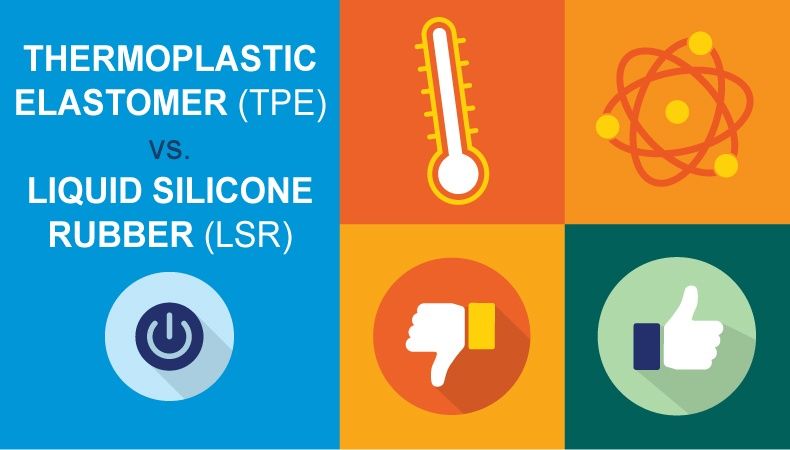
Medical Molding: TPE vs LSR
The medical device industry has a wide range of products and applications that are a fit for medical molding and choosing the right material from the beginning will save significant time and resources.
Often it’s easy to be confused about which “soft material” you should choose for your application when there are so many options, especially when comparing TPE to LSR. The first place to start in your medical application is with the environmental conditions of the application as a beginning point to narrow down the choices.
Your Medical Application
TPE: A great choice for a variety of medical device applications and some implantable devices, cost effective process, recyclable during the molding process, and has a high range of “softness”.
LSR: With high chemical and heat resistant properties as well as less diverse reactions to skin contact, this material is ideal for implantable device applications.
TPE Basics
TPE stands for Thermoplastic Elastomer and in general is a flexible material that can be stretched repeatable to over twice its length with a range of softness on a durometer scale. The most common general application for TPE would be to “over-mold” the TPE on top of a substrate for a “soft touch” type of feel. Typically, TPE’s are most commonly used on handles or areas that would be physically touched.
Traditionally, there were 6 primary TPE types categorized into two generic classes,
- Block copolymers (styrenics, copolyesters, polyurethanes, and polyamides),
- Thermoplastic/elastomer blends & alloys (thermoplastic polyolefins and thermoplastic vulcanizates).
However, over the past few years there have been two additional emerged technologies;
- Metallocene-catalyzed polyolefin plastomers & elastomers
- Reactor-made thermoplastic polyolefin elastomers.
A huge benefit of a TPE over LSR is the recyclability of the TPE. This allows a “re-molding” opportunity with the TPE without a chemical change to the material, this differentiator as well as a less expensive molding process vs LSR will in turn typically have a lower production cost.
According to medicalplasticsnews.com “Medical device manufacturers increasingly turn to thermoplastic elastomers (TPEs) for applications that require flexibility or rubber-like elasticity. These compounds have replaced alternative materials like thermoset rubber and PVC in standard applications like tubing, bags, pouches, drip chambers, masks, cushions, syringe tips, ventilator bags, luers, stoppers, gaskets, seals, and dropper bulbs.
And as designers have come to appreciate the value of TPEs, more and more are using these elastomers for new applications”
TPE growth in medical devices involves their advantages over alternative materials. The most obvious advantages stem from the fact that TPEs are thermoplastics. They process more efficiently and economically than thermoset rubber, provide greater design freedom, exhibit a wider range of color options, and, unlike rubber, can be recycled.
At the same time, TPEs provide device manufacturers with a means of obtaining comparable or even superior properties while avoiding problems associated with certain alternative materials.
LSR Basics
LSR stands for Liquid Silicone Rubber and is typically either injection molded or compression molded. LSR is a thermosetting polymer, which means that once it’s molded it cannot be recycled like the thermoplastic counterpart in TPE. The main raw material is sand or silicon dioxide and is then combined with methyl chloride which can then create different silicone types including liquid silicone rubber.
Much different than TPE, LSR uses a two-component reactive chemical that is mixed, heated up, and then changed into a rubber form. Because the LSR components are shipped in sealed containers and processed with a closed system, there are fewer issues with dust and moisture contaminants.
In medical molding, LSR usage has been increasing over the years for implantable devices mainly because during the molding process it cures completely. This means that the device will not leach chemicals and potentially cause adverse reactions in the patient. Since LSR has an extremely high heat and chemical resistance, it can handle rigorous sterilization processes which make it a good fit for many different applications in the medical industry.
Choosing Your Supplier
Due to the main differences of thermoplastic (TPE) vs a thermoset (LSR) choosing the right supplier for your application can be difficult depending on how many different implantable vs non-implantable products your company produces. Oftentimes, the molding supplier will be focused on either thermoplastic or thermoset types of a material for a majority of their business with some companies having a few machines/processes in their non dominate material.
If your company mainly produces non-implantable products, then it’s a good idea to focus on a TPE molding expert who has all of the certifications and cleanroom facilities to handle most of your product needs. This in turn leaves any implantable products ideal for an LSR application to be sourced to a company that focuses primarily on LSR molding.
Crescent’s Medical Capabilities
Crescent Industries has been providing TPE and thermoplastic solutions to the medical industry for over 50 years. Our application expertise has a wide range of uses in the medical, dental, and pharma industries utilizing their ISO 13485 certification with Class 8 (100K) clean room operations and a Class 7 (10K) clean room for assembly and packaging services. Crescent continues to expand its technology and is dedicated to providing the medical, dental, and pharma industries with the highest quality products solving some of the most challenging applications.
Contact us today to learn how Crescent can assist with your injection molding project!
Topics:
Related Articles
-
Mar 17, 2025
Advancements in Plastics Additives – What to Consider
Plastic additive technology has made some massive advancements over the past 10 years, but with all...
-
May 13, 2024
ABS Injection Molding: Benefits and Process
The types of plastic used to create components and products depend on its strength, heat...
-
Feb 20, 2024
What are Thermoplastic Elastomers?
Have you ever wondered about the versatile materials that seamlessly blend rubber's flexibility...