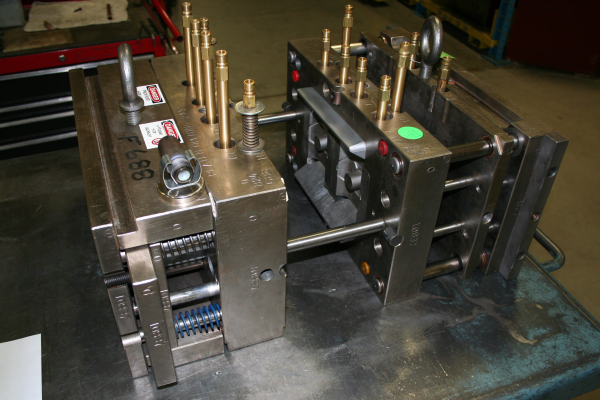
Benefits of Metal to Plastic Injection Molding Conversion
Replacing metal parts with plastic molded parts began during World War II when the demand for metal outgrew the supply, and manufacturing speed took precedence over the product's longevity. By the 1950s, stronger and more durable resins and plastics made plastic parts a viable option. Since then, plastic quality has continued to improve, and now parts made by plastic injection molding are a wise choice for almost any industry. Though injection molding was born out of need, many industries are converting to plastic injection molding over metal parts.
What Are The Benefits of Plastic Injection Molding for Parts?
If your business is currently using metal parts and you have no real complaints, converting to plastic injection molded parts might seem like a hassle. However, take a look at just a few of the benefits of plastic injection molded parts, and you may find a good reason to make the switch.
More Design Flexibility
While metal parts can be custom-made for many applications, they cannot offer you nearly as many design options as molded plastic parts. Plastic adds strength without weight, reinforcing assets like gussets or ribs directly to the molding process and, in many cases, outperforms metal parts.
The ability to customize the blend of materials in plastic parts makes it possible for you to create plastic that fits your needs exactly. You may need a plastic part that is safe for handling food or one that is particularly resistant to scratching or friction. These options and many more can be achieved by carefully selecting the materials before molding them into the exact shape and size you need.
Better Aesthetics
With plastic injection molded parts, you can create any look. They can be molded in various colors, shapes, and sizes without losing functionality. This is particularly helpful for those who manufacture cars, boats, some electronics, furniture, appliances, or any other product where the look is almost as important as the functionality.
Faster Production
The process of making metal parts is not as accurate as plastic injection molding. Finished metal parts may not be the right shape or have the correct dimensions. Grinding them down or heating and reshaping them requires specialized tools a skilled craftsman, and most importantly, time.
Plastic injection molded parts are manufactured more quickly than their metal counterparts, and the molding accuracy reduces further grinding or reshaping of the finished parts.
Lower Costs
Plastic parts are cheaper to manufacture and buy, and customization is easier and less expensive. To create the exact size and shape of parts you need, a manufacturer just needs to program the dimensions into the injection machine. In addition, the amount of time and money saved by reducing the need for reworking, grinding, sealant application, redesign, and product testing saves even more money.
How To Decide if Metal to Plastic Conversion Is Right for Your Company
Although it may save you time, energy, and money in the long run, the cost of converting from metal parts to plastic will be significant. You need to carefully consider if the benefits of conversion outweigh the initial costs. You can begin by following these steps:
- Find a reputable plastic injection molded parts manufacturer and pick their brains. You may even want to have them tour your facility to see firsthand what parts you need and how they will be used. They should then be able to advise you about costs, materials, and ease of conversion.
- Review the parts you want to convert for feasibility and the benefits of converting them. Look at the number of specific parts you will need and whether decreasing their weight or changing the aesthetics will be advantageous.
- Factor in special considerations. These may include sterilization procedures, strength or flexibility, or the ability to withstand extreme temperatures.
- Analyze the costs. While converting to plastic injection molded parts can be cost-effective for most applications, this is not always the case. Parts you do not need in large quantities or those already fully functional may not be a valuable investment.
Ask an Injection Molding Expert
If you are looking for a reliable, reputable manufacturer of plastic injection molded parts to help you get started, contact Crescent Industries. We are a USA-based injection molder and tool builder, and we have been meeting the needs of our clients since 1946.
Resources
https://www.plasticcomponents.com/metal-to-plastic-conversion-guide
https://www.vikingplastics.com/capabilities/metal-to-plastic-conversion/
https://www.kaysun.com/blog/top-benefits-of-plastic-injection-molding
https://info.crescentind.com/blog
Topics:
Related Articles
-
Mar 19, 2025
Top 6 Advantages of Injection Molding for Your Project
Injection molding — the process of injecting molten resin into a mold — is one of the most...
-
Feb 19, 2025
Injection Molding vs CNC Machining: Which Method to Choose?
Every year, humans produce and use countless plastic products in various shapes, sizes, and...
-
Oct 03, 2024
Injection Molding Uses: Exploring Applications Across Industries
Injection molding is one of the most versatile manufacturing processes, with a wide range of...