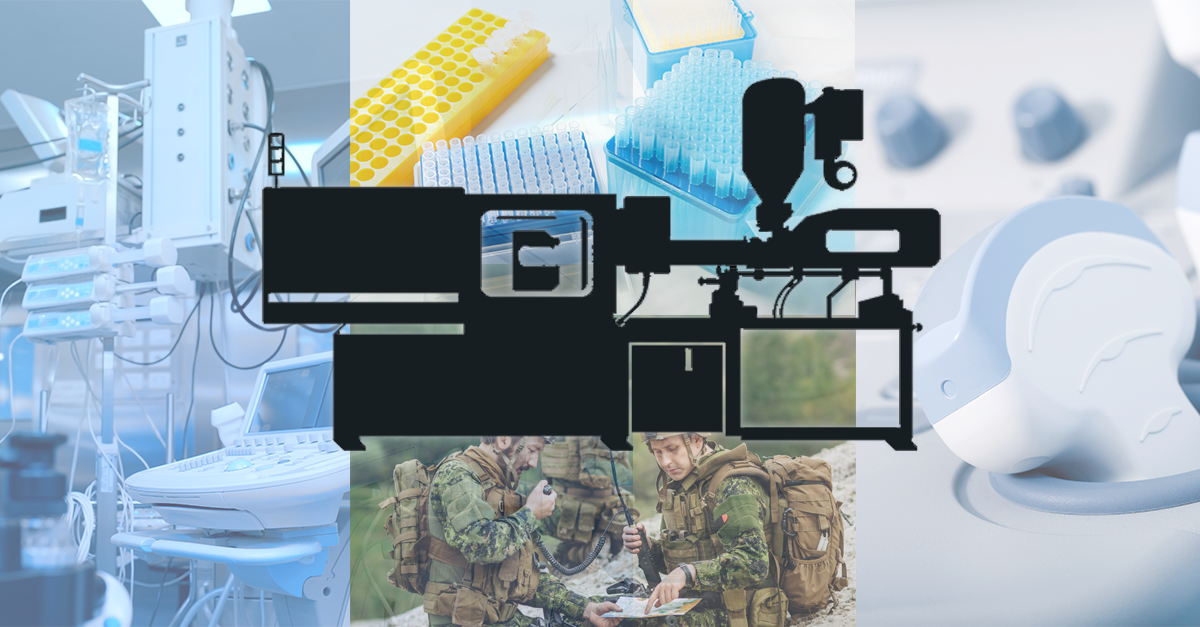
Plastic Part Production Through Injection Molding
In this technologically advanced era, there are different processes to choose from when developing a plastic product. The selection criteria often depend on the commodity type and the product's application. One creative and reliable process that product developers use is injection molding.
Working with a professional plastic injection molding partner like Crescent Industries guarantees high-quality plastic components or devices. In addition, ensuring a stable molding process that is repeatable and reliable is developed will allow easier production of small, medium, and large volumes.
At Crescent Industries, we can use the injection molding process to create custom plastic parts. Here is further insight into the components and factors affecting plastic part production through injection molding.
What Key Parts are Involved in the Injection Molding Process?
The injection molding process mainly involves a mold, an injection molding machine, and a plastic raw material. First, the plastic resin is melted at extremely high temperatures. The injection molding machine then pushes the melted plastic into a mold, which cools and solidifies. Finally, the resin takes the mold's shape, resulting in the final plastic injection molded part.
The Injection Mold
Creating the mold is the first step in the injection molding process. Different precision machine processes build the mold from high-strength steel or aluminum. Injection molds comprise two halves: a core side and a cavity side. Each half contains numerous precision features that ensure the accurate production of plastic parts.
During the injection molding, the molten resin flows into the mold and fills the cavities through gates and runners. After cooling, the mold opens up, and the machine's ejector rod pushes the final part into a waiting collection bin.
The Injection Molding Press
The injection molding machine comprises a base, barrel, nozzle, material hopper, rotating screw or injector, and a clamping unit. Its base supports the other components and the electronic appliances needed to run the machine. The attached electronic devices regulate the range of the hydraulics, heaters, sensors, and injection pressures.
The Material Hopper
The hopper holds the resin at the start of the injection molding process. It has a dryer component that protects the plastic material from external moisture. The hopper also has small magnets that keep harmful metal pieces from entering the machine. After going through the hopper, the resin enters the barrel, which is heated to a molten state.
The Rotating Screw
The barrel has a rotating screw or injection ram that pushes the molten plastic into the cavities or molds in the clamping unit. The screw rotates as the resin pellets are fed from the hopper into the barrel, pushing the material forward. Its swirling motion mixes and distributes heat evenly throughout the mass, purging any colors or materials left over from the previous run. A cylinder unit also compacts, transports, and agitates the molten resin before it gets to the injection mold.
