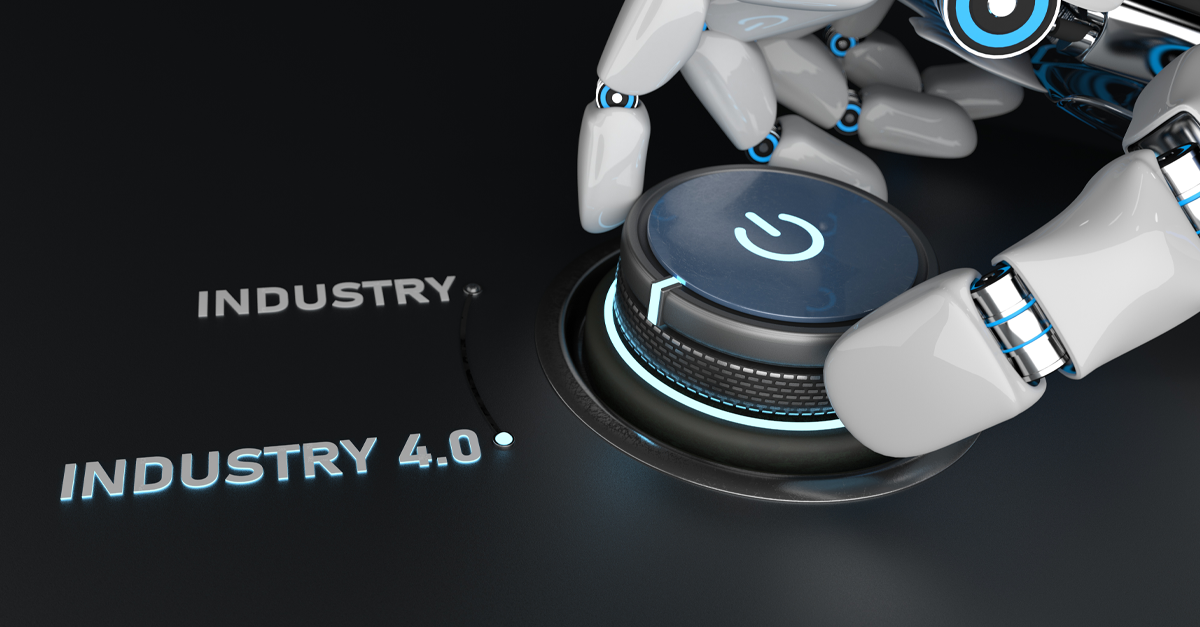
5 Benefits of Industry 4.0 in Plastic Injection Molding
Industry 4.0 is an ongoing revolution that’s seen countless new technologies changing modern industry across all sectors. In manufacturing, the impact of artificial intelligence, the Internet of Things (IoT), and other advanced tech can’t be overstated. This is true for all areas of manufacturing, and injection molding production is no exception.
Transforming Plastic Injection Molding With Industry 4.0
Plastic injection molding processes are often complex and difficult to control. The process of designing custom injection molding; implementing the solution; and optimizing quality, costs, and efficiency has many variables at play. The onset of these new Industry 4.0 injection molding technologies is changing what injection molding processes can achieve today.
1. Enhanced Efficiency and Productivity Through AutomationAutomation is among the most promising areas of Industry 4.0 technology. While automation is already widespread throughout manufacturing, Industry 4.0 lets manufacturers reach an entirely new level. It’s one area that’s seeing the most attention, with 62% of manufacturers saying they plan to invest in robotics and automation in 2023.
Already, a variety of automation solutions are improving efficiency and productivity in plastic molding. Robotic solutions can now carry out more complex physical tasks and can do so without human error. This can improve both quoted and actual cycle times for products manufactured via injection molding.
Automation in data management also serves to reduce labor requirements and improve accuracy. Instead of relying on manual data collection and management through spreadsheets, automated aggregation software collects and stores data without error. Having that data all in one place also eliminates data silos, letting teams cooperate and collaborate more easily.
