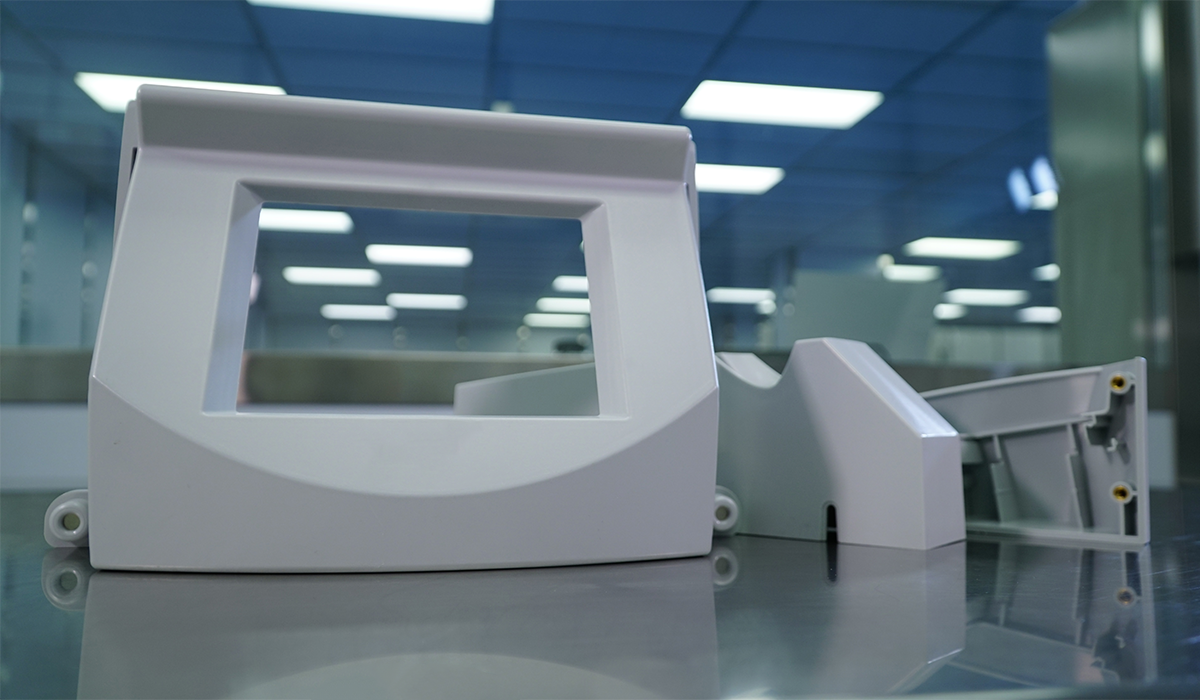
Injection Molding Uses: Exploring Applications Across Industries
Injection molding is one of the most versatile manufacturing processes, with a wide range of applications dating back to the late 1800s. Modern manufacturing techniques enable the production of parts with tight tolerances, diversifying injection molding uses into high-precision industries like medicine, dentistry, and defense.
Benefits of Injection Molding
There are many reasons why businesses use injection molding for their manufacturing needs over other large-scale manufacturing alternatives. Some of the main benefits of injection molding include:
- Cost-effectiveness: The injection molding process is cost-effective as the majority of the investment goes towards designing and manufacturing reusable molds. With high-volume production, this cost splits between the thousands of parts manufactured over the lifetime of the mold.
- Design Adaptability: Mold designs can adopt complex geometries with high precision. You can also custom-make designs that suit your applications in size, durability, material, and surface finish.
- High Production Rates and Consistency: You can use a single mold anywhere from a few hundred to a few thousand times, producing replicas of the same part repeatedly. With injection molding, you can achieve high production rates without worrying about inconsistencies or drops in quality.
What Is Injection Molding Used For?
The versatility of injection molding has made it the go-to solution for a steady supply of high-quality parts made from a variety of plastic materials like polymers and alloy steel. Manufacturers can produce everything from single-use plastic syringes for the medical industry to high-heat resin equipment and weaponry for the military.
Even within the same industry, injection molding has different uses that serve niche applications, whether durable personal protective equipment (PPE) or precision-made, non-reactive labware. At Crescent Industries, we work primarily with healthcare providers, defense, and Original Equipment Manufacturers (OEM), with injection molding uses that include:
Medical Devices Uses
The medical industry uses plastic injection molding as a source of reliable and sterile equipment that facilitates the safety and comfort of the patient and their healthcare provider. A few of the most common applications of plastic injection in the medical industry include:
- Labware Equipment & Instrumentation: The precision manufacturing of plastic parts means they can be used reliably to measure specific quantities in a laboratory setting. Also, lab technicians can use non-reactive and durable plastics when handling hazardous and toxic materials.
- Diagnostic Disposables: Syringes, fluid collection bags, PPE, and sample collection swaps are all single-use equipment medical professionals use during patient visits. Diagnostic disposables must meet safety standards for both patients and service providers.
- Emergency Medical Devices: Thanks to the relatively fast production cycle of plastic injection parts, hospitals and clinics can request medical device injection molding on short notice.
- Orthopedic Surgical Instruments & Devices: Polymer composites and custom-made implants can be used in orthopedic surgical procedures to help correct fractures and replace damaged joints.
- Regenerative Medical Devices: Tools and implants made from biocompatible plastics can aid in proper tissue regeneration, repair, or replacement. It’s a specific type of plastic that promotes cell growth by mimicking human tissue.
- Surgical Instruments & Devices: Disposable scalpels, wound drains, endotracheal tubes, speculums, and catheters are all examples of plastic devices and instruments often used during surgery and patient examination.
- Dental: The dental industry requires access to reusable and single-use plastic equipment such as impression trays, saliva ejectors, disposable suction tips, syringes, and mixing spatulas.
Industrial Manufacturing Uses
OEM industrial injection molding offers accuracy and high-volume production. The replicability of results makes injection molding more reliable for assembly and large-scale manufacturing for industries such as:
- Aerospace: The low weight and tight tolerances of plastic parts made with injection molding make them ideal for aerospace use. Many planes opt for plastic bezels, blades, and controllers to cut costs and weight in their manufacturing.
- Electrical: Plastic is an ideal material for electrical applications as it’s effective at insulating electrical currents, ensuring safer installation of electrical work. Many electrical components are made using injection moldings, like panels, adapters, sockets, and junction boxes.
- Electronic: The casing and buttons of electronics are often made with injection molding. This minimizes variation between multiple product patches and isolates the electrical components from users’ hands.
- Telecommunication: The short production time of plastic components makes them ideal for telecommunication companies to regularly update their networks and infrastructure and fix issues when old components break.
Military Uses
The defense industry often relies on plastic injection molding for mission-critical applications because of its reliability and precision. Military injection molding uses include:
- Handheld Communication Devices: Injection molded plastic in military handheld transceivers can withstand combat conditions and won’t degrade with exposure to sun, water, or extreme temperatures.
- Weaponry: The plastic components in weaponry must have tight tolerances to fit other components during assembly. Often used in the grip or controls of a machine, these plastic pieces must have uniformly textured surfaces to facilitate a sure grip.
- Binocular & Monocular Housings: Using plastic in the casing of binoculars and monoculars ensures the lenses don’t sustain any damage from falls and they’re kept safe from harsh environments.
- Munitions: The lightweight and durable plastics of injection-molded munitions make them ideal for military and defense uses. They can be used in anything from flash bangs and impact munitions to sting-ball grenades.
- Guidance Systems: These systems attach to ships, aircraft, missiles, or satellites, so they must be lightweight and durable for optimal application.
Choosing Crescent Industries for Your Injection Molding Needs
Employee-owned and USA-based, Crescent Industries is a leading single-source plastic injection molding company. Our team of expert engineers carefully designs every step of the injection molding process, manufacturing a wide range of materials with the uttermost precision, including medical, pharmaceutical, dental, defense, and OEM.
Contact us and schedule a call to learn how we can help your business with custom plastic parts.
FAQs
What is injection molding used for?
Injection molding is used to produce high-quality, durable plastic components for various industries, including medical, industrial, aerospace, and military.
What are the applications of injection molding?
Applications of injection molding include medical devices, industrial components, military equipment, and electrical and optical parts.
Topics:
Related Articles
-
Mar 19, 2025
Top 6 Advantages of Injection Molding for Your Project
Injection molding — the process of injecting molten resin into a mold — is one of the most...
-
Feb 19, 2025
Injection Molding vs CNC Machining: Which Method to Choose?
Every year, humans produce and use countless plastic products in various shapes, sizes, and...
-
Oct 03, 2024
Injection Molding Uses: Exploring Applications Across Industries
Injection molding is one of the most versatile manufacturing processes, with a wide range of...