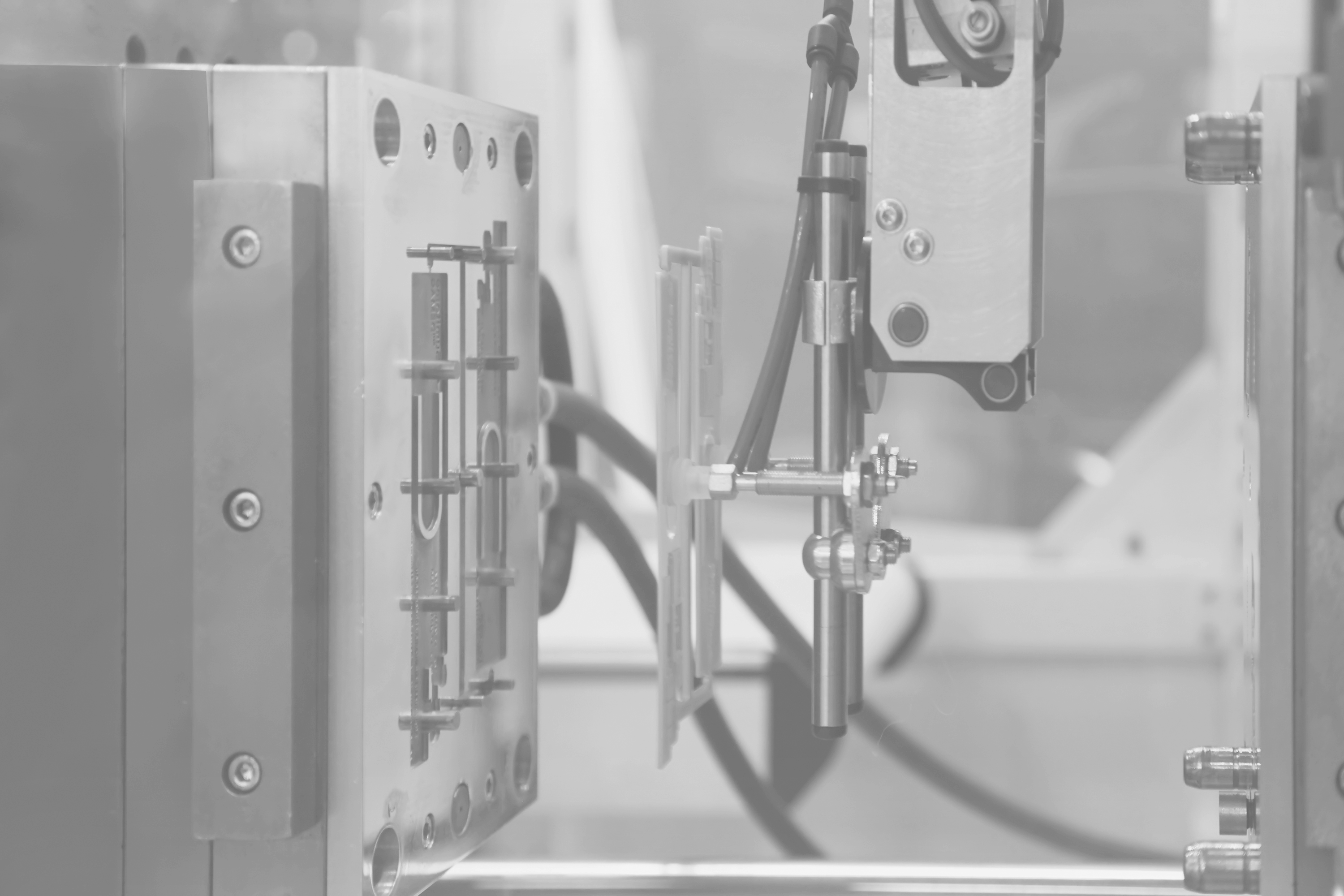
How to Choose the Right Injection Molding Company
(Updated June 2019)
By making parts quickly and economically, injection molding has become one of the dominant fabrication technologies for thermoplastic and elastomeric parts. Injection molding is also the default choice when both high volume production and tight tolerances are required—such as in medical device manufacturing.
While it may be easy for OEMs to select injection molding for making their product, choosing which injection molding contract manufacturer (CM) among the hundreds to do the molding isn’t so simple. Fortunately, by focusing on three key areas: required production capacity, your specific molding needs, and the relevant expertise needed by the molder, OEMs can find the best injection molding partner for them and their product.
Production Capacity: Can the Molder Keep Up with Demand?
