Automation Case Study
WINNING DIAGNOSTIC PLATE BUSINESS BY DELIVERING A CUSTOM AUTOMATED INJECTION MOLDING SOLUTION
Our customer wanted to achieve two goals reduce labor and guarantee quality parts for 19 different diagnostic plates with varying internal geometries.
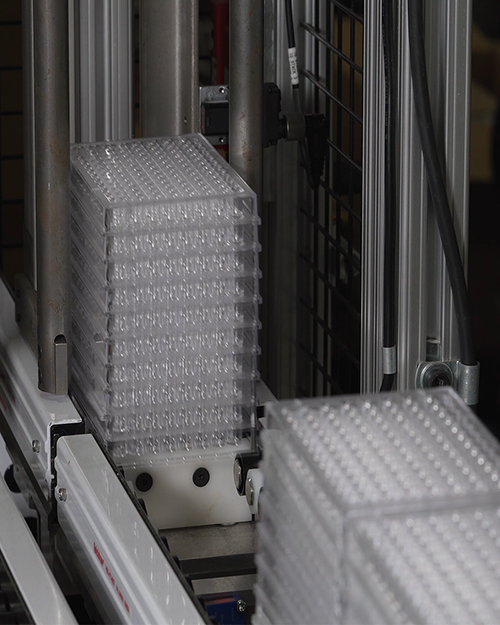
-
Crescent's In-House Automation Team Created the Solution!
The injection mold transfer included four molds producing 19 different diagnostic plates. The tools have four cavities with varying internal geometry. The external parts dimensions are common, allowing us to design automation to handle any plate configuration within the project.
Our automation team developed a plan to automate portions of the process with the goal in mind to reduce labor and assure quality. The strategy involved picking the parts and runner from the mold and handing them off to another automation cell to inspect and stack the parts for the final packing. Our ROI analysis was favorable, so we proceeded with the project. -
Customer Goals Achieved
Reaching a very low reject rate due to the reduced handling and maintaining part separation until building the stack.
-
Our Solution
The conveyor delivers the oriented plates to an injection station in our automation cell. Here we use a telecentric camera lens to inspect the parts for visual defects. If any defects are detected, the part is conveyed into a reject bin. Once a plate meets the visual criteria, it is conveyed to an up-stacker programmed for the proper stack height required for that particular part number. The completed stacks of parts are distributed onto three separate accumulating conveyors where the operator will periodically unload the stacks for packaging. The operator is responsible for bagging and boxing the final package.
We started by designing and building End-of-Arm-Tools (EOAT) for each of the four molds. We use a quick change feature for each EOAT, allowing easy and accurate switching back and forth during mold changes. The EOAT is controlled by a 3-axis press robot that picks the plates and runner from the mold while allowing the press to keep running in automatic mode. After picking the plates from the mold, the press closes and continues producing the next shot. Next, the press robot places the runner into a grinder. Next, the press robot orients the plates and places them onto a conveyor in a single file. Once complete, the press robot returns to its home position, ready to pick and place the next shot.
Why Choose Crescent?
Discover the countless benefits of partnering with us for all your injection molding manufacturing needs and let us show you why we are the perfect match for your business.