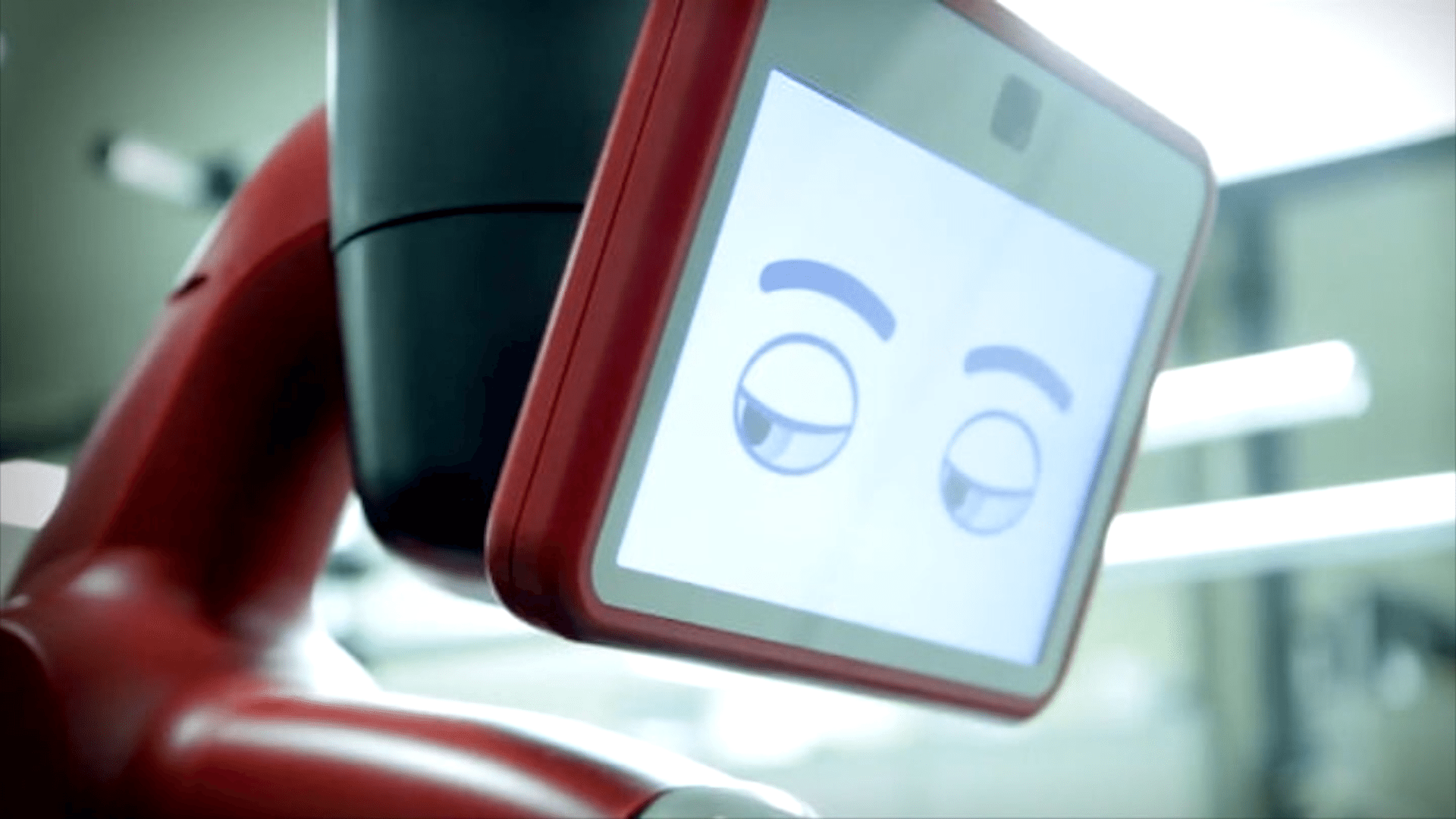
The Basics of Injection Molding
Currently Injection molding represents approximately 60% of all plastic parts presently made, so let’s take a basic approach to how injection molding differs from other plastic processing types.
For companies seeking cost-effective, complex, and customized components, plastic injection molding is an ideal solution. To better understand the basics of injection molding it will first be useful to understand how this process compares to other plastic molding techniques. Below are some of the most common methods used to manufacture plastic parts.
Compression Molding: Plastic is compressed between two heated mold cavities to force the material to fill the desired mold shape.
Blow Molding: Heated plastic is blown into a mold along with air and as the plastic expands, it presses against the walls of the mold forming a thin-walled, hollow shape.
Rotational molding: Plastic is inserted into the mold at the desired temperature while the mold continuously rotates to form hollow parts with uniform wall thickness.
Thermoforming: Sheets of plastic are heated and a vacuum is drawn to pull the plastic into the mold cavity to form the desired shape.
Extrusion: Dry plastic material is fed into a heating chamber where the heated plastic is pushed out of a die to form the shape of the desired finished product.
Injection Molding: Melted plastic is injected into a mold cavity to form the shape of the mold.
Plastic Injection Molding Process and Equipment
Now that we better understand how injection molding differs from other molding methods, let’s discuss the injection molding process and equipment in more detail. Examples of typical injection molding equipment are below. The molds are typically made of steel or aluminum and are precision-machined to form the desired features and intricacies of the final product. In this process, solid plastic, often granules, is stored in a hopper and fed into a heated barrel. As shown, a screw is used to mix, heat, and transport the plastic toward the mold. The melted material is then injected through a nozzle into the mold and travels via a gate and runner system into the mold cavity; the proper design of the gate and runner system is essential to ensuring the mold is filled properly. As the plastic enters the mold, excess air can be released via vents. The pressure and temperature of the mold are maintained to allow the plastic to conform to the desired shape and harden quickly. Once the part is adequately cooled, the mold opens and the part is ejected, often with the help of ejector pins. The mold is then ready to receive the next charge of melted plastic. The injection molding process is a continuous operation with minimal downtime, resulting in high output rates.
(photo credit: Wikipedia)
Advantages of Plastic Injection Molding
Plastic injection molding has several benefits compared to other molding processes, and below are some of its key advantages.
Excellent versatility: Injection molding is a good choice for a wide range of part sizes, materials, and colors. This process is used to create everything from large automotive parts to small, intricate components for the medical field. Most polymers, including thermoplastics and elastomers, are suitable for use in injection molding, adding to their versatility since there are thousands of materials designers can choose from to meet the desired component properties such as strength and elasticity! Additionally, injection molding allows for the use of multiple materials simultaneously, allowing for a high degree of customization.
Very reproducible: Injection molding produces products that are virtually identical from part to part which provides excellent brand consistency and part reliability during high-volume runs. High reproducibility also allows for production to be scaled up to very large volumes, resulting in low costs per unit after the upfront equipment set-up costs are paid.
Able to Produce Complex Parts: Plastic injection molding is typically performed at very high pressure which forces the plastic into small crevices in the mold (that other molding processes are unable to reach), enabling the production of intricate and complex parts.
Efficient Production: Injection molding is a very fast process that generates high-output production compared to other molding methods, making injection molding a more efficient and cost-effective solution.
Automation Reduces Cost: Plastic injection molding is highly automated via the use of machines and robotics, requiring less oversight by operations personnel. Automation increases consistency and efficiencies which decreases the manufacturing cost per unit.
Low Waste Generation: Injection molding manufactures smooth products that have minimal finishing requirements after removal from the mold – resulting in less waste generation compared to other molding techniques. Oftentimes, injection molding waste can be reused, resulting in a more environmentally friendly and lower cost process.
Crescent Industries’ Injection Molding Capabilities
Crescent Industries is a custom injection molder providing an integrated single-source solution for our customers. Utilizing our Scientific Injection Molding Principles and state-of-the-art Injection Molding Machines, our focus is to provide our customers with a robust process to produce the highest level of quality for their components. Crescent’s plastic injection molding services are categorized as follows:
Medical and Pharma Injection Molding: For close to 50 years, Crescent has been consistently producing superior supply chain solutions for the medical, pharmaceutical, and dental industries. When required, Crescent can manufacture in our certified ISO 8 (100K) clean room. To provide our customers with a single source solution, we also offer an ISO Class 7 (10K) clean room for assembly and packaging services to complete your project.
Military and Defense Molding: Crescent is recognized by the U.S. Department of the State as an ITAR-Registered Manufacturer. We understand that durability, reliability, and repeatability are paramount in defense applications and we have decades of experience in injection molding and mold-building for this industry.
Custom Injection Molding: Crescent has been a trusted partner for OEMs across multiple industries for 70+ years. We create custom molding solutions for our customers’ unique requirements in industries as diverse as medical, defense, electronics, and industrial/OEM.
Crescent Industries has an extremely knowledgeable team to assist with all of your design questions – contact us to learn more about how we can assist with your injection molding project!
Crescent combines custom injection molding excellence with a full suite of services, delivering additional value and streamlining your supply chain.
Topics:
Related Articles
-
Mar 19, 2025
Top 6 Advantages of Injection Molding for Your Project
Injection molding — the process of injecting molten resin into a mold — is one of the most...
-
Feb 19, 2025
Injection Molding vs CNC Machining: Which Method to Choose?
Every year, humans produce and use countless plastic products in various shapes, sizes, and...
-
Oct 03, 2024
Injection Molding Uses: Exploring Applications Across Industries
Injection molding is one of the most versatile manufacturing processes, with a wide range of...