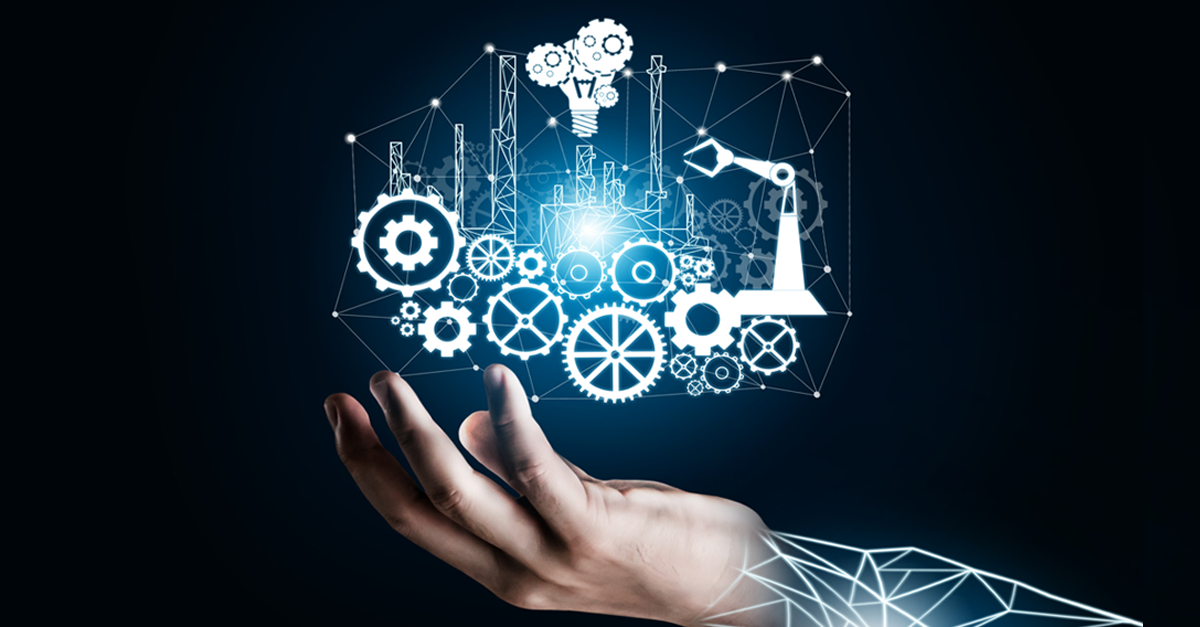
The Role of Design for Manufacturability (DFM) in Product Cost Optimization
Cost optimization is one of the most important considerations when manufacturing your product design for plastic injection molding. But with so many variables, knowing where to focus your efforts can take time and effort.
Your team could have the most efficient part design or device. However, without an effective manufacturing process, your product will take longer to manufacture, cost more than expected, and be of lower quality. That’s why understanding the concept of design for manufacturability (DFM) is essential: it helps you optimize the design of your product and reduce costs.
Read on to learn more, including answers to questions such as "What is design for manufacturability?" "What are the components of design for manufacturability?" "How can design for manufacturability lead to cost optimization?"
What Is Design for Manufacturability (DFM)?
Design for manufacturability (DFM) is an approach to product design that emphasizes optimizing the manufacturing process, with consideration given to all aspects of a product’s design. DFM is a design process based on the idea that you can optimize the manufacturing process and create high-quality products by incorporating design considerations during the product design phase. In plastic injection molding, DFM involves evaluating the part design for mass production, designing and building the tooling to achieve that goal efficiently, and maintaining product quality and integrity.
DFM has various components that you should consider during the product design phase. These include:
- Understanding your manufacturing process: Before designing your product, you must understand the methods and techniques used to produce your component or device. This will help you choose materials, parts, and design features compatible with your processes and equipment.
- Designing for efficiency: When making design decisions, you should consider optimizing the design for efficiency. This includes reducing the number of parts, simplifying tooling, and choosing the most straightforward assembly process for your product if needed.
- Choosing your materials wisely: The materials you choose will significantly impact the total cost of your product. It’s essential to research and select materials that are easy to manufacture, cost-effective, and of high quality.
- Designing for the intended environment: It’s important to consider the environmental conditions your product will need to be able to withstand and design accordingly. This includes considering factors such as temperature, moisture, and chemical exposure.
6 Reasons Why DFM Is Essential To Product Cost Optimization
While there are many advantages to design for manufacturability, cost optimization is one of the main reasons it’s so important. Here are seven ways that DFM can help you reduce costs and optimize the design of your product:
1. Optimizing Tool Design and Molding Process
The tools and processes you choose can significantly affect the cost and quality of your product. DFM helps you optimize the design of your tooling and molding process by ensuring that the components’ design adheres to the best injection molding practices. The mold design is made to fulfill the project requirements and provide quality products for the project’s entire lifecycle.
2. Streamlining All Manufacturing Processes To Minimize Room for Error
Manufacturing processes are complex, and mistakes can be costly. DFM helps you streamline the entire manufacturing process and reduce room for error. By designing components that are easy to manufacture and assemble, you can minimize the time it takes to produce your product and maximize its likelihood of being the highest quality.
3. Ensuring Consistent Material Selection To Enhance Production Efficiency
Materials selection is one of the most important decisions you’ll make when designing a product, as it will have a major impact on both the cost and quality of your product. DFM can verify whether the material is suitable for a component or device, which can help enhance production efficiency and reduce overall costs.
4. Simplifying THE Assembly Process by Optimizing Part Design
Using DFM can help you optimize the design of your parts so that they are easy to assemble. This includes reducing the number of parts and designing parts to have the fewest possible contact points. This reduces the time and cost of assembly and minimizes potential problems during manufacturing, such as misalignment or incorrect assembly.
5. Avoiding Costly Issues With Preemptive Mold Design Analysis
Mold fill simulation is an integral part of DFM that helps identify potential problems in the mold's design phase before the tool's fabrication or production runs. This can save time and money by detecting design errors that may lead to costly rework or even scrapping the entire mold. Mold fill simulation also allows you to optimize the design of the mold to ensure that the product is produced with the highest quality and efficiency.
6. Optimizes Tight Tolerances for Processes and Materials
The tolerances of processes and materials can have a major impact on the cost and quality of a product. For instance, materials with too thick walls can slow the cooling process and increase production time. DFM helps you to see how different tolerances can affect production time and cost and then optimize tolerances to ensure optimal product quality.
Discover the Benefits of Plastic Injection Molding for Your Products
Plastic injection molding is a cost-effective and efficient way to create high-quality products. With the help of design for manufacturability, your product's mold design and manufacturing will be efficient, reduce costs, and create a superior-quality product. At Crescent Industries, we understand the importance of design for manufacturability in product cost optimization. We offer advanced injection molding services optimized for efficiency, quality control, and cost. Our experienced team is available to assist with all your injection molding needs and can help you create a product that meets the highest standards.
Contact us today to learn more about our plastic injection molding capabilities.
Resources
https://quality-manufacturing.org/china-design-for-manufacturing/
https://www.plasticcomponents.com/design-for-manufacturing-in-plastic-injection-molding-guide
https://www.thermalpress.com/basics-of-design-for-manufacturability/
https://www.pcbnet.com/blog/a-guide-to-design-for-manufacturing-dfm-principles/
Topics:
Related Articles
-
Jul 24, 2024
The Evolving Landscape of Custom Injection Molding
A big part of establishing your foothold in any industry is adopting—or at the very least, staying...
-
Nov 21, 2023
3D Printing vs Injection Molding: Pros and Cons
Many manufacturers compare 3D printing vs. injection molding to determine the best method for...
-
Nov 02, 2023
A Guide To The Overmolding Process
Along with its ability to create high-quality soft-touch grips, the over-molding process benefits...