The use of automation and robotics is not just for high-volume production runs. For example, the implementation of cobots, end-of-arm-tooling (EOAT), is often integrated into the manufacturing of custom injection molded parts with low or moderate production volumes.
Why? Because programming collaborative robots and robotics involves performing specific repetitive tasks without variation. The robotic operations use precise guidance and intelligence-based features to include vision, integrated force, and sensing capabilities that an in-house automation team can easily change to match project requirements. As a result, these robotics allow injection molders to achieve specific levels of flexibility to multi-task various functions, which are easily interchanged from one custom product to another.
Cobots are being used more frequently for post-processing operations; they are designed to work alongside humans safely. They can move parts from one place to another to be decorated, assembled, or packaged. They perform repetitive movements accurately, repeatable, and reliably for improved part quality and increased production throughput.
Just simple EOAT like grippers or vacuum cups can be suitable for removing delicate components from the injection mold or soft-grip fingers to pick n place parts for packaging or stacking without damaging the product. In addition, these attachments can be swapped out quickly to meet the specific task for each custom injection molded component.
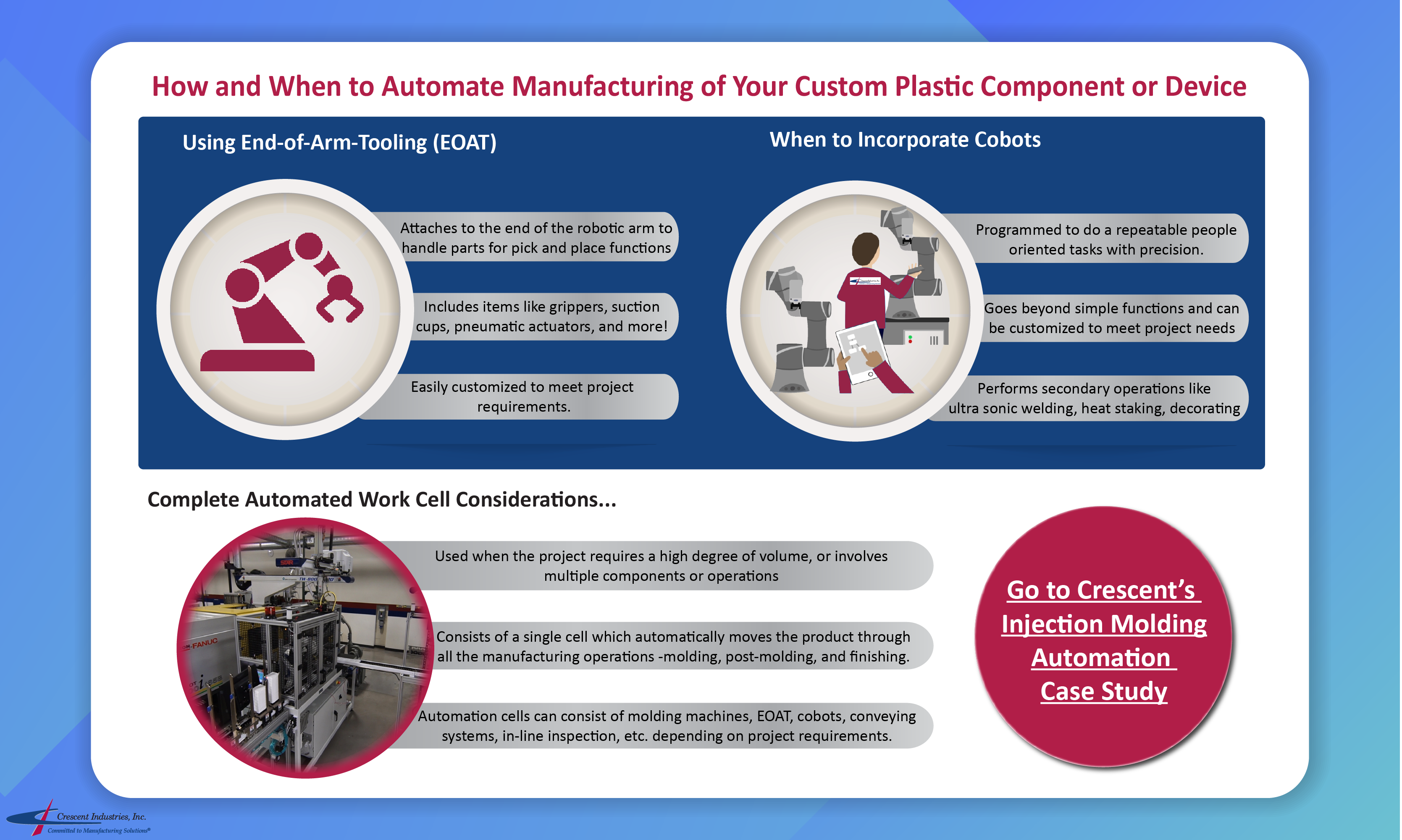
Using robotics and EOAT for even low to moderate volume runs allows your injection molder to deliver consistent results with precision and flexibility. In addition, teaming up with a molding partner adapting to these techniques provides you the competitive advantage of driving speed to market for low to moderate production volumes.
As these technologies continue, automation integration into custom injection molding will continue for high-volume projects and lower-quantity runs. Contact Crescent Industries to see how they can create a manufacturing solution for your next injection molded project.