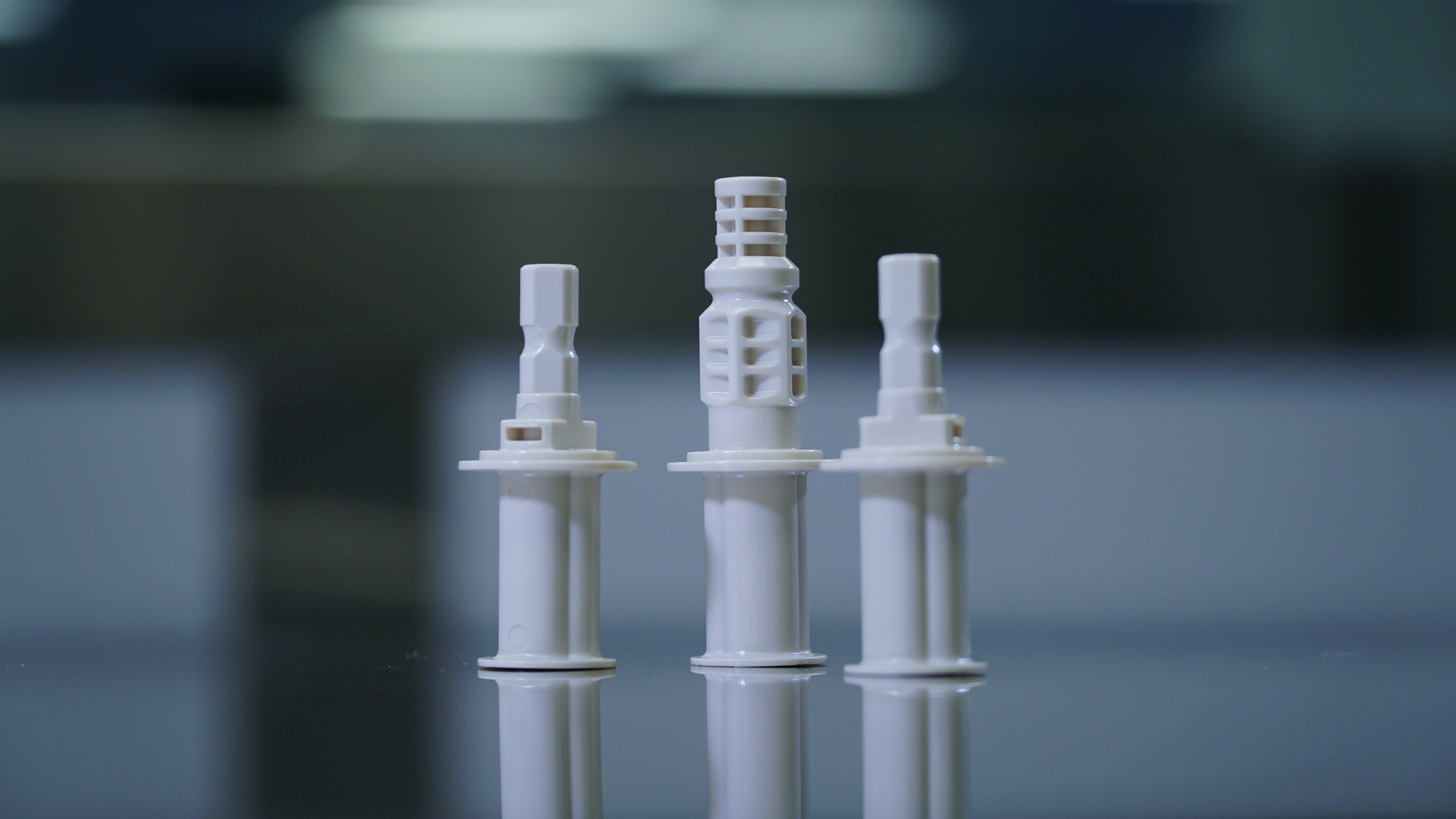
Quality Process and Controls for Medical Device Contract Manufacturing
Medical device contract manufacturing is a heavily regulated industry that must adhere to strict standards. Medical device suppliers should ensure that their injection molding partners possess certain qualifications, for medical device manufacturing.
From basic components, like tubing and syringes, to advanced machines like ventilators and pumps, the equipment used in the medical industry saves lives everyday. That's why medical device contract manufacturing requires stringent quality metrics of third-party suppliers and the capabilities to fabricate the required components to their exact specifications.
If medical device manufacturers are looking to partner with another supplier to build their components, they should make sure all their suppliers have the necessary certifications for building such vital equipment. The International Organization for Standardization (ISO) and the Food and Drug Administration (FDA) are the two main regulatory bodies whose standards manufacturers must follow, so we'll explain them both — and give another important fabrication capability.
Quality Guidance and Best Practices: ISO 13485
A globally recognized authority on ensuring the quality and safety of our everyday lives, the ISO developed standard 13485 to guide manufacturers in producing the highest-quality medical devices possible. The specific purpose of ISO 13485 is to:
"...be used by organizations involved in the design, production, installation and servicing of medical devices and related services. It can also be used by internal and external parties, such as certification bodies, to help them with their auditing processes."
The complete breadth of the ISO 13485:2016 requirements is vast, but this standard gives comprehensive guidance to both manufacturers and partners regarding best practices on many issues, like:
- Quality Management Systems (QMS)
- Resource Management
- Management Responsibility
- Product Realization
- Measurement, Analysis, and Improvement
When checking for ISO 13485 certification, it is important to note that the requirements for this standard were updated from ISO 13485:2003 to ISO 13485:2016. All medical device contract manufacturing partners should be ISO 13485:2016 certified to keep up with current requirements. At Crescent Industries, we are proudly certified as an ISO 13845:2016 contract manufacturer, proving our ability to offer plastic injection molding services at the quality demanded within the medical device industry.
FDA Registration for Medical Device Manufacturers
The ISO is a non-governmental regulatory body, but national standards also exist that companies must follow if they are to build medical device components. The FDA is responsible for enforcing these regulations, and has created standard 21 CFR Part 820 to guide contract manufacturers in proper medical device fabrication. This standard outlines the federal requirements for medical device manufacturing, like:
- Design Controls
- Document Controls
- Purchasing Controls
- Identification and Traceability
- Production and Process Controls
- Labeling and Packaging Controls
The FDA not only outlines quality metrics for production, but they also require that all medical device contract manufacturers annually register to be eligible to manufacture their parts. This standard falls under 21 CFR 807 and also requires manufacturers to list which components are made at their facility and what operations are performed. This ensures maximum component quality, and it's why Crescent Industries is FDA-registered as a medical device contract manufacturer.
Quality Management for Injection Molded Medical Devices
Lack of quality management systems and controls for your medical device contract manufacturer end up far more costly due to rework or scrap material, shut down lines, freight costs, recalls and potentially even incur penalties.
Suppliers for injection molding components are now held responsible for making certain that all their processes are validated. They have to have high-quality systems in place for things like:
- Product risk management
- CAPA’s
- Design change control
- Root cause analysis
- Complaint handling
- Non-conformance
Partnering with experienced plastic injection molding manufacturer makes it possible to anticipate and plan for medical device production processes that meet all necessary regulatory, quality, and commercial standards.
Injection molding experts must maintain procedures for monitoring and controlling process parameters for validated processes. They must also guarantee that validated processes are performed by qualified individuals. These re-validations can be required anytime processes or equipment are changed.
Validation Of Processes
Process validation means “collection and evaluation of data - from the process design phase - thorough production." This approach establishes evidence that a process is capable of consistently delivering quality products. This description is also a verbatim definition from the FDA.
This validation needs to be performed when the process is not yet fully verified by inspection or testing. For injection molding for these specific critical components, the detailed and successful process validation needs to be defined and approved - especially after producing the medical device that consistently performs according to customer specifications - before production runs can be begin.
Before beginning process validation for injection molding - experimentation needs to happen by changing process parameters. This is done to better determine which process variables have the most impact on the product as-well-as how far these process variables can be varied.
At every stage documentation must be kept which details inspection results, parameter settings and any other deviations from the expected performance including every reason for them. Only after all process validation procedures have been successfully completed and approved - can production begin.
These controls use a combination of resources including technology, equipment, materials and personnel. Documentation of the process validation is kept in order to show the achievement of planned results - and the ongoing maintenance of the procedure. If any part of the proving process is changed, the changed process must be re-validated.
For the market expertise in injection molding validation - consider working with the industry experts - those of us who have been on the guiding-edge of the injection molding processes for as long as plastics have been around.
Cleanroom for Medical Device Manufacturing
Because of the need for minimally contaminated or even sterile production, many medical devices must be manufactured in highly controlled environments. That makes cleanrooms a critical part of some medical device manufacturing processes, so make sure your contract manufacturer has access to cleanroom facilities.
Cleanroom facilities may have different requirements based on their application, so multiple ISO classes exist to distinguish between them. Two of them are:
- ISO Class 8, which requires that cleanrooms perform 10–25 air changes per hour and have no more than 100,000 air particles per square foot.
- ISO Class 7, which requires that cleanrooms perform 30–60 air changes per hour and have no more than 10,000 air particles per square foot.
Crescent Industries is capable of providing medical device contract manufacturing services under multiple cleanroom conditions, as we perform plastic injection molding in an ISO Class 8 and assembly and packaging in an ISO Class 7 environment.
Crescent Industries: Your Medical Device Contract Manufacturer
Medical devices can save lives, so they must be produced with the utmost quality and care. Strict regulations from federal and non-governmental organizations exist to ensure best practice implementation, and both certifications and registrations can be obtained to prove that these standards are upheld.
At Crescent Industries, we are not only ISO 13485:2016 certified and FDA registered, but we have access to cleanroom technology to ensure that all medical components can be fabricated under the conditions they require. We offer medical device injection molding with a variety of plastic resins, and can provide design feedback along the way to ensure optimum product quality. Contact us today to see how our experts can engineer your medical device, and put our expertise to work.
Topics:
Related Articles
-
Mar 17, 2025
Labware & Diagnostic Injection Mold Building and Molding
Medical device molding requires much higher levels of precision injection molding and tolerance...
-
Jan 10, 2025
Benefits of a Plastic Medical Device Manufacturer
Reusable and single-use plastic medical devices are held to high standards of sanitation, texture,...
-
Jun 07, 2024
The Key Benefits of ISO 7 Cleanroom Standards for Injection Molding
The International Organization for Standardization (ISO) sets strict standards for the safety and...