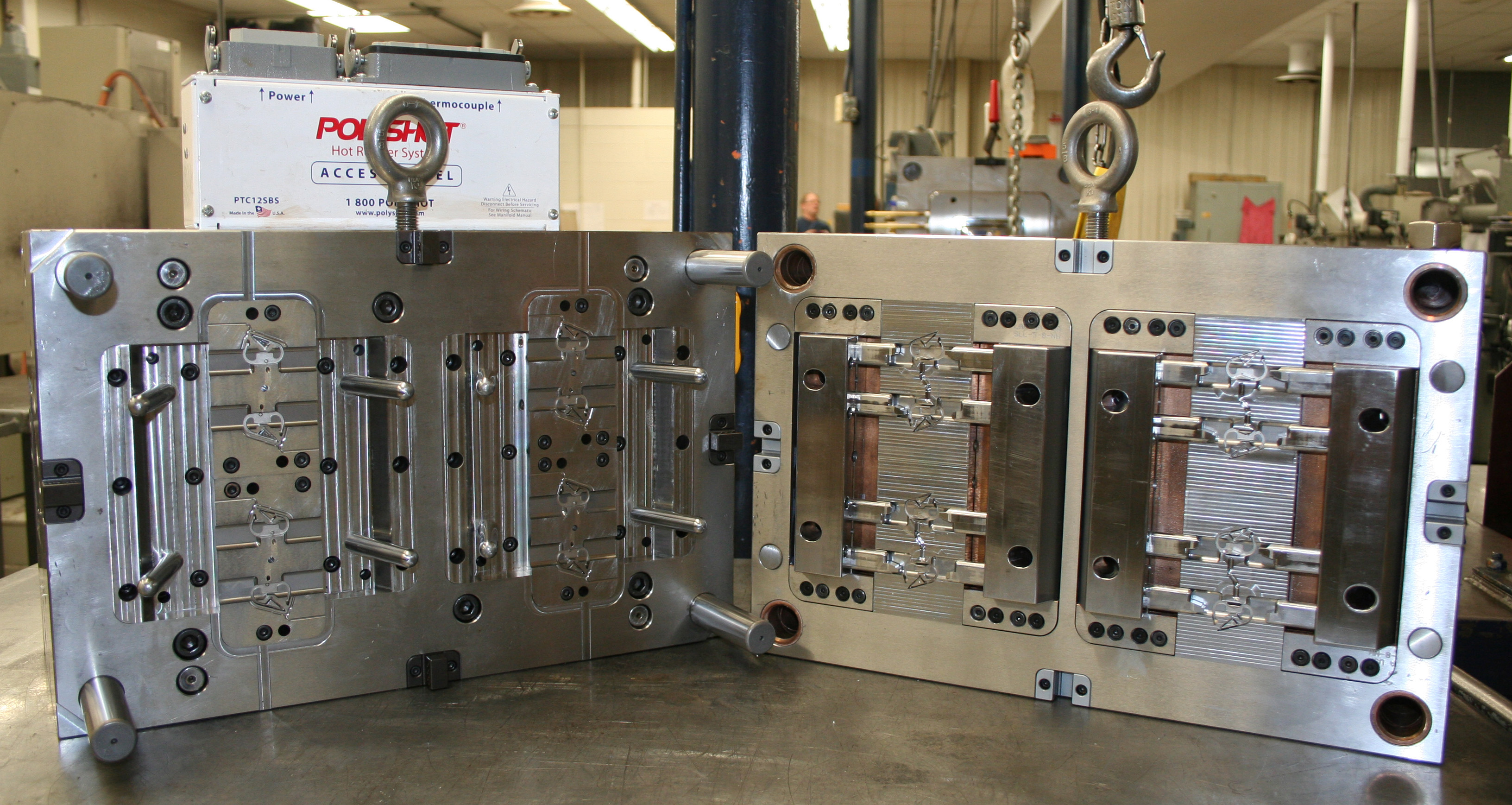
Benefits of a Single Source Solution for Your Injection Molded Project
Plastic injection molding is a complex manufacturing process. Transporting your mold or parts to different places for production and finishing can be tricky. It adds more steps to the process. Using a single-source solution for your plastic injection molding project makes things easier. It saves time and stops you from dealing with many vendors.
How Single-Source Solutions Enhance Project Outcomes
Choosing one company to manage all parts of product development helps you build a strong, long-term relationship. This partner will understand your needs from part design to completion. Some of the benefits include:
Streamlined Communication and Coordination
A big part of a supply chain manager's job is to coordinate many parts of the production network. That also means getting products from one stage to another, often at different facilities in far-flung locations. Single-source injection molding companies can eliminate many of those nodes.