2. Real-Time Monitoring and Data Analytics for Process OptimizationTraditionally, most plastic materials manufacturing processes don’t implement true real-time data. Production and quality data often rely on manual quality checks or periodic reports from manufacturing execution systems, both of which incur latency between an issue arising and when it is identified. Industry 4.0 enables real-time monitoring to avoid that problem.
Now, manufacturers can be made aware of any production issues immediately. They can act to salvage production runs, reducing waste and associated costs. Systems that compile data from all available sources in real time increase visibility across the entire injection molding process.
The wealth of data collected also delivers long-term benefits. The latest data analytics can parse out new insights from historical production data to optimize processes. They make it possible to optimize parameters such as injection speed, temperature, and more to increase the consistency of production runs.
3. Predictive Maintenance and Reduced Downtime
Maintenance has always been a major challenge in injection molding. Mold cavities naturally degrade over time until the molds must be replaced. However, replacing molds too early increases costs, and waiting too long can lead to an unplanned stop. The same general principle applies to other machines on the factory floor.
Instead of planning maintenance on a rigid schedule, Industry 4.0 now allows manufacturers to take advantage of machine learning and other technologies to achieve predictive maintenance. The system analyzes production data to determine which changes in quality, parameters, and other criteria indicate an upcoming need for mold machine maintenance.
The system goes through an initial training phase in which it learns the individual process and what to look for. Once trained, it can provide accurate recommendations for when molds and other elements require maintenance. Manufacturers can then implement these in planned maintenance stops to avoid unplanned stop events.
4. Improved Quality Control and Defect Detection
Quality is a major challenge in custom plastic molding, in particular. Potentially limited production runs for individual parts mean that teams don’t always have time to get to know the quirks of production. Industry 4.0 enables new quality control and defect detection methods to improve the level of injection molding.
Smart devices allow for the implementation of new sensors, even where space, power, and connectivity are limited. These can go beyond basic metrics such as weight measurement to include acoustic sensors, visual inspection, and other modern quality control methods.
These technologies increase the range of defects that can be detected during quality control. They can reduce the extent of human inspection needed, shrinking costs significantly. Increased accuracy means that fewer defective parts make it through, boosting the reliability of end-use applications.
Having these quality control tools available in real time can provide considerable benefits for injection molding processes. Automated alerts can let production teams know as soon as quality starts to drift, rather than them finding out about it after hundreds or thousands more faulty parts have been manufactured.
5. Cost Reduction and Waste Minimization Through Smart Manufacturing
Manufacturers face more pressure to reduce waste today than ever before. There’s no industry where this is more acute than plastics manufacturing. Reducing waste on the factory floor is one of the most important tasks for any plastics manufacturing operation, for both sustainability and cost.
Faulty production is among the most significant sources of waste, and Industry 4.0 provides a variety of options for tackling this issue. The use of artificial intelligence in production control is especially promising and could dramatically reduce waste.
Artificial intelligence and machine learning can develop an understanding of processes that enable improved control. While quality criteria will still follow a normal distribution with some defects, these technologies allow for tighter tolerances that mean less wasted production.
To achieve this, a variety of classification algorithms draw insights from production data. Artificial intelligence finds connections in large datasets that people can’t, allowing the system to classify production in new ways. The result is a plastic injection molding process that minimizes waste to reduce costs and improve environmental impact.
Harness the Power of Industry 4.0 in Injection Molding With Crescent Industries
Industry 4.0 injection molding has already changed the way we see plastics production today, and your organization can take advantage of everything it has to offer. The team at Crescent Industries maintains the latest smart production methods to provide our customers with the best quality, cost, and efficiency. For modern plastic injection molding solutions, contact us today.
Topics:
Related Articles
-
Mar 19, 2025
Top 6 Advantages of Injection Molding for Your Project
Injection molding — the process of injecting molten resin into a mold — is one of the most...
-
Feb 19, 2025
Injection Molding vs CNC Machining: Which Method to Choose?
Every year, humans produce and use countless plastic products in various shapes, sizes, and...
-
Oct 03, 2024
Injection Molding Uses: Exploring Applications Across Industries
Injection molding is one of the most versatile manufacturing processes, with a wide range of...