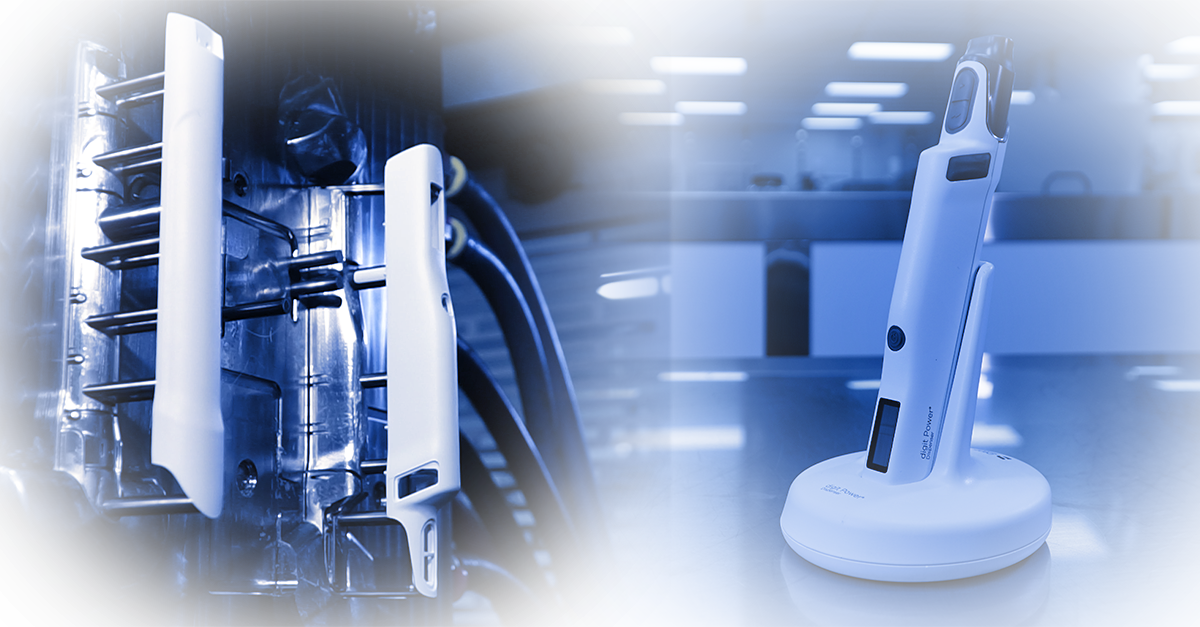
Benefits of a Plastic Medical Device Manufacturer
Reusable and single-use plastic medical devices are held to high standards of sanitation, texture, and firmness in order to be considered safe for patient examination and medical procedures. Plastic medical device manufacturers use a variety of materials, such as Polypropylene, ABS, Nylon, including medical grade resins.
Working with the right manufacturer when sourcing your medical injection molding is crucial for healthcare providers. The quality of the tools you use daily with patients can impact the quality of the care and how comfortable the patient feels in your practice.
What Are Plastic Medical Device Manufacturers?
Medical device manufacturing companies are industry professionals who specialize in the design and production of medical-grade plastic components or devices. They use a variety of plastic resins depending on the medical application of the device; for example, whether it needs to be reusable or withstand high temperatures and humidity.
By specializing in the medical field, manufacturers are able to keep up with the latest manufacturing technology, sterilization standards, and local regulations. They can also better source the manufacturing and packaging material best suited for healthcare applications.
Benefits of Working With Them
While medical suppliers can technically partner with just about any plastic injection manufacturer, working with companies that specifically offer injection molding for medical devices has numerous benefits, including:
• Cost reduction: Manufacturers with experience in injection molding medical plastics already have the machinery, infrastructure, and knowledge needed for large-scale production. This is considerably cheaper than having to fabricate a production line from scratch.
• Industry connections: By virtue of being in the medical industry, they know where to source the best material for plastic in medical applications. That way, they’re less likely to face supply chain challenges while seeking the various raw materials needed for injection molding.
• Guaranteed quality: Plastic medical device manufacturers already have an established footing in the medical molds industry and are more likely to have past and current clients who vouch for the quality of their production.
• ISO certified: With a history of producing medical devices, specialized manufacturers are more likely to be ISO Cleanroom Certified. This means they can control for airborne pollutants in the manufacturing environments, which is necessary with plastics for medical uses.
Key Factors to Consider When Partnering Up
There are a few key factors to consider before partnering up with one of the many medical injection molders on the market.
1. Experience and Expertise in Medical Device Manufacturing
Manufacturers in the medical device industry have proven experience and up-to-date knowledge of injection molding that prioritizes patient safety. This includes knowledge of the types of thermoplastic materials that are safe to use for implants and which are only suitable for single-use dipsticks.
Additionally, if you’re looking to produce new types of medical device components, the company’s experts would be able to advise you on some of the design elements and options for suitable materials.
2. Quality Assurance and Regulatory Compliance
The International Organization for Standardization (ISO) determines the quality assurance requirements for various industries around the world. This includes injection molding for medical equipment. Earning and maintaining an ISO certificate takes a lot of continuous effort on the manufacturer’s part and proves their commitment to safety and quality.
Depending on the plastic devices you’re looking to outsource, you should seek a manufacturer that has adequate certifications and complies with relevant regulatory standards. The ISO-13485 certification, for example, is for quality management, ensuring the manufacturing is able to replicate the same standards of quality for different patches of the same product.
When it comes to medical products, it’s particularly important to work with trustworthy manufacturers that won’t cut corners or compromise on material quality and production methods.
3. Technological Capabilities and Innovation
The complexity of machinery needed to manufacture plastic parts with specific medical applications isn’t available for all manufacturers. Even a manufacturer with a history in the medical industry might not have the technological capabilities needed to manufacture parts with highly specific tolerances or measurements, or the capacity for specialized processes like plastic insert molding.
Plastic insert molding is a more efficient and cost-effective iteration of traditional plastic injection molding that allows the manufacturer to create complex assemblies in a single step. Insert plastic injection molding can be used in a wide range of applications, including medical devices, so it can be useful to find a manufacturer with plastic insert molding experience.
Also, if you’re seeking long-term contract medical manufacturing services, companies that prioritize innovation make better partners. Over the last couple of years, manufacturers have begun adapting plastic injection molding to Industry 4.0. They’re also utilizing smart manufacturing with the help of the Internet of Things (IoT) to eliminate silos and make manufacturing more time- and cost-efficient.
Let Crescent Industries Help
Finding a reputable plastic injection manufacturer is already hard enough, let alone one with extensive experience and expertise in manufacturing plastics for medical applications. If you’re looking for a manufacturer that ticks all the right boxes, then give us a call at Crescent Industries.
We’re a USA-based, employee-owned plastic injection molding company with decades of experience in the healthcare industry. We serve the medical, pharmaceutical, and dental markets, among many others, and we use our advanced engineering capabilities to help you design and source the right plastic parts.
Learn more about how we can help your business by contacting us today.
Topics:
Related Articles
-
Mar 17, 2025
Labware & Diagnostic Injection Mold Building and Molding
Medical device molding requires much higher levels of precision injection molding and tolerance...
-
Jan 10, 2025
Benefits of a Plastic Medical Device Manufacturer
Reusable and single-use plastic medical devices are held to high standards of sanitation, texture,...
-
Jun 07, 2024
The Key Benefits of ISO 7 Cleanroom Standards for Injection Molding
The International Organization for Standardization (ISO) sets strict standards for the safety and...