Despite the fact that other molding technologies, like transfer and compression molding, have far lower initial setup and tooling costs compared to injection molding, they don’t enjoy injection molding’s economies of scale. The relatively large capital investment injection molding requires gets amortized over the total number of parts that get molded. The OEM’s production requirements are therefore key to realizing the long-term cost benefits of injection molding, and by extension critical for enjoying a beneficial partnership with their outsourced injection molding partner.
For instance, an injection molding company with in-house expertise in high-throughput mold design can support an OEM as production volumes rapidly increase due to increasing market share and customer demand. It’s good practice to design a large amount of reserve throughput into a production process and idle the line when necessary, as opposed to outgrowing a process and then having to spend yet more money to bring up a higher capacity solution. Designing tools with multiple cavities is one standard way to increase production capacity.
Multi-cavity tooling multiplies the number of molded parts per cycle, boosting annual yields while reducing the required cycle time per part. More cavities in the mold, however, require more tonnage at the press, so the injection molder must match their mold design skills with appropriate production equipment. Have the molding CMs you’re currently considering investing in the machinery necessary to make your product a business success?
The same argument can be made regarding another requirement for high quality, high volume manufacturing: automation.
Modern collaborative robots (“cobots”) can work safely in close proximity to human workers and can be fitted with specialized end of arm tooling (like grippers, nippers, and vacuum cups). Combining cobots with fully automated work cells, which start at the injection press and end at the shipping pallet is the cutting edge of factory automation. Injection molding CMs have invested in these technologies and the skilled personnel to integrate and support them. These CMs are the companies who in turn can deliver cost efficiencies and high quality products for their OEM customers.
Can They Satisfy Your Specific Molding Needs?
Depending on the product’s design and requirements, an OEM may need one or more specialty injection molding processes:
- Overmolding: Surrounding an already molded part with another molded material. For example, a plastic tool’s stiff and strong thermoplastic core is overmolded in some areas with a thermoplastic elastomer to provide soft grips that make the tool easier to hold.
- Insert Molding: Same basic concept as overmolding, except that metal inserts are molded over instead of previously molded resins. One common use of insert molding is to incorporate threaded metal inserts into molded plastic cases for robust, yet easy assembly.
- Cleanroom Molding: By performing the injection molding in a cleanroom, part defects, and machine downtime due to accumulated contaminants are reduced, resulting in more consistent outcomes as well as increased patient safety.
- Use of Hot Runner Molds: By keeping the thermoplastic resin inside the sprue and runners molten, less resin is wasted each cycle. Hot runner tooling is particularly important for expensive resins (less waste means lower resin costs) and situations where regrinding the runners isn’t a practical option.
OEMs must understand the needs of their product well enough to spot the injection molder best suited to mass produce their new product since each molded part has its own unique needs.
ExpertiseIncreasingly powerful computer workstations and the sophisticated CAD/CAM simulation software they run have been a boon to design for manufacturing (DFM) analysis in the injection molding industry. Engineering and machining expertise, however, is still needed to translate simulation results into high performance tooling.
When OEMs are visiting and evaluating injection molding companies, they need to investigate the tool design and engineering expertise of each facility they visit. DFM in injection molding is two-fold, because both the part and the mold, which makes it, need to be optimized. For the part itself, the DFM review includes the placement and number of ribs and bosses, wall thicknesses, and core outs. When it comes to mold DFM analysis, draft angles and the positions of gates, runners, and vents are typical areas of focus.
Related to the necessary technical expertise is the scientific injection molding process, which uses methodical experimentation and statistics to maximize consistency and minimize waste. Scientific injection molding is a process that adds considerable value to the injection molding CMs that use it, and savvy OEMs should insist on it.
If OEMs focus on production capacity, molding capabilities, and in-house expertise during their search for an outside injection molding partner, finding the perfect match should be straightforward. For many OEMs in the medical device and defense industries, Crescent has been that match. From tooling design and machining to fully automated production work cells, Crescent is a fully qualified, full-service injection molding CM.
For additional information, please click below to get our white paper "Tips to Assist You in Selecting an Injection Molding Partner".
Topics:
Related Articles
-
Mar 19, 2025
Top 6 Advantages of Injection Molding for Your Project
Injection molding — the process of injecting molten resin into a mold — is one of the most...
-
Feb 19, 2025
Injection Molding vs CNC Machining: Which Method to Choose?
Every year, humans produce and use countless plastic products in various shapes, sizes, and...
-
Oct 03, 2024
Injection Molding Uses: Exploring Applications Across Industries
Injection molding is one of the most versatile manufacturing processes, with a wide range of...