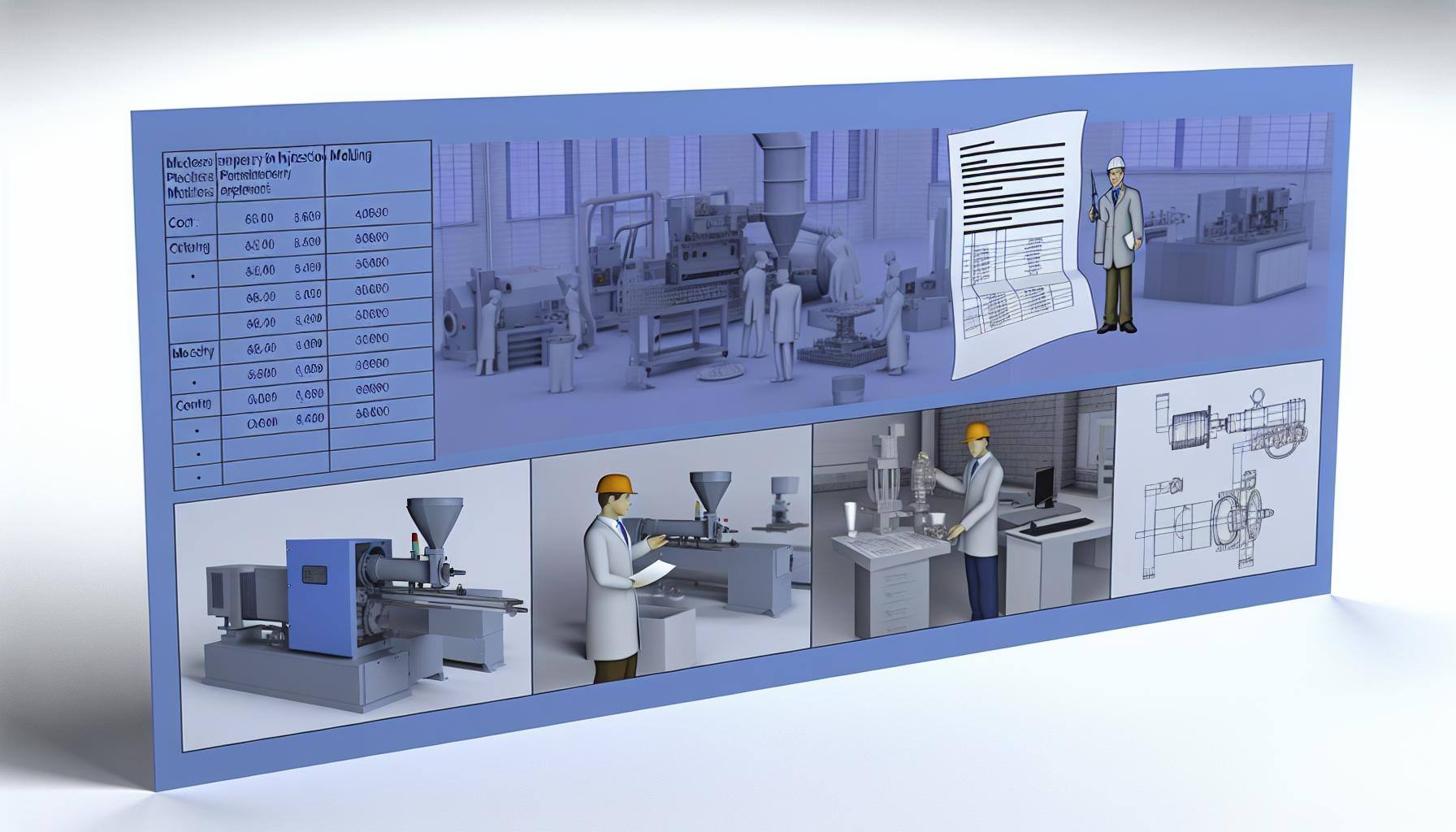
Overview of Plastic Injection Molding Costs
Material cost changes, tooling expenses, production volumes, and even secondary operations, such as finishing and assembly, contribute to the overall expenditure.
Working with a reliable, experienced injection molding partner and understanding how different factors affect the cost of injection molding can help keep your expenses down without sacrificing quality or delivery time.
The Cost Factors in Injection Molding
In addition to supply chain upheavals, many other factors impact the cost of the injection molding process. Here are just a few of the most significant.