The Nozzle
The injection molding machine has a nozzle at the bottom of the ejector unit that pushes molten plastic into the mold. Modern nozzles can mix, filter, and cut off the flow of the molten resin, minimizing contamination and clogging of the machine.
The Clamping Unit
The clamping unit opens and closes the injection mold. This part allows the ejection of plastic injection molded parts. There are two central clamping systems: the toggle and hydraulic configurations. The toggle system comprises a series of linkages, while the hydraulic set has several hydraulic cylinders.
Each clamping system comprises two metal plates held together when the molten resin gets injected into the mold cavity. The clamping unit then opens after the plastic cools, allowing the formed plastic part to fall out.
Resin Raw Material
Plastic resins are vital materials for manufacturing plastic components and devices.
Depending on your product's requirements, many choices for resin raw materials fall into two main categories, commodity or engineered resins.
A few of the most common materials used in injection molding include:
- Polycarbonates
- Nylon
- Propylene
- Polyethylene
What Key Factors Affect the Plastic Injection Molding Process?
Numerous scientific breakthroughs have made the injection molding process far more predictable and efficient. A few key parameters critical to an optimal plastic part production process include:
Plastic Resin Flow Rates
The resin injection rate into the mold has to be optimal enough to produce a plastic injection molded part successfully. A slow plastic flow rate increases shrinkage and warping as the molten plastic cools quickly. This shrinkage lowers the quality and shortens the lifespan of the final product. Meanwhile, a high flow rate increases the mold's pressure, which may overflow.
An optimal resin flow rate fills the mold cavity at least 95% to 99%. Manufacturers can fill the remaining space once the pressure in the cavity subsides to compensate for any shrinkage.
Cooling Rate
In any injection molding process, the cooling rate is a crucial factor. The cooling process begins as soon as the molten plastic enters the mold. At first, the part cools rapidly but gradually slows down as it approaches the mold temperature; the cooling rate differs across various plastic materials.
The injection molding process also determines optimal cooling rates based on mold and part designs to avoid certain defects. These defects include delamination, shrinking, and warping. The wall thickness and geometry also determine the plastic injection molded part's cooling rate. An experienced injection mold provider ensures even cooling by using cooling channels to prevent undesirable outcomes.
Melt Temperature
Molten plastic resin can easily acquire the shape of a mold. The optimal heating temperature at the barrel, nozzle, and mold ensures that the final plastic part achieves the desired properties. The nozzle and barrel temperature directly influence the molten resin's flowability through the injection mold.
Optimal barrel and nozzle temperatures are often set between the plastic's thermo-decomposition and melting point for proper plasticization. Extremely low melting temperatures slow the flow, create ripples, and lead to unfilled mold parts. Meanwhile, high temperatures can result in flashing and resin overflow.
In addition, the barrel temperature is often higher than the nozzle temperature. If set too low, the molten resin will decompose and drool inside the nozzle. The molten plastic can also end up blocking the nozzle.
Pressure
Another vital factor in the injection molding process is plastic pressure. Most injection molded pieces need high injection pressures to avoid quality issues. The pressure applied onto the plastic is known as screw-back pressure since a screw imparts pressure onto the part inside the barrel.
An expert injection molder can increase the screw-back pressure to increase plastic flowability. However, such an increase can cause a thin layer of plastic to flow out of the cavity. Alternatively, decreasing the pressure introduces bubbles and holes in the plastic. Such defects affect the strength and aesthetics of the final plastic part.
To learn more about plastic injection molding, go to the " Complete Guide for Plastic Injection Molding".
Choose Crescent Industries as Your Plastic Injection Molding Partner
Injection molded parts have extensive use in the pharmaceutical, medical, defense, dental, and industrial markets. These industries rely on multipurpose, single-use, durable plastic items that the injection molding process can provide sustainably.
Crescent Industries is a one-stop shop for all your custom-molded plastic parts. Our expert team utilizes advanced engineering methods to improve project turnaround times and efficiency. Contact us now to benefit from our numerous injection molding capabilities and solutions.
Resources:
https://www.academia.edu/51148147/_Herbert_Rees_Understanding_Injection_Mold_Design_b_ok_org_
https://iopscience.iop.org/article/10.1088/1742-6596/1798/1/012042/pdf
Topics:
Related Articles
-
Mar 19, 2025
Top 6 Advantages of Injection Molding for Your Project
Injection molding — the process of injecting molten resin into a mold — is one of the most...
-
Feb 19, 2025
Injection Molding vs CNC Machining: Which Method to Choose?
Every year, humans produce and use countless plastic products in various shapes, sizes, and...
-
Oct 03, 2024
Injection Molding Uses: Exploring Applications Across Industries
Injection molding is one of the most versatile manufacturing processes, with a wide range of...