold, minimizing waste significantly. Any waste that does occur can be recycled to minimize environmental impact.
When designs are more precise and end products are accurate and high-quality each time, there is less waste. Crescent Industries delivers these benefits and more.
Industries Benefiting From Injection Molding Services
Most industries can benefit from injection molding, so it can be found everywhere. Here are industries that rely on the technology the most and key product examples within each of them:
- Medical: Lab equipment, imaging components, medical devices, surgical instruments
- Pharmaceutical: Packaging, tubs, nests, IV ports
- Military and defense: Handheld communication devices, decoys, battery packs, weaponry, guidance systems
- Dental: Surgery components, office equipment
- Aerospace: Connectors, battery enclosures, bezels
- Industrial: Machinery components, mechanical parts
- Electronics and electrical components: Device shells, electronic housings, plug components
Injection molding is used to produce a wide range of plastic products in these industries that ensure cost-effectiveness, safety, and quality. Reliance on this technology will only continue to increase as more uses are discovered and sustained in different processes.
Take Advantage of Expert Injection Molding Services Today
Injection molding is one of the most successful technologies contributing to tech advancements in product manufacturing. Alongside automation techniques, companies across industries are discovering the advantages of the injection molding process to see exceptional results.
When you’re ready to explore options, turn to Crescent Industries' team of experts. With over a century of experience in custom molding, we can work with you on whatever your product and material selection needs may be.
We primarily serve the medical, military, and industrial/OEM industries and will help bring your product to life. Our customers have seen our team's expertise at work to produce higher-quality products.
Get started today by contacting Crescent Industries to talk about your injection molding needs.
Topics:
Related Articles
-
Mar 19, 2025
Top 6 Advantages of Injection Molding for Your Project
Injection molding — the process of injecting molten resin into a mold — is one of the most...
-
Feb 19, 2025
Injection Molding vs CNC Machining: Which Method to Choose?
Every year, humans produce and use countless plastic products in various shapes, sizes, and...
-
Oct 03, 2024
Injection Molding Uses: Exploring Applications Across Industries
Injection molding is one of the most versatile manufacturing processes, with a wide range of...