1. Material Selection Impact on Cost
Material costs don't just depend on the price per pound of resin. They also include price changes due to material properties, availability, and market volatility. Different resins come with different price tags. Commoditized resins, including Polyethylene (PE), Polypropylene (PP), and Acrylonitrile Butadiene Styrene (ABS), are generally more cost-effective than engineering resins, such as Polyamide (PA) or Polycarbonate (PC). High-performance materials such as Polyether Ether Ketone (PEEK) or Polyphenylene Sulfide (PPS) can skyrocket costs due to their specialized properties and relative scarcity.
The cost can significantly increase if a particular material is in high demand or low supply. Being flexible with material choices can help your business handle this fluctuating availability and build resiliency into your supply chain.
2. Mold Types and Cost Considerations
The type of plastic injection molds you choose can significantly affect upfront costs and long-term production expenditures. Aluminum molds are usually less expensive but less durable, making them ideal for prototype runs. Conversely, hardened steel molds are costlier initially but offer a longer lifespan, becoming more cost-effective over large production volumes.
The more complex the mold design, the higher the tooling cost. Complex molds with detailed features or multiple cavities require sophisticated CNC machining, specialized coatings, or even hand-finishing, all of which add to the tooling cost. Mold size is also a cost factor. Simple, single-cavity molds are generally cheaper but might not be efficient for large production runs as they produce fewer parts per cycle.
All molds require maintenance, including cleaning, lubrication, and, occasionally, repair. However, a mold base with intricate details or tight tolerances is more susceptible to wear and may demand frequent and specialized maintenance. These costs can add up over the mold's lifetime and should be factored into the total cost.
Molds are classified according to their material and the number of cycles they can withstand, as follows:
- Class 101 can withstand over one million cycles. They are best for large-scale, high-precision parts manufacturing and are typically made from the highest quality steel metal mold.
- Class 102 can handle up to one million cycles. They're suitable for less abrasive materials and simpler part designs.
- Class 103 can be used for up to 500,000 cycles. Often made from mid-grade steel, they are cost-effective for less complex parts and materials that are not overly abrasive.
- Class 104 is ideal for 100,000 cycles or fewer. They are best for prototype development or small runs. These molds are often less durable, making them unsuitable for abrasive materials.
3. Part Complexity and Design Costs
The complexity of your part dictates not only the mold cost but also the production time, which directly affects overall injection mold costs.
Complex designs that include complicated elements, such as intricate curves, undercuts, or thin walls, require specialized molds that may require actions that will add to the mold's initial cost.
In addition, tight tolerances require more precise molds, higher-quality materials, and possibly additional quality control measures. All these aspects increase the mold’s upfront and long-term costs.
Surface finish requirements also increase with part complexity. A high-quality surface finish might require specialized mold materials or coatings, post-mold treatments, or even hand-finishing. While these steps ensure a superior final product, they also add multiple layers of costs to the process.
A mold flow analysis is often necessary for complex parts to anticipate and mitigate potential issues like warping or sink marks. While this step can save costs in the long run by preventing defective parts, it also adds an upfront expense that needs to be considered.
4. Production Volume and Economies of Scale
Thanks to economies of scale, production volume is inversely proportional to per-unit costs in injection molding.
The initial costs for mold creation and setup are fixed. These costs remain relatively constant whether you produce a hundred or a hundred thousand parts. These fixed costs will be amortized over fewer parts in low-volume production, resulting in a higher unit cost. In high-volume production, these costs are spread over many units, substantially reducing the per-part expense.
Achieve Efficiency Gains With the Right Injection Molding Partner
Working with the right partner can make all the difference in optimizing injection mold costs and quality. Crescent Industries is a USA-based, employee-owned plastic injection molding company serving medical, pharmaceutical, dental, defense, and OEM/industrial markets.
Our top-notch engineers have decades of experience in custom plastic injection molding and tool building. We’ll work with you at all stages of your injection molding project to ensure your finished products are of the highest quality. Reach out today to learn more.
Topics:
Related Articles
-
Jul 16, 2024
Overview of Plastic Injection Molding Costs
Material cost changes, tooling expenses, production volumes, and even secondary operations, such as...
-
Jun 21, 2022
What You Need to Know About Injection Molding Cost Estimates
Not all estimates are created equal.
-
Jun 07, 2022
A Good Fit? Take a Look at Your Purchasing Needs for Plastic Parts
Choosing a partner for plastic injection molding is a major decision, involving many overlapping...