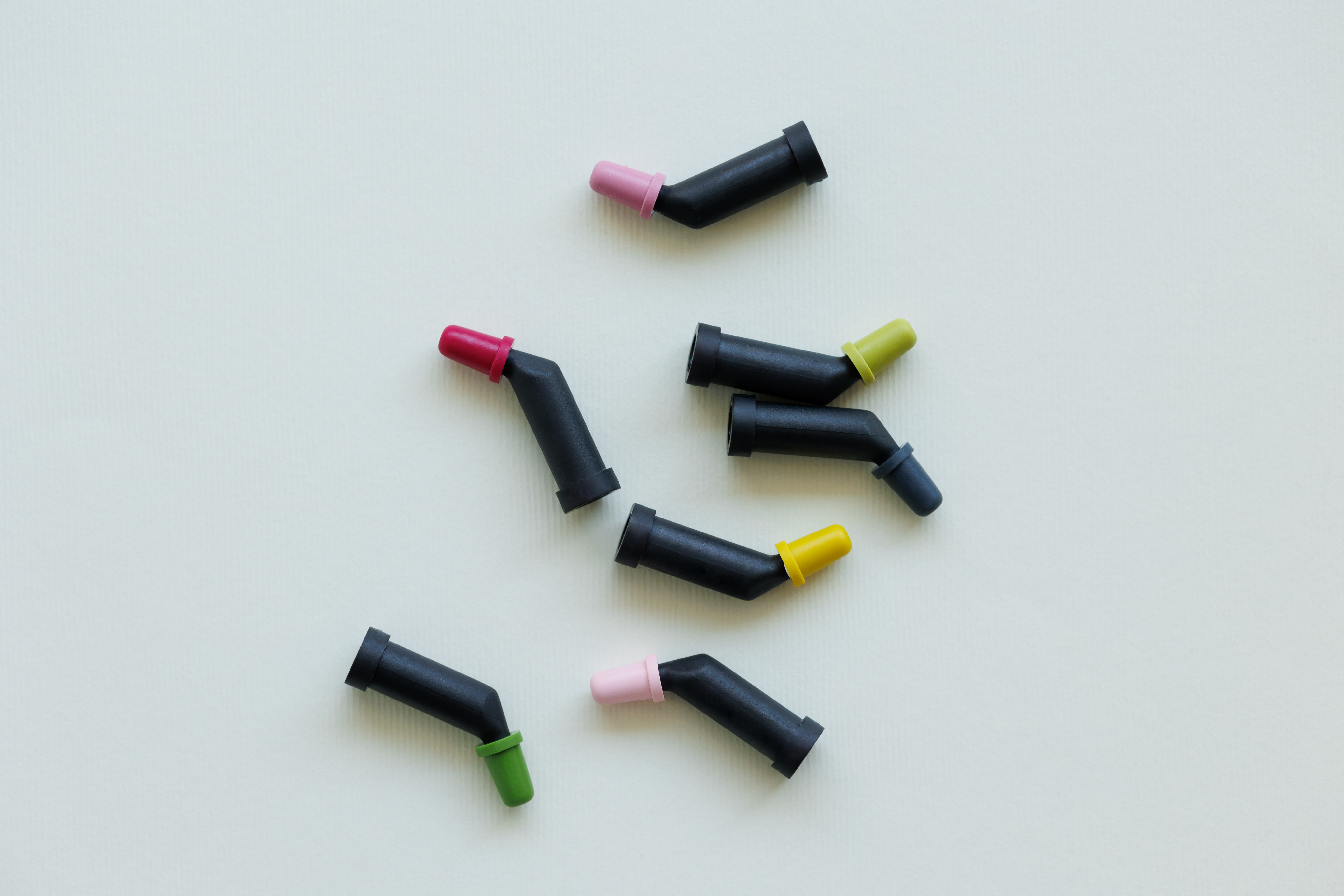
Quality Control for Injection Molding of Dental Components & Devices
While injection molding has existed since the 1800s, its use for dental components and devices has become increasingly popular in recent years. Plastic injection molding offers a fast and cost-effective way to produce precise and uniform products with consistent repeatability. However, as with any manufacturing process, quality control is vital to ensure patient safety and the successful production of high-quality parts. Therefore, when utilizing this method, you must adhere to quality control standards throughout the entire production process, from design to delivery of the finished product.
But what is involved in the quality control process, and how do you ensure your molding components meet industry standards? This article will discuss how to make plastic components for the dental industry safe, focusing on quality control, including the steps you need to take and what materials to use.
Injection Molding for Dental Industry
Before diving into the specifics of quality control, it’s essential to understand the basics of injection molding. Injection molding is a manufacturing process that involves injecting molten plastic construction material into a cavity or mold at high pressure. The injection molding material cools and hardens in the shape of the mold, resulting in a precise and uniform product. The process is incredibly fast compared to other manufacturing techniques, and it can produce high volumes of parts with a relatively short delivery time. This makes injection molding an ideal choice for large-scale production runs.
