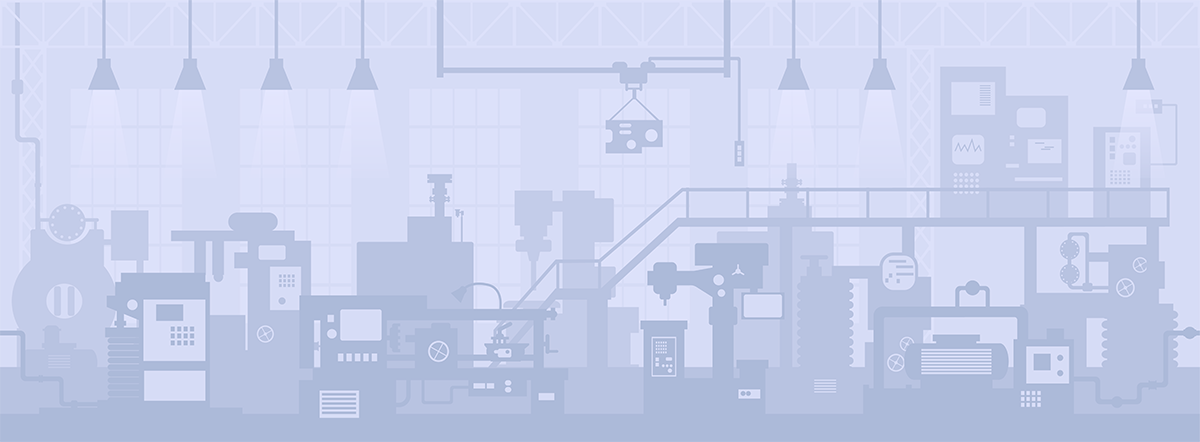
How to Include Injection Molding DFM in Your Manufacturing Process
Original equipment manufacturers that are preparing to produce an injection molded component have many good reasons to include design for manufacturability (DFM) in the process. Through plastic injection molding DFM, you can identify a range of problems that, if not addressed, would affect the strength and appearance of components and would be costly and time-consuming to solve.
Follow the steps and best practices below in order to:
- Understand what injection molding DFM consists of
- Anticipate what you’ll need to do as an OEM when engaging in design for manufacturability
- Ensure that you’re working with a CM that is qualified to lead your DFM process
Understanding Injection Molding DFM
Design for manufacturability (DFM) is a process that’s used to identify and address potential problems in the design phase. Design for manufacturability can be done in any type of manufacturing, but in plastic injection molding, there are specific problems that it’s used to solve. Defects that occur in plastic injection molding can be caused by flaws in part design, mold design, material temperature, injection pressure, cooling time, and other parts of the manufacturing process. Nearly all of these types of defects can be predicted and avoided through DFM.
Key phases of injection molding DFM include:
Analysis of Plans and Identification of Concerns
Engineers inspect all existing plans, documentation, and information regarding the project, including as many details as possible about not just the component but the overall product and its uses. Any concerns about potential manufacturing problems with the project are identified and shared with the engineering team; these can include issues that have come up if the component has been manufactured previously, or when similar components have been produced.
Mold Fill Simulation
Specialized mold flow simulation software, such as Sigmasoft, is used to simulate the injection molding processes. This produces real 3D simulations of flow, heat flux and warpage for injection molding. Simulations can be run based on an imported part design or mold design, or a process simulation can be conducted. Based on the simulation, engineers inspect the project for all of the parameters in the checklist for DFM in plastic injection molding, identifying any problems that will occur unless changes are made to the design, mold, materials, etc.
Presentation of Results and Recommendations
Engineers prepare and share the results of the simulation and recommend the best solutions to the problems identified. They prepare and present a document communicating the results of the DFM process and the resulting recommendations, including screenshots from the simulation process.
Prototyping, Testing, and Completion
Often the DFM process continues with use of 3D printing (additive manufacturing) to carry out prototyping and creation of parts for the OEM to test. As needed, portions of the DFM simulation described above can be repeated, along with prototyping and testing, until the product is ready for manufacturing.
OEM’s Role in Successful DFM
For OEMs engaging a contract manufacturer to carry out their plastic injection molding project, a qualified CM should lead and carry out the DFM process. That said, the OEM plays a crucial role in making the process successful. That role includes:
1. Providing complete handoff materials
Be prepared to provide your CM with your CAD models, 3D models, and other planning documents, as well as any existing prototypes or samples of previously manufactured iterations.
2. Engaging in Pre-DFM consultations
Expect to have at least one if not more consultations with your CM prior to and during the Analysis of Plans and Identification of Concerns phase. This allows the CM to ensure that all relevant factors are taken into account when planning the project, and provides the opportunity for the engineering team to share observations that can lead to a more productive DFM process.
3. Providing as many details as possible
With a signed CDA and NDA in place, the best results from the DFM process come when the CM knows as much as the OEM’s engineers do about the end use of the product and all the different components that it interfaces with. Share as many details as possible, understanding that some constraints may apply to projects regulated by International Traffic in Arms Regulations and other policies.
4. Facilitating ongoing communication
As the DFM process progresses, and often through manufacturing itself, communication among all parties is a good predictor of success.
Identifying the Right Contract Manufacturing Partner for DFM
Not all contract manufacturers are equipped to prepare your project for success using DFM. When looking for a plastic injection molding contract manufacturer, make sure to:
- Ask their sales team if they provide design for manufacturability as a service
- Consult their website for a description of their DFM services along with any DFM case studies of their past work
- Request to see the list of items they evaluate in their DFM process and compare it to the recommended checklist for DFM in plastic injection molding
- Establish that they employ engineers with extensive experience in custom plastic injection molding and injection mold tool building
- Set up a consultation with an engineer from their DFM team to discuss how they would handle your project
DFM includes recommendations that can necessitate investments in new equipment on the part of the CM, so look for a partner that has the capacity — the facilities and cash position — to respond to these needs.
DFM is an important component of any plastic injection molding project. OEMs can leverage DFM most effectively by understanding the process, being prepared to engage in it effectively, and selecting a qualified CM partner.
Topics:
Related Articles
-
May 20, 2025
Designing for Injection Molding Success: What Every Engineer Should Know
Designing plastic parts for injection molding is both a science and an art. From material selection...
-
Jul 24, 2024
The Evolving Landscape of Custom Injection Molding
A big part of establishing your foothold in any industry is adopting—or at the very least, staying...
-
Nov 21, 2023
3D Printing vs Injection Molding: Pros and Cons
Many manufacturers compare 3D printing vs. injection molding to determine the best method for...