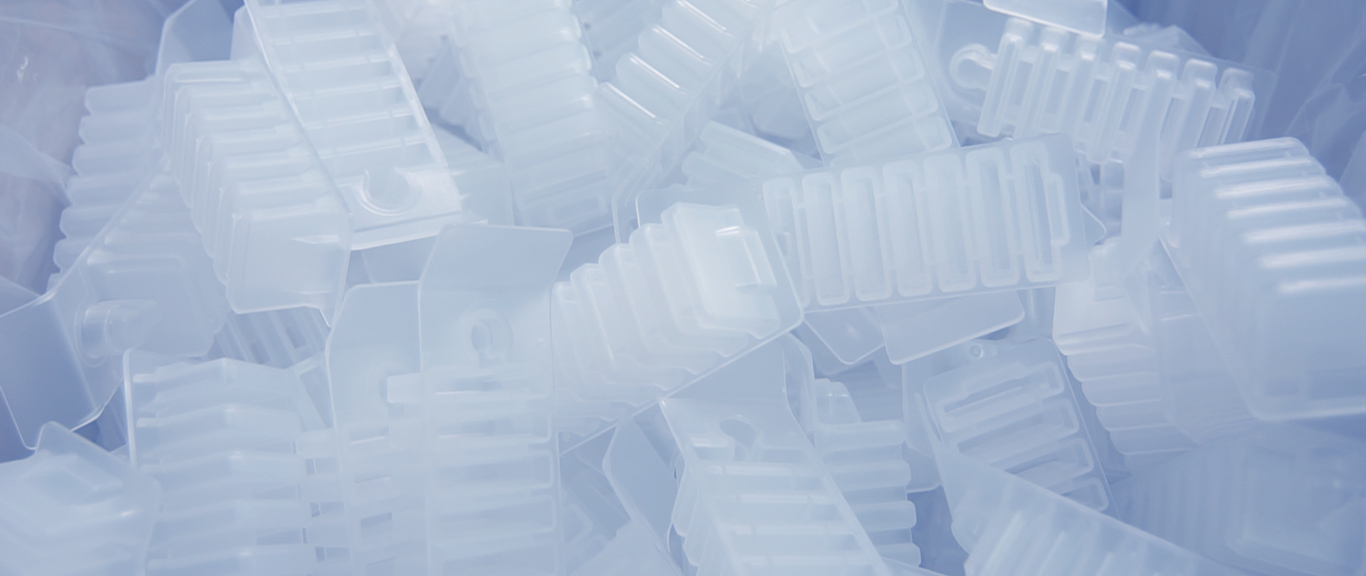
The Benefits of Custom Plastic Parts
The global plastic market value was over $638 billion in 2023. As more manufacturing companies turn to plastic parts, this figure may grow at an annual rate of 4.3% by 2030.
Plastic has higher versatility, durability, and cost-effectiveness than traditional materials like metal, glass, wood, and rubber. Injection molding remains one of the most efficient and flexible methods for producing plastic products, including custom plastic parts. Here's an overview of the key applications for custom made plastic parts and the benefits of injection molding in modern manufacturing.
Importance of Custom Plastic Parts in Manufacturing
Custom plastic part fabrication is essential across many sectors. Several manufacturers, including Crescent Industries, use advanced technology to produce precise plastic components in various shapes, sizes, and materials for medical, military, and industrial industries.
Medical Sector
Plastic injection molding has revolutionized medical device manufacturing by offering an advanced process to create precise, high-quality, and sanitary custom plastic parts, including:
- Medical Device Enclosures: These components require accurate dimensions and must adhere to strict regulatory standards. Engineers can manufacture these plastic parts consistently and reliably with injection molding.
- Dental and Surgical Instruments: Engineers can use plastic injection molding to manufacture instruments with designs that enhance comfort and usability for healthcare professionals and patients.
- Laboratory Consumables and Diagnostic Equipment: Injection molding enables rapid, secure, and cost-effective creation of disposable diagnostic items, including test kits, reagent containers, microplates, pipette tips, and specimen containers.
