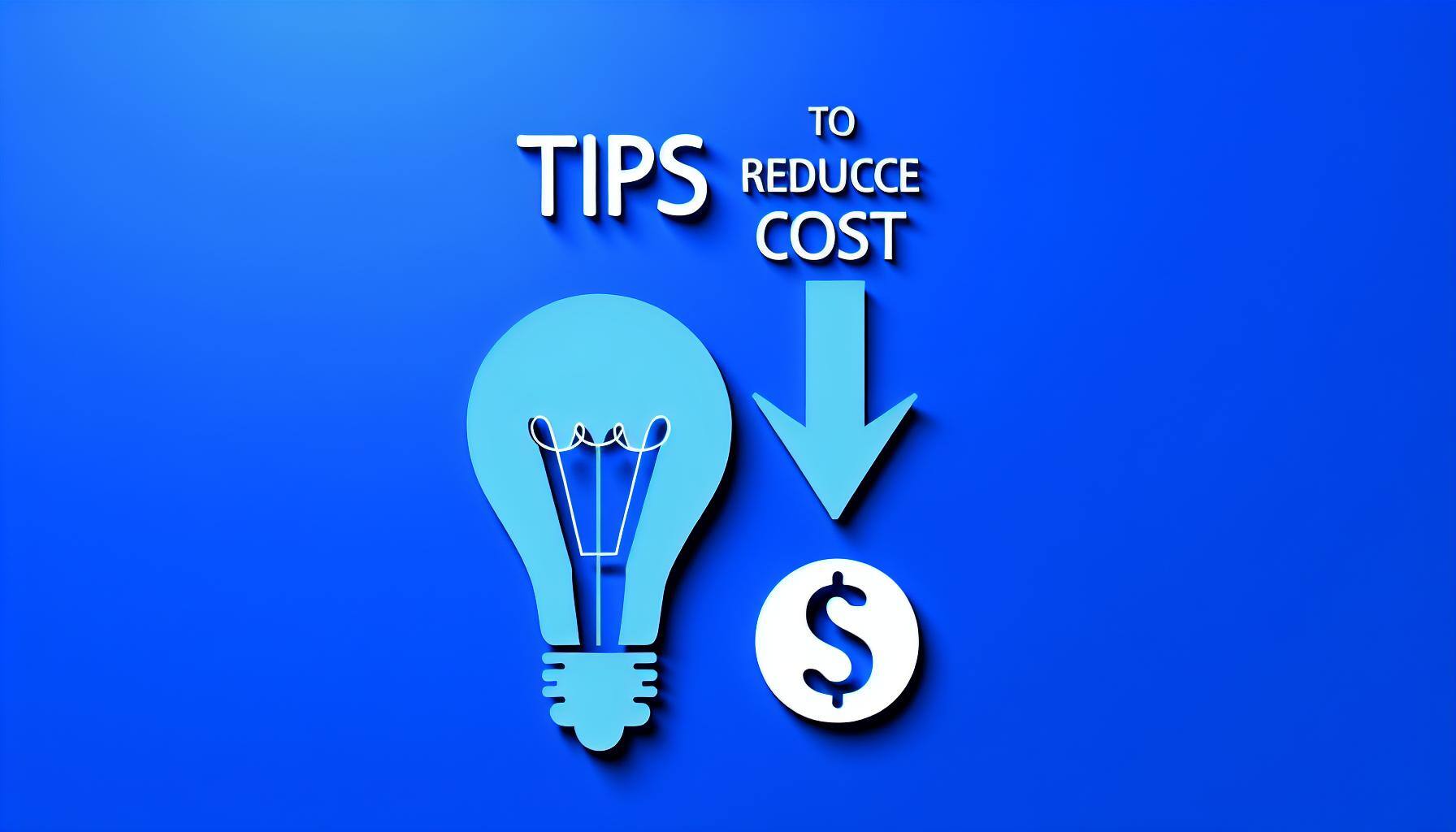
Tips to Reduce Plastic Injection Molding Costs
While plastic injection molding is one of the most cost-effective manufacturing processes available, it is all too easy for unexpected and unnecessary cost additions to drive up the overall price of a project. If this is a situation you have encountered, or if you simply wish to know ways to reduce injection molding costs, the below tips may help.
Knowledge and foresight are the two biggest factors that define the actionable steps below. Once you know how to properly plan an injection molding project, you are in a position to keep the cost under control.
How to Cut Costs of Injection Molding Projects
Is injection molding expensive? In comparison to other processes, the answer is almost always no. By following the below steps, you can better ensure your injection molding budget remains as reasonable as possible.
- Plan thoroughly and complete tasks in bulk. Planning is the most important step to take in managing costs. By mapping your entire project — including budget, timeline, and desired results — you provide direction and guidelines for every step of the process. Whenever possible, set benchmarks and deadlines to keep quality, costs, and timing on track. Also, be sure to take a holistic view of all processes and components needed so that you can group like processes into bulk orders and gain cost benefits.
- Design to minimize material usage. Completely solid plastic injection molded pieces are often unnecessary. Using design best practices such as ribs and gussets, you can strengthen molded pieces while vastly reducing the amount of material used throughout a production run.
- Follow best practices to increase production efficiency. Injection molding is a versatile process, but also one with numerous design and manufacturability best practices that should be followed. By adhering to pointers such as using curved corners instead of right angles, using minimum wall thicknesses, and assuring proper material flow throughout the mold, you could reduce the number of rejected parts and gain more efficiency in the production process.
Register for Injection Molded Part Design Guidelines. - Combine processes. If your project requires components made of other materials, such as machined inserts, use a provider with over molding capabilities to eliminate an assembly step, speed production, and improve the quality of the finished product.
- Reduce finishing and secondary operations. Operations such as drilling holes or assembling parts add costs and time to the project. Whenever possible, design aspects such as drilled holes into your molded part, so that these processes do not need to be completed separately.
- Choose the right material. There are thousands of injection molding plastics available, each offering different material qualities and costs. Avoid overengineering your product — instead, choose a material that offers the minimum material properties that you need while still meeting performance and quality requirements. Using an unnecessarily expensive material will increase your costs without returning value.
As plastic injection molding specialists, Crescent Industries is ready to offer our expertise in completing your project on time, on budget, and with exceptional quality and service.
To learn how we can help, contact us today.
Topics:
Related Articles
-
Mar 19, 2025
Top 6 Advantages of Injection Molding for Your Project
Injection molding — the process of injecting molten resin into a mold — is one of the most...
-
Feb 19, 2025
Injection Molding vs CNC Machining: Which Method to Choose?
Every year, humans produce and use countless plastic products in various shapes, sizes, and...
-
Oct 03, 2024
Injection Molding Uses: Exploring Applications Across Industries
Injection molding is one of the most versatile manufacturing processes, with a wide range of...