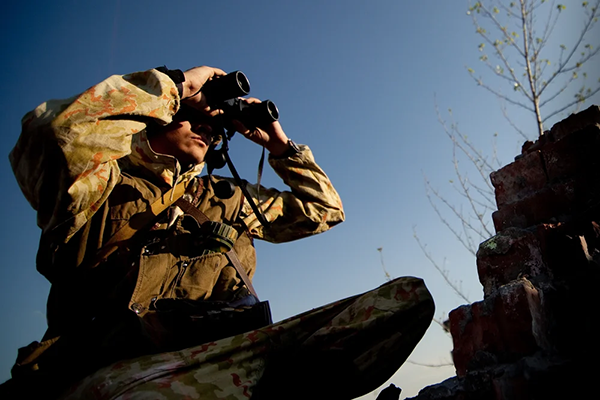
Injection Molding Solutions for Military & Defense Markets
High-performance injection molded parts have been making inroads into defense applications for years. The combination of highly engineered resins and the inherent advantages of injection molding continues to deliver components that can meet the precision, durability, reliability, performance, and environmental requirements of military applications. In addition, injection molded parts can resist the degrading effects of moisture, heat, abrasion, and chemical contact while maintaining minimal flame, smoke, and toxicity (FST) dangers for the military personnel who rely on those parts.
Advantages of injection molded parts for the defense industry. Injection molded plastic parts have replaced machined metal components in many defense applications, due to the former’s many advantages over the latter:
High strength and lighter weight. Many high performance resins can provide the same mechanical strength as machined metal parts—and often weigh less. For firearm components and other parts that must be carried by military personnel, that lighter weight translates into greater ease of movement on the battlefield, as well as the ability to carry more of the equipment needed to complete the mission.
High value. Injection molding (especially when hot runner molds are used) wastes very little material. Also, plastic parts can very often be molded into the final desired shape without secondary machining, thus avoiding the loss of the material machined away as well as the labor costs necessary for that machining. Both of these features often make injection molding more cost effective than machining metal parts. When robotics and advanced automation are well integrated into the injection molding process, then the cost advantages become even more compelling.
Compatibility with mass production. Injection molding is the preferred method for the high-volume production of plastic parts across many industries, including defense. For large production volumes, low costs per part can be achieved, even while meeting tight tolerances and low defect and scrap rates. Plastic injection molding produces exceptional product quality and accommodates high production quantity.
For defense applications, this advantage is vital because orders of defense-related products can be very large, especially when conflict erupts.
Ability to reliably meet tight tolerances. Technologies such as die-sink and wire-sink EDM, high precision CNC milling, and powerful mold fill simulation software enable injection molding contract manufacturers to meet the demanding tolerances required of the defense industry. Technology, as helpful as it is, is not the only tool needed. Robust mold design skills and the processing capabilities needed for recurring production are also necessary for hitting those tight specs, part after part.
Wide selection of material properties. Due to the abundance of polymer and additive options, a compounded resin can have many possible properties. These include resistance to heat, oil, abrasion, impact, scratching, chemical reagents, and ultraviolet light. Resins can also be formulated for specific usable temperature ranges, flexibility, stiffness (i.e. durometer), optical transparency, electrical conductivity, flame resistance, lubricity, and strength.
The vast selection of materials available provides a great match for the varied performance requirements of defense applications. Whereas some parts like armament components may be constantly exposed to abrasive materials such as sand, other parts like gaskets may not be exposed to the elements, but may require resistance to specific chemicals instead.
Injection molding solutions for military & defense. As the demand for injection molded plastic parts by the defense industry has grown, leading injection molders have risen to their unique challenges by providing defense customers solutions such as sand, other parts like gaskets may not be exposed to the elements, but may require resistance to specific chemicals instead.
Molding facilities that are International Traffic in Arms Regulations (ITAR) registered and possess Federal Firearms Licenses (FFL). Besides showing that a molder meets regulatory requirements, ITAR registration and possession of an FFL also demonstrate that a contract injection molder has the knowledge of the stringent demands of defense products—and the experience to reliably meet them.
Engineering expertise. Molders with an in-house engineering team can more closely and productively work with a defense customer’s own engineering and design staff. By providing crucial guidance on polymer and additive material selection, part features, and geometry modifications early in the design phase, costly re-designs and production problems can be avoided. Such in-depth Design for Manufacturing (DFM) assistance is a real asset to OEMs in the military and defense markets where durability and reliability of the molded part, along with the repeatability of the process used to mold it, is paramount as failure in the field could be disastrous to soldiers, civilians, and the mission.
Complex secondary operations. From ultrasonic welding to EMI/RFI shielding, molded parts commonly need additional steps before they are ready for the battlefield. Only a select few injection molders are capable of providing these additional value-added operations to military standards and therefore provide the cost savings and efficiency of one-stop shopping for defense customers.
The ability to meet demanding quality requirements. An injection molder with quality certifications such as ISO 13485 has proven that they can meet the rigorous measurement and documentation requirements necessary for defense products. From inspection and test to corrective and preventative actions (CAPAs), adherence to quality system standards enforces and maintains a process and other controls throughout the entire production facility. For defense customers, this translates into more reliable, safer, and higher performing components.
With engineering expertise, mastery of Scientific Injection Molding (SIM), and decades of experience in injection molding for military and defense markets, Crescent Industries is the FFL and ITAR registered injection molder defense OEMs turn to.
Topics:
Related Articles
-
Mar 21, 2023
Plastic Injection Molding Military Components
Military components must withstand harsh conditions and not fail. On the battlefield, a...
-
Sep 27, 2018
Injection Molding Solutions for Military & Defense Markets
High-performance injection molded parts have been making inroads into defense applications for...