- Prosthetics and Implants: Plastic mold manufacturing helps create patient-specific solutions like dental implants and joint replacements while ensuring comfort, safety, and functionality.
Military Sector
The military sector also relies on injection molding for custom plastic parts. Military devices must withstand heavy use, extreme conditions, high impact, and severe temperature changes. Custom plastic parts offer a durable and lightweight substitute for heavier materials, providing performance without added weight.
Military products created using custom plastic components include weaponry, munitions, battery packs, handheld comms, guidance systems, and bi- and mono-ocular housings. After manufacturing, these plastic parts are typically subjected to rigorous quality testing for impact resistance and environmental durability to ensure they meet military standards.
Industrial Sector
Original Equipment Manufacturers (OEMs) across various sectors also benefit significantly from custom-molded plastic parts:
- Electronics: Custom-made plastic parts tend to be precise and cost-effective, so they are helpful in the production of smartphones, computers, and home appliances, as well as in the manufacture of the housings, connectors, and other internal plastic parts of these appliances.
- Agricultural and Industrial Machinery: Injection molding is typically used to create machinery parts, irrigation fittings, and tool handles. Some of the custom plastic parts in machinery components include gears, housings, and casings, offering resistance to wear and chemicals.
- Packaging: By selecting raw plastic materials that meet these standards, you can create custom plastic packaging and food-safe products like caps, closures, and containers.
Top Benefits of Custom Plastic Parts
Custom plastic part molding offers numerous advantages, making it an invaluable resource in modern manufacturing.
Versatility in Design and Functionality
One of the main benefits of custom plastic part fabrication is design flexibility. Plastic part manufacturers can design and create plastic parts that meet your exact specifications, allowing you to get all the complex shapes you need and include specialized functions that would be impossible to achieve through other methods.
This versatility ensures that the plastic components not only meet the specific needs of your industry but also optimize your final product's efficiency and performance. With custom-made plastic parts, you have the flexibility to integrate components easily into your larger assemblies.
Rapid Prototyping and Production Speed
Production speed is vital for every new or improved product about to be introduced to the market. However, a custom plastic part goes through numerous design stages while it evolves from an idea to reality.
Plastic injection molding can help you quickly develop various prototype designs and test each product component's form, fit, and function. This way, you can eventually streamline production and ensure on-time delivery.
High-Quality, Durable Materials
Custom plastic molding manufacturers typically use high-quality, durable plastic resins that offer excellent resistance to heat, chemicals, and wear and extend product life exponentially. Enhanced durability often reduces the need for constant maintenance and regular replacement, eventually lowering overall operational costs.
Scalability for Large and Small Orders
Scalability is one of the main factors affecting the manufacture of different product volumes. Custom plastic injection molding can efficiently accommodate any product volume — large or small. This flexibility can help you scale your operations up or down and fulfill different order sizes depending on your needs.
Why Choose Crescent Industries for Custom Plastic Parts?
Custom plastic parts offer clear advantages across multiple sectors. The design versatility, rapid prototyping, durability, and scalability involved in their manufacture make custom plastic pieces suitable for the medical, military, and OEM industries. In all three sectors, rigorous testing and quality assurance are critical to ensure optimal reliability and standards.
Because creating custom plastic parts requires precision and expertise, the engineers at Crescent Industries produce high-quality custom plastic components tailored to the specific needs of your industry. For example, as a certified International Traffic in Arms Regulations manufacturer, we ensure all our products meet the highest security and quality standards for military device production.
With 75+ years of experience and an extensive network, Crescent Industries can meet your unique manufacturing needs. Contact us today to discuss your next project.
Topics:
Related Articles
-
Mar 19, 2025
Top 6 Advantages of Injection Molding for Your Project
Injection molding — the process of injecting molten resin into a mold — is one of the most...
-
Feb 19, 2025
Injection Molding vs CNC Machining: Which Method to Choose?
Every year, humans produce and use countless plastic products in various shapes, sizes, and...
-
Oct 03, 2024
Injection Molding Uses: Exploring Applications Across Industries
Injection molding is one of the most versatile manufacturing processes, with a wide range of...