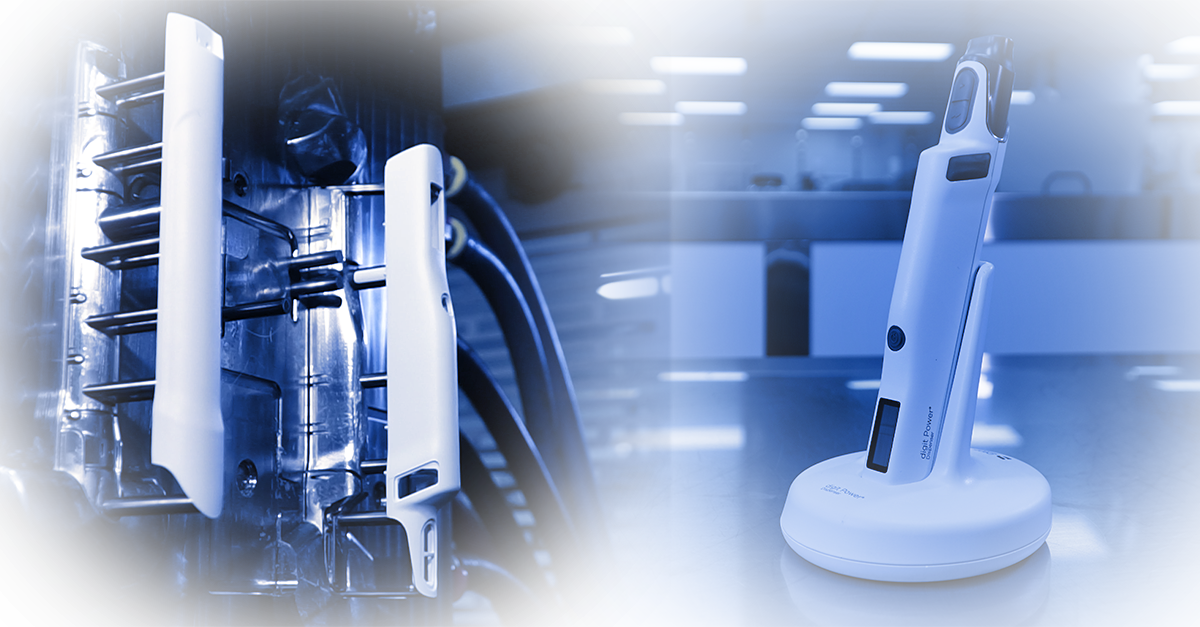
Injection Molding for Medical Devices: Benefits and Considerations
Injection molding for the medical sector is a fast-growing area, with rampant growth expected to continue at least through 2025. In fact, medical applications are forecasted to be the biggest driver of injection molding growth over that five-year period. When you consider the benefits of injection molding for medical devices, that growth should come as no surprise — and we will look at those benefits throughout this piece.
Companies turn to outsourced injection molding services for their medical device products for a number of reasons, including:
- Access to expertise: A dedicated injection molding partner is committed to one thing: top-of-the-line plastic injection molding. The experience and expertise of an injection molding partner provides peace of mind that each part or component will be designed, engineered and manufactured with a focus on your success and satisfaction.
- Stringent standards: When you are using plastic injection molding for medical parts, numerous standards must be met. At a minimum, an injection molding partner should be certified to ISO 13485 standards for medical devices. Working with an experienced injection molding manufacturer with expertise in the medical field — including knowing which regulations apply during the manufacturing process — will ensure that the finished product meets all required guidelines.
- Risk mitigation: While injection molding is a very versatile and relatively straightforward process, risks are still involved, especially as part designs are becoming more complex. A dedicated injection molding partner can provide risk mitigation services such as PFMEA (Product/Process Failure Mode and Effect Analysis), which quantifies and assesses process variables to minimize risks such as part defects before they occur. Other risk mitigation tactics include mold-fill simulation to optimize tool design, and project management to keep orders on budget and on schedule. All of these services add up to a reliable, consistent process, maximizing quality and minimizing unexpected costs.
Risk Management: Tips When Launching a Project
Now that we’ve discussed what it looks like to use a partner for injection molding in the medical industry, let’s examine the benefits of the process itself.
Benefits of Injection Molding for Medical Devices
Injection molding offers a number of benefits for medical manufacturing. These include:
- Medical-grade materials: With injection molding, parts and components can be created from optimal medical-grade materials. Other plastics — such as polyethylene, polypropylene and polystyrene — offer various material properties suited for medical devices and applications, including high strength, resistance to breaking, and, for certain materials, the heat resistance required for autoclave sterilization.
- Design flexibility: Injection molding is a highly versatile process, allowing for complex design features while offering high precision. Because the plastic takes the form of the mold cavity, complex geometries can easily be achieved over and over. While there are some restrictions and best practices for manufacturability in injection molding, in general the process is extremely versatile.
- Accuracy and repeatability: As mentioned above, the nature of the injection molding process makes it extremely accurate, allowing for high repeatability and tight tolerances. Note that the design of the mold itself matters, as factors such as flow rate and fill time can affect the quality of the finished product. Be sure to choose an injection molding partner with experience in optimizing mold design — not all molds are built the same.
The Medical Device Injection Molding Process
While the injection molding process is the same for medical manufacturing as it is for other industries — injecting molten plastic into mold cavities, allowing it to cool and harden, ejecting the parts, and repeating the process — there are special considerations for medical applications, such as:
- Engineering partnership: When working with an injection molding partner for medical device and component manufacturing, it is vital that engineering teams cooperate to make certain that every aspect and component of a device works together properly.
- Medical device injection molding prototyping: Prototyping is important for any product but is especially significant in the medical field. The accuracy, strength and safety of every medical device and component is paramount, and prototyping helps to ensure that the required benchmarks can be met in the production process.
At Crescent Industries, we offer decades of experience in medical and pharmaceutical injection molding, with expertise in delivering accurate, high-quality parts that meet all necessary regulations. We are ready to assist and partner with you for prototyping, engineering, certification and validation, along with all other aspects unique to the medical production process. To further discuss our services, contact us today.
Resources:
https://news.thomasnet.com/featured/medical-sector-drives-growth-in-plastic-injection-molding/
https://www.mddionline.com/pros-and-cons-injection-molding-medical-device-manufacturers
https://www.stackplastics.com/medical-molding
https://www.crescentind.com/medical-and-pharma-injection-molding
https://www.crescentind.com/product-design-and-prototyping
https://info.crescentind.com/blog/risk-management-tips-when-launching-a-new-injection-molding-project
https://info.crescentind.com/blog/how-you-can-minimize-risk-for-your-outsourced-injection-molded-parts
https://info.crescentind.com/blog/bid/63310/ways-to-ease-risk-factors-when-sourcing-injection-molds
Topics:
Related Articles
-
Mar 17, 2025
Labware & Diagnostic Injection Mold Building and Molding
Medical device molding requires much higher levels of precision injection molding and tolerance...
-
Jan 10, 2025
Benefits of a Plastic Medical Device Manufacturer
Reusable and single-use plastic medical devices are held to high standards of sanitation, texture,...
-
Jun 07, 2024
The Key Benefits of ISO 7 Cleanroom Standards for Injection Molding
The International Organization for Standardization (ISO) sets strict standards for the safety and...