When one provider manages all parts of custom injection molding, you only talk to one project lead. This cuts down the chance of miscommunication. A central point of contact works with all stakeholders, including designers, engineers, and injection molders. A unified approach and consistent communication allow you to make decisions and solve problems faster.
This close collaboration gives the injection molding supplier comprehensive insight into your project’s requirements and goals. Since they participate in every stage of the program, from mold design to production, they can identify and resolve potential issues early.
Better communication also improves project tracking and accountability. When you’re dealing with multiple vendors, it’s easy for each to shift responsibility for problems to another. With a single supplier, there’s no question about who’s responsible for what, from the start of the mold design through to mass production.
There are no misunderstandings or misaligned objectives that can cause delays or quality issues. Project management is handled in one facility for more efficient and effective project execution.
Enhanced Quality Control
Quality issues can arise at every stage of plastic molding and decisions made in one stage often affect quality in another. Single-source providers can work with you from the beginning to perfect your design for superior results. Their engineers have extensive experience with best practices for injection molding. That means they can provide feedback on your initial design and suggest modifications based on their knowledge of complex injection molding processes, such as cycle times, gate locations, mold requirements, and more.
During the production process, they can implement and enforce rigorous quality control standards consistently. This comprehensive oversight helps your plastic injection molding project adhere to predefined quality standards to minimize the risk of defects and inconsistencies.
If there are quality control issues, they can be quickly traced back to their source so you can resolve them and prevent a recurrence. This end-to-end approach to quality control contributes to better project outcomes and long-term success.
Cost and Time Efficiency
You’ll also save time and money by choosing a single-source solution. Consolidating all aspects of the injection molding process under one provider eliminates the need for multiple vendors and the associated administrative overhead. In addition to saving on transportation costs, you’ll save on labor expenses since you won’t have to pay for extra work involved with packing up and moving products for additional services.
With a single provider, the transition between different stages of the project happens much faster. Different teams work together to make decisions that can save time and money.
For example, your injection mold builder will work with the designer on complex designs to identify issues such as wall thickness, the injection unit, and the optimum plastic resin to give you the most cost-effective option. They can also predict which parts are likely to wear out faster, so they pre-build spare parts, saving you time in the long run.
Integrated Design and Manufacturing
When you bring a finished design to a traditional plastic injection molding supplier, they may let you know if your design needs changes to adhere to injection molding best practices. A single source provider manages both the mold design and the manufacturing processes. That means they’re designing with the manufacturing process in mind. This integrated approach reduces the risk of design flaws and production challenges.
By working with an integrated provider, you can take a more collaborative approach to product development. Design teams and manufacturing experts work closely together from the outset to find potential issues and opportunities for improvement early in the process. Eliminating silos in the design and manufacturing process allows for more innovative solutions.
Another benefit of integration is that you can iterate faster. Design changes can be quickly assessed and implemented without the delays typically associated with coordinating between separate vendors. You’ll be able to prototype, test, and refine designs faster, giving you a competitive edge and a first-mover advantage.
Simplified Supply Chain Management
The supply chain upheavals of the past few years have highlighted the importance of building a resilient supply chain.
Every supplier you add to the manufacturing process increases its complexity and expense. You have to coordinate the logistics of transporting raw materials and the injection molded plastics for finishing. You also have to track each vendor's performance and manage negotiations.
Switching to a one-stop shop for all your plastic project needs, simplifies your supply chain logistics. You’re less likely to experience delays and disruptions caused by a bottleneck in one node of your supply chain.
Single-source providers often have long-term, established relationships with their suppliers based on high-volume orders, so their contracts are likely to be prioritized. You also don’t have to pay for excess inventory and storage costs because your supplier manages all of the raw material storage.
This lean approach to supply chain management eliminates expense and effort on your part.
Your ONE-STOP for Plastic Injection Molding Projects
Crescent Industries has been an integrated, single-source supplier for over 75 years. We’ll work with you to optimize your plastic injection molding project for performance and cost-efficiency. Reach out today to learn how we can simplify all stages of the injection molding manufacturing process.
Topics:
Related Articles
-
Mar 19, 2025
Top 6 Advantages of Injection Molding for Your Project
Injection molding — the process of injecting molten resin into a mold — is one of the most...
-
Feb 19, 2025
Injection Molding vs CNC Machining: Which Method to Choose?
Every year, humans produce and use countless plastic products in various shapes, sizes, and...
-
Oct 03, 2024
Injection Molding Uses: Exploring Applications Across Industries
Injection molding is one of the most versatile manufacturing processes, with a wide range of...