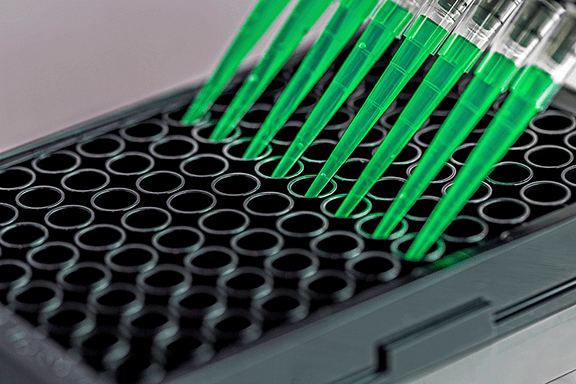
Labware & Diagnostic Injection Mold Building and Molding
Medical device molding requires much higher levels of precision injection molding and tolerance control compared to non-medical applications. This is especially true when the devices are to be used in exact calculations and measurements, like labware and diagnostic tools.
Manufacturers of plastic materials for the medical industry typically develop their expertise and reputation in the sector over decades of work. They also need to stay on top of the latest innovations in manufacturing technology and keep their relevant ISO certifications up-to-date at all times for their products to be recognized on the global market.
Labware and Diagnostic Molding 101
Injection molding for medical devices is a mass production process that aims to replicate results over large batches. Labware injection molding and diagnostic devices require precise injection molds and molding process to avoid production problems.
Diagnostic device and component mold building ensures that the mechanical properties of the parts used by laboratories across the globe yield identical results. This is the case for all medical products that need to meet certain regulatory requirements in order to qualify for sale in the market.
The same mold can be used to reproduce anywhere from a few hundred to tens of thousands of identical plastic pieces. So a lot of precision work is dedicated towards perfecting the fine details of the tooling and ensuring they’re not used beyond their effectiveness. Healthcare providers, labs, and researchers all depend on plastic injection manufacturers to control for dimensional stability in their products, as conformity of results is crucial for delicate operations and experiments.
The Mold Building Process for Labware and Diagnostics
Custom injection molding for labware and diagnostics is a long process that begins well before the production of the first batch. If you require highly specific surgical tools or specialty labware, you should expect to go through the custom mold-building process.
Design and Engineering Considerations
While plastic injection molding is one of the best methods for producing large quantities of the same parts with minimal differences, there are some limitations to the technology. For one, you’re going to need to consider the tensile strength of your design and how much stress it can take. It needs to be able to withstand the de-molding process, in addition to any subsequent polishing and trimming afterwards.
Some designs use a single mold, while others might need two or three separate parts to the mold. The right manufacturer can guide you through the process of finding a balance between design complexity and utility.
Material Selection for Molds
The material you choose determines the parameters of the parts you’re able to manufacture. Rigid materials with little flex are more brittle and harder to de-mold without breaking, so they might need multi-part molds or less complex designs.
Injection molding medical devices you’ll still need to take factors such as material porosity, flexibility, resistance to extreme temperatures and humidity, and hardness into consideration, as well as whether it can withstand repeated use.
Prototyping and Testing Phases
Using computer models and theoretical calculations alone isn’t enough to determine whether the design will work for large-scale manufacturing. You can expect to go through multiple stages of prototyping different options and testing them for wear and tear, reliability, and, user performance.
Benefits of Specialized Injection Molding for Labware and Diagnostics
Opting for medical device manufacturing for producing labware and diagnostics equipment has many benefits compared to other mass-production technologies, including:
- Replicability: Plastic injection molding allows you to produce near-exact replicas of the same product repeatedly with a high degree of precision.
- Lower costs: Plastic injection molding is considerably cheaper than other mass-production techniques. It also benefits from the economy of scale, where each part costs less when you produce more at a higher rate.
- Faster production: The rapid cycle times that medical injection molding is known for allows you to keep up with the fluctuating demands of the healthcare industry around flu and holiday seasons when injuries and illnesses are more prevalent.
- Scalability: Plastic injection molding relies heavily on automation, which makes scaling operations based on demand easier without compromising on cost or product quality.
- Design flexibility: Working with molds, you can produce more complex and detailed designs without having to worry about an extensive and long production process.
- Material choice: You can choose from a variety of non-toxic thermoplastics and resins to find the right balance between durability, flexibility, usability, and comfort.
How Crescent Industries Can Help
Medical device plastic molding for producing labware and diagnostic equipment is a sensitive operation. It requires you to work with highly reputable plastic injection manufacturers with extensive experience and expertise in the medical industry.
Crescent Industries is one such manufacturer that you can trust. We’re an employee-owned, USA-based plastic injection molding company with decades of serving the medical, pharmaceutical, and dental industries, among many others. We put our engineering capabilities towards creating processes that use a wide range of engineered and commodity-grade resins and plastics.
Topics:
Related Articles
-
Mar 17, 2025
Labware & Diagnostic Injection Mold Building and Molding
Medical device molding requires much higher levels of precision injection molding and tolerance...
-
Jan 10, 2025
Benefits of a Plastic Medical Device Manufacturer
Reusable and single-use plastic medical devices are held to high standards of sanitation, texture,...
-
Jun 07, 2024
The Key Benefits of ISO 7 Cleanroom Standards for Injection Molding
The International Organization for Standardization (ISO) sets strict standards for the safety and...