The dental industry has embraced injection molding as a manufacturing process for effectively creating complex shapes and sizes. In addition, it is a versatile molding technique that can be used for various applications, from dental bite blocks to single-use syringes to compules. However, maintaining strict quality control standards is the key to producing safe and reliable dental injection molded components.
When you think of quality control, consider it an additional layer of safety. Without quality control, you risk producing defective parts that could harm patients. Quality control also ensures that your components are made according to your specifications and meet the required performance standards.
Here is a look at the quality control process and what you must do to ensure safe and reliable injection molding:
Adapting to Specific Manufacturing Requirements for Dental Components
The first and most crucial step in the quality control process is ensuring that your manufacturing processes comply with all applicable regulations and industry standards, such as FDA regulations and the International Organization for Standardization (ISO). FDA’s rules and guidelines ensure dental components are safe and perform as expected. Similarly, ISO standards provide quality systems and process guidelines, such as angular design control and risk management.
For instance, the ISO 13485 standard details requirements for a comprehensive quality management system that you can apply to producing, installing, and servicing medical devices. It also details how to demonstrate that you can provide consistent, high-quality products and services that meet customer requirements.
FDA's 21CFR872 also has specific requirements for dental components. This regulation outlines the requirements for materials used in dental molding, design and construction, performance testing, labeling and packaging, sterilization (if applicable), biocompatibility, and more. The regulation details the specifications for various products, such as dental syringes, retainer cases, and compules.
Material Selection and Precision Molding Techniques
The materials you choose must meet your dental device/component requirements. They should also adhere to FDA’s standards for use in dental components and any additional needs your organization sets. In addition, precision molding techniques are essential for successfully producing high-quality and current design-style parts. You must, therefore, select molding profiles, optimize cycle times, and use the latest molding technology to ensure high-precision parts with consistent performance.
Precision molding makes it possible to reproduce even the most intricate designs accurately. This ensures that quality products meet customer expectations and requirements. Furthermore, precision molding produces parts with a uniform surface finish and tight dimensional control, which is critical for high-precision dental components.
Full Inspections With State of the Art Equipment
Inspections are a crucial part of the quality control process. You must inspect all components to meet current design styles, performance standards, and customer expectations. You should inspect components both pre- and post-molding. Pre-molding inspections involve assessing the molds, materials, and settings to ensure they meet industry standards. Post-molding inspections involve assessing the parts for defects and ensuring they meet performance requirements, such as strength and durability.
To ensure accurate inspections, you should use the latest state-of-the-art equipment, such as optical comparators, micrometers, profilometers, and imaging systems. This equipment can measure and inspect microscopic details with precision, thus assuring that parts meet all the desired requirements.
Product Modifications
The quality control process should also include product modifications, if necessary. Product modifications involve changes to the design situation or manufacturing processes that can improve the performance of a product.
Products may require modifications to improve safety, accuracy, or efficiency. Therefore, you should regularly review your components’ design elements and manufacturing processes to identify improvement areas. This can reduce costs and improve the performance of your products.
Versatility of Plastic Injection Molding for Dental Components
Versatile molding involves the use of various types of materials and processes to create complex parts. It’s an essential aspect of quality control, allowing you to create customized and classic designs for individual customers. This also enables you to produce parts with various finishes and colors, which can help to differentiate your products from other brands.
Learn more about Medical Device Contract Manufacturing for plastic components and devices.
Certifications and Inspections
For enhanced assurance, you should consider obtaining third-party certifications and inspections. This can provide customers with added confidence in the quality of your components and reinforce your commitment to producing safe and reliable products. Obtaining third-party certifications is also a great way to differentiate yourself from other brands in this industry, demonstrating that you have taken the necessary steps to ensure safety and quality.
Plastic Injection Molding Solutions For Your Dental Products or Devices
Your dental products or devices are only as safe as the quality control process to ensure their safety and reliability. Therefore, it’s critical to partner with a plastic injection molding provider with the knowledge and expertise to ensure your products meet all applicable standards.
Partnering with an experienced molder such as Crescent Industries will enable you to produce safe and reliable dental molding supplies that meet your performance requirements. Our advanced engineering capabilities and integrated single-source solution ensure we make components with the highest quality standards. This way, you can be confident that your products will meet customer expectations.
Contact us today to learn how we can help you with your dental injection molding supplies and needs.
Resources
https://www.iso.org/standard/59752.html
https://www.accessdata.fda.gov/scripts/cdrh/cfdocs/cfcfr/CFRSearch.cfm?CFRPart=872&showFR=1
Topics:
Related Articles
-
Feb 15, 2024
How to Ensure High Quality Injection Molding: 6 Best Practices
The widely used practice of injection molding is a highly versatile and efficient manufacturing...
-
Feb 01, 2024
Why Should You Work With an ISO 13485 Certified Injection Molder?
In medical device manufacturing, it's important to have a business partner who understands the...
-
Jun 13, 2023
Quality Control for Injection Molding of Dental Components & Devices
While injection molding has existed since the 1800s, its use for dental components and devices has...