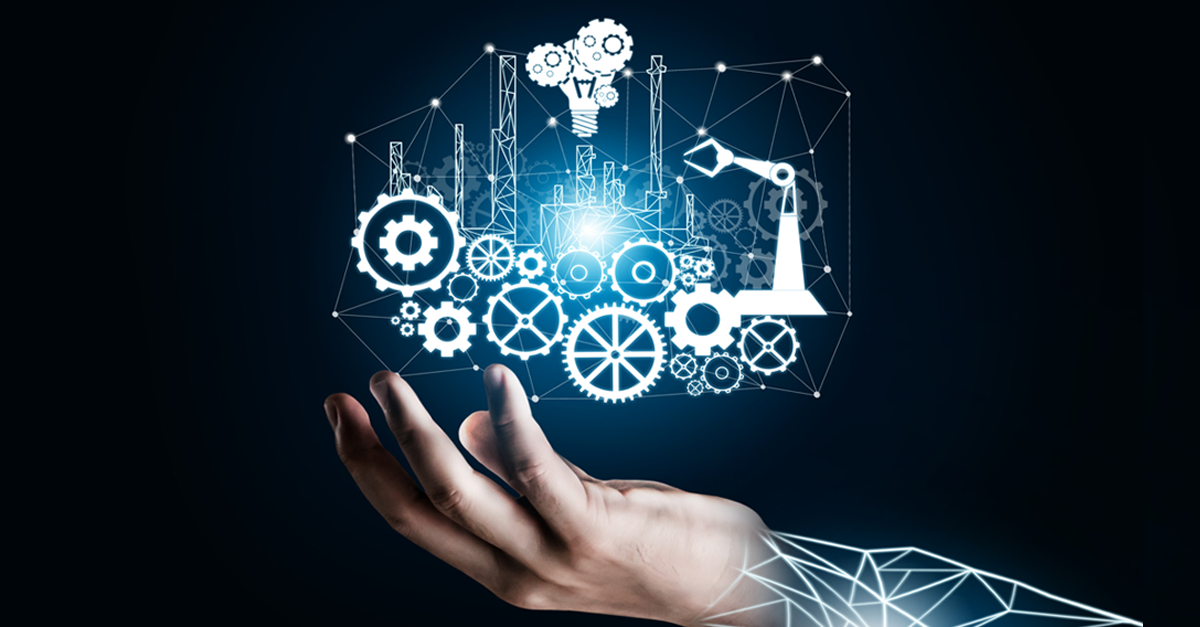
The DFM Process: What to Expect From an Injection Molding Manufacturer
Design for manufacturability (also called design for manufacturing or DFM) enables original equipment manufacturers and contract manufacturers to identify current and potential problems and fix them in the design phase, which is the least expensive time to address them. Any qualified plastic injection molding contract manufacturer should carry out a thorough and state-of-the-art DFM process to ensure your project's success. As an OEM, you play an essential role in that process.
When your plastic injection molding CM is leading DFM for your project, you should expect them to:
Analyze Plans and Identify Concerns
You will need to provide the CM with plans and documentation for the part, along with information about the product and relevant project details:
- If the part has been previously manufactured, provide a sample of the part itself.
- Provide all plans, information, and documentation related to the part.
- Describe any concerns you may have about the manufacturability of the component or problems you might anticipate in its manufacturing.
- Provide information about how the part interfaces with other components or assemblies and downstream end-use.
During this step, CM engineers consider these concerns and review plans and documentation to identify potential issues affecting manufacturability.
Conduct a DFM Simulation
The CM engineers use specialized mold filling simulation software to simulate the injection molding processes. They use the software to create a real 3D simulation of flow, heat flux, and warpage for injection molding, including the complete mold with all details. During the simulation, they inspect the project for all of the parameters in the checklist for DFM in plastic injection molding, identifying any problems that will occur unless changes are made to the design, mold, materials, etc.
Present the Simulation Results and Recommendations
Upon conclusion of the simulation, the CM engineers will prepare and share the simulation results with you and recommend the best solutions to the problems identified. A key deliverable to you from the CM is a document communicating the DFM process results and the resulting recommendations, including screenshots from the simulation process. The document should include:
- Conditions used for the simulation:
- Press setup information, including:
- Material
- Shot Size
- Material Temperature
- Mold Temperature
- Fill Time
- Pack Time
- Total Mold Closed Time
- Gate Size
- Nozzle Size
- Gate Freeze
- Pack Pressure
- A material data sheet with specifications sourced from the material supplier, e.g., ExxonMobil. (DFM should include guidance from the CM on resin raw material and other raw materials selection to meet the project's plastic component requirements.)
- Press setup information, including:
- A section covering each parameter that was tested in the simulation, presenting simulation results
- Multiple sections comparing the results of different variables introduced in the simulation and the results achieved, for example, a comparison of various packing pressures and the resulting sink marks, hot spots, and voids.
- A summary of concerns that arose from the simulation
- A summary of the contract manufacturer's recommendations and remedies that adhere to injection molding best practices and optimized manufacturing
Prototype, Test, and Complete the Project
Often, the DFM process continues with 3D printing (additive manufacturing) to carry out prototyping and the creation of parts for you to test in the overall manufacturing process for your product. As needed, portions of the DFM simulation described above can be repeated, along with prototyping and testing, until the product is ready for manufacture.
By seeking out and engaging with a contract manufacturer skilled at DFM, you can produce plastic injection molded parts with confidence, knowing that the process will run smoothly.
Topics:
Related Articles
-
May 20, 2025
Designing for Injection Molding Success: What Every Engineer Should Know
Designing plastic parts for injection molding is both a science and an art. From material selection...
-
Jul 24, 2024
The Evolving Landscape of Custom Injection Molding
A big part of establishing your foothold in any industry is adopting—or at the very least, staying...
-
Nov 21, 2023
3D Printing vs Injection Molding: Pros and Cons
Many manufacturers compare 3D printing vs. injection molding to determine